Welcome to the Onshape forum! Ask questions and join in the discussions about everything Onshape.
First time visiting? Here are some places to start:- Looking for a certain topic? Check out the categories filter or use Search (upper right).
- Need support? Ask a question to our Community Support category.
- Please submit support tickets for bugs but you can request improvements in the Product Feedback category.
- Be respectful, on topic and if you see a problem, Flag it.
If you would like to contact our Community Manager personally, feel free to send a private message or an email.
Cannot get smooth loft
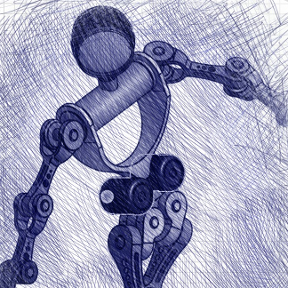
Second post on this topic. I modeled the hull of a boat using the loft feature. For this, I sketched the boat outline on various x, y, and z planes. The sketches on the z planes serves as profiles for the (multiple) lofts. The rest served as guides.
Getting the loft to work at all was very difficult. After a lot of iteration, I got a complete outline of the hull. Trouble is... where the lofts meet, there are crests, or sharp edges, meaning that the hull is not smooth as it should be.
I tried everything I can think of to avoid these crests. I tried more guides, but too many of these created "waves" in the outline of the hull, which was as bad as the crests.
I tried the Fill feature too, but it too gave me crests at the interfaces. I tried setting tangent and curvature conditions for the profiles and guides in the lofts also, but these never seemed to work.
When all else failed, I tried importing the hull as a mesh (STL) into Blender (3-D modeling tool with tools for smoothing and organic modeling). Still, this is no better than handcarving wood, and because of the precise nature of the hull, the unavoidable imperfections in my smoothing touches leave me with as bad a hull as I started with—even if the crests are now gone.
Worse than that, I need the hull in a STEP file. My hope was that I could import the smoothed hull as an STL into OnShape and export it as a STEP file, but that is not the case. Once imported back into OnShape, the mesh can only be exported as a mesh file (which makes sense).
Would someone know how I can get a smooth hull (without undesired crests or lines)? Here is the model:
https://cad.onshape.com/documents/0aaf43f3648b10110e35b470/w/8c052db76211ac0fbd52c4f6/e/6b5ab95c376dead424bdb884
Getting the loft to work at all was very difficult. After a lot of iteration, I got a complete outline of the hull. Trouble is... where the lofts meet, there are crests, or sharp edges, meaning that the hull is not smooth as it should be.
I tried everything I can think of to avoid these crests. I tried more guides, but too many of these created "waves" in the outline of the hull, which was as bad as the crests.
I tried the Fill feature too, but it too gave me crests at the interfaces. I tried setting tangent and curvature conditions for the profiles and guides in the lofts also, but these never seemed to work.
When all else failed, I tried importing the hull as a mesh (STL) into Blender (3-D modeling tool with tools for smoothing and organic modeling). Still, this is no better than handcarving wood, and because of the precise nature of the hull, the unavoidable imperfections in my smoothing touches leave me with as bad a hull as I started with—even if the crests are now gone.
Worse than that, I need the hull in a STEP file. My hope was that I could import the smoothed hull as an STL into OnShape and export it as a STEP file, but that is not the case. Once imported back into OnShape, the mesh can only be exported as a mesh file (which makes sense).
Would someone know how I can get a smooth hull (without undesired crests or lines)? Here is the model:
https://cad.onshape.com/documents/0aaf43f3648b10110e35b470/w/8c052db76211ac0fbd52c4f6/e/6b5ab95c376dead424bdb884
0
Comments
Are there any specific areas or goals that you are looking at?
Screenshots? Markups? What can we do for you?
What I've posted in the first one was for a reason.
First, attempts to loft trough series of sections is always a bad idea, regardless of the shape's geometry. It can work only for simple, direct transitions.
You wouldn't expect the loft to succeed with elaborated shape, depicted below.
It doesn't matter how many sections I will create it won't work. Why your hull should be any different? Because it's smooth?
When we're a designing an original artifact, this is not a problem, since we're not aiming at a specific shape to achieve. We're detailing design intent by defining geometrical properties an artifact. Whatever shape we get in result will suit us.
With your restoration project, we already have the shape well defined (even executed, I would say) and the deal is to bend your imagination to find a suitable patch layout.
That's not a trivial task. Both, available toolset and our perception are limited.
Sections (stations) from a scan, were drawn only for documentation.
They won't work for MCAD as shape definitions. I think my example was illustrative enough.
Not only they won't articulate the desired shape, but equal spaces between sections are also artificial.
Apart from sections, we usually have well-imagined keel and hull's edge. On those, we base our profiles. They will serve us as guides, for a loft.
Surface passing trough profiles built on a set of curves doesn't have to match those curves. That surface most likely will slightly alter from them.
That will occur even on simplest examples.
In the picture below, we have guides with a specific shape and three profiles we would like to loft. Just before we pick guides, we can see that three sections are not enough to follow guides shape, by them self.
We can guess that 4, might be enough. The question remains, how to place them? What we know for sure, is that an equal spacing won't work.
We can add those guides, but then the software will determine the flow between profiles. There is no warranty that this flow will match part we like to recreate.
More profiles, more doubts.
With more profiles, comes another problem. Surfaces become wobbly.
From profile to profile, they will tend to oscillate.
Reason for that is simple. Spline or surface will behave like a lever, where spline point/profile will be a pivot point.
If we have multiple profiles/spline points evenly spaced, we won't see a lot.
It's enough to narrow one of the spaces to see that smallest deviation will drastically change the neighboring curvature.
It works exactly like a lever, a proportion between spaces equals the ratio of a magnitude of curvature change.
We can easily imagine it in 2D.
When extrapolated into three dimensions it's impossible to understand the consequences of any move.
Nevertheless, you can try to make it in MCAD (like Onshape), but I must warn you that you will have to compromise the fidelity of your model.
Below is a link to my model, this is how far I've managed to get:
projektowanieproduktow.wordpress.com
Michal, thank you so much for taking the time to put that model together. It looks fantastic. The ridges are gone and, to my surprise, the hull matches the plan views very closely—all with just a few profiles and guides. For sure simpler is better here.
Thanks also for the detailed explanation. I learned a few things. I could tell that my many profiles and guidelines were causing a problem, but to reduce them—it seemed before—was to settle for a hull that didn't match the plan views, even approximately.
Thanks again. I'd almost given up on the idea of getting a nice smooth hull. Now I think can get this boat to look just right.
Tony