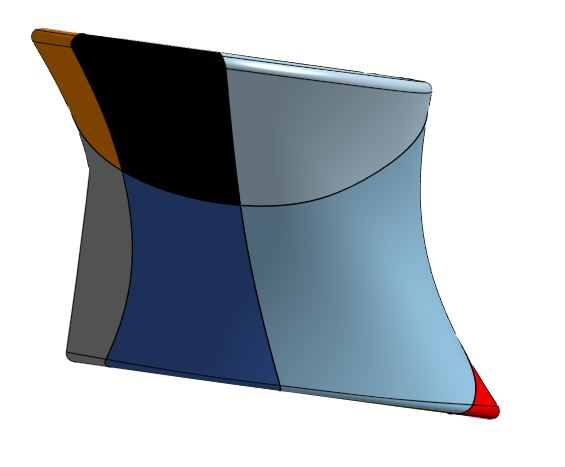
Welcome to the Onshape forum! Ask questions and join in the discussions about everything Onshape.
First time visiting? Here are some places to start:- Looking for a certain topic? Check out the categories filter or use Search (upper right).
- Need support? Ask a question to our Community Support category.
- Please submit support tickets for bugs but you can request improvements in the Product Feedback category.
- Be respectful, on topic and if you see a problem, Flag it.
If you would like to contact our Community Manager personally, feel free to send a private message or an email.
How best to replicate and re-position a rod shape many times where faces meet?
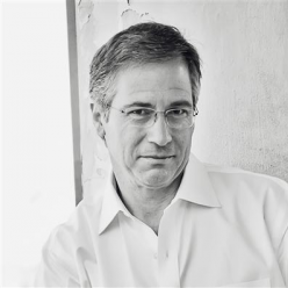
I'm going to teach a lesson showing how to create molds for casting objects too large to 3D print as a single part. The design for the part we're going to cast is here. As I write, the next step in preparing this object for printing, mold making, and eventually casting is to introduce 50mm long holes along the adjoining faces of adjacent segments so that the rods are spaced about 2 inches or so from each other. Once the segments have been 3D printed, 100mm long 3mm rods will be inserted into the holes during assembly. This full-scale assembled object will be used during the mold creation process.
My question is how best to position the rods along the faces of adjacent segments. Once all the rods are in place, I estimate ending up using about 100 rods in total, a Subtract boolean will be done with all the rods as tools and all the segments as targets.
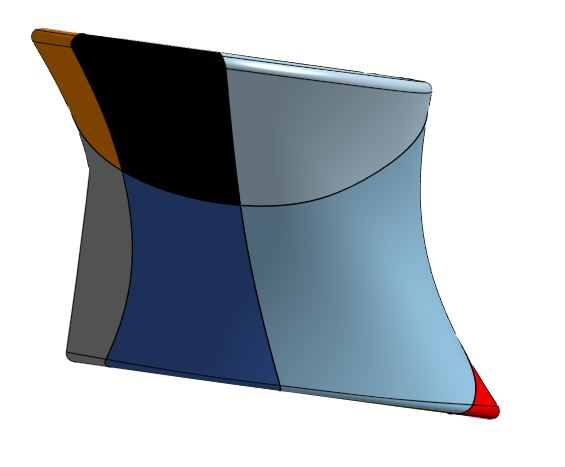
Any help will be appreciated.
- Bob
My question is how best to position the rods along the faces of adjacent segments. Once all the rods are in place, I estimate ending up using about 100 rods in total, a Subtract boolean will be done with all the rods as tools and all the segments as targets.
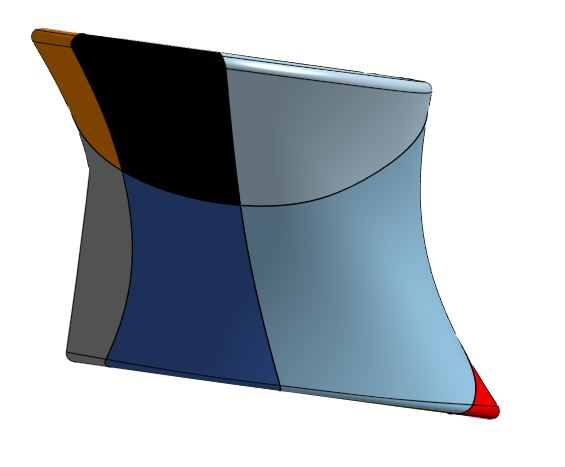
Any help will be appreciated.
- Bob
0
Best Answer
-
Cris_Bowers Member Posts: 281 PRO
I wonder if this Transform Pattern feature script would work for you
1
Answers
In the document referenced above, my desire is to position a series of rod shapes along the faces of the parts that are adjacent to each other.
My initial thought is that I could transform a single rod part using the 'Transform by mate connector' option of the Transform feature. OnShape recently introduced the ability to use ad hoc mate connectors in features. But the 'To mate connector' box of the Transform panel will only accept a single connector. If it allowed multiple connectors, then I imagined that might be able to position a single rod on each face then use the Curve Pattern tool to replicate the complete set of rods needed for my design.
I also found that the ad hoc mate connector mechanism forces connectors to snap into specific places. If you want them somewhere else you need to move and reorientate them using hardcoded values. I find this to be impractical in the majority of use cases when I think it would otherwise be handy to use ad hoc mate connectors.
At that point, I realized that there were limits at every turn - or that I wasn't imaginative enough to figure out how to replicate and position the rod parts into positions alone the adjacent faces. So I created a multitude of sketches along every adjacent face to which I manually added properly spaced circles that I would extrude to create the holes where the connecting rods would be inserted during the model-making phase of my project.
BTW, sketches have linear and circular patterns, but not curve following patterns similar to the curve pattern feature outside of sketches. My work would have been much more productive if sketches had curve-following patterns.
But after all the sketches were created, the Extrude feature generated an error when I tried to extrude all the regions in all of these sketches because the sketches weren't all on a common plane - even though I believe that my extrusion intent is unambiguous. So I ended up having to add multiple Extrude features, one for each sketch of circle profiles.
So what I'm asking in this question is whether I lack the proper level of imagination to allow OnShape to accomplish this design intention without having to resort to the multitude of manual, brut force combinatorial set of features.
Again, thanks for any help.
- Bob