Welcome to the Onshape forum! Ask questions and join in the discussions about everything Onshape.
First time visiting? Here are some places to start:- Looking for a certain topic? Check out the categories filter or use Search (upper right).
- Need support? Ask a question to our Community Support category.
- Please submit support tickets for bugs but you can request improvements in the Product Feedback category.
- Be respectful, on topic and if you see a problem, Flag it.
If you would like to contact our Community Manager personally, feel free to send a private message or an email.
Recommended practice for modifying library enclosure
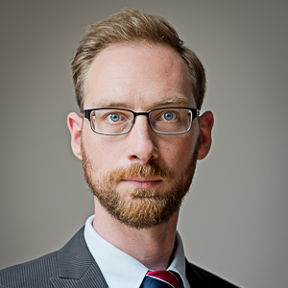
Hi,
I am trying to design an enclosure for a project using an off the shelf enclosure. I will use this enclosure range frequently, so I have already modeled it as a library component with some basic configurations. As this enclosure is already made of a number of parts, I have a parts studio and an assembly of the unmodified case.
Now I need to design the extra machining for the front and rear panels in my actual design. What is the best practice to do this? I think derive may be the appropriate method, but this only applies to each part. How do I use this within the case assembly?
Thanks in advance.
I am trying to design an enclosure for a project using an off the shelf enclosure. I will use this enclosure range frequently, so I have already modeled it as a library component with some basic configurations. As this enclosure is already made of a number of parts, I have a parts studio and an assembly of the unmodified case.
Now I need to design the extra machining for the front and rear panels in my actual design. What is the best practice to do this? I think derive may be the appropriate method, but this only applies to each part. How do I use this within the case assembly?
Thanks in advance.
0
Answers
The first thought that comes to mind is that I would have the library "assembly" enclosure modeled in the as assembled state in a part studio. Then when you want to use a modified version of it you would insert the whole part studio into an assembly studio. This brings all the parts in situated as they are assembled so you can use a group constraint. Create your in-context part studio, copy in place, make your changes and insert the changed parts back into your enclosure assembly. They will be inserted at the correct location so you can add them to the group constraint. You can then suppress or delete the original parts and release this assembly as a new part number.
The one flaw is that if you update your in-context part studio after deleting or suppressing the original parts you will break the in-context link for the copy in place.