Welcome to the Onshape forum! Ask questions and join in the discussions about everything Onshape.
First time visiting? Here are some places to start:- Looking for a certain topic? Check out the categories filter or use Search (upper right).
- Need support? Ask a question to our Community Support category.
- Please submit support tickets for bugs but you can request improvements in the Product Feedback category.
- Be respectful, on topic and if you see a problem, Flag it.
If you would like to contact our Community Manager personally, feel free to send a private message or an email.
How do I bend this tail hoop up, let's say, 10 degrees...
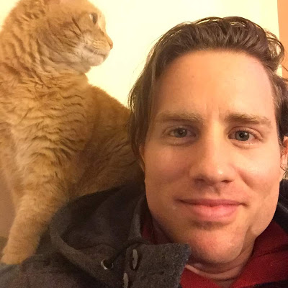
I'm trying to model this specific arear of my motorcycle frame so I can create a model in Onshape for a custom seat, seat pan, rear seat cowl, and electrical tray for under the seat with attachment points for everything. See picture at bottom of the page to see the area of focus that I'm trying to recreate.
My question: I learned how to use the sweep function and modeled the part of the frame where said items of interest live. How do I bend the rear tail hoop ~10 degrees towards the front plane? I did my darnedest to draw a scribble on my screenshot to clarify my question.
Second question: On the crossbar in the middle intersecting the origin, I had to shorten the bar "artificially" because when it was true to sketch coincident points length, the tops of the tube stuck out above the tube perpendicular that it's intersecting. Note the pink semi-circle trying to clarify what I mean of the area where it would stick out before I shortened it. Since I plan on eventually trying to build the entire frame in Onshape, is there a more fluid way to connect intersecting tubes?
-Nikolos
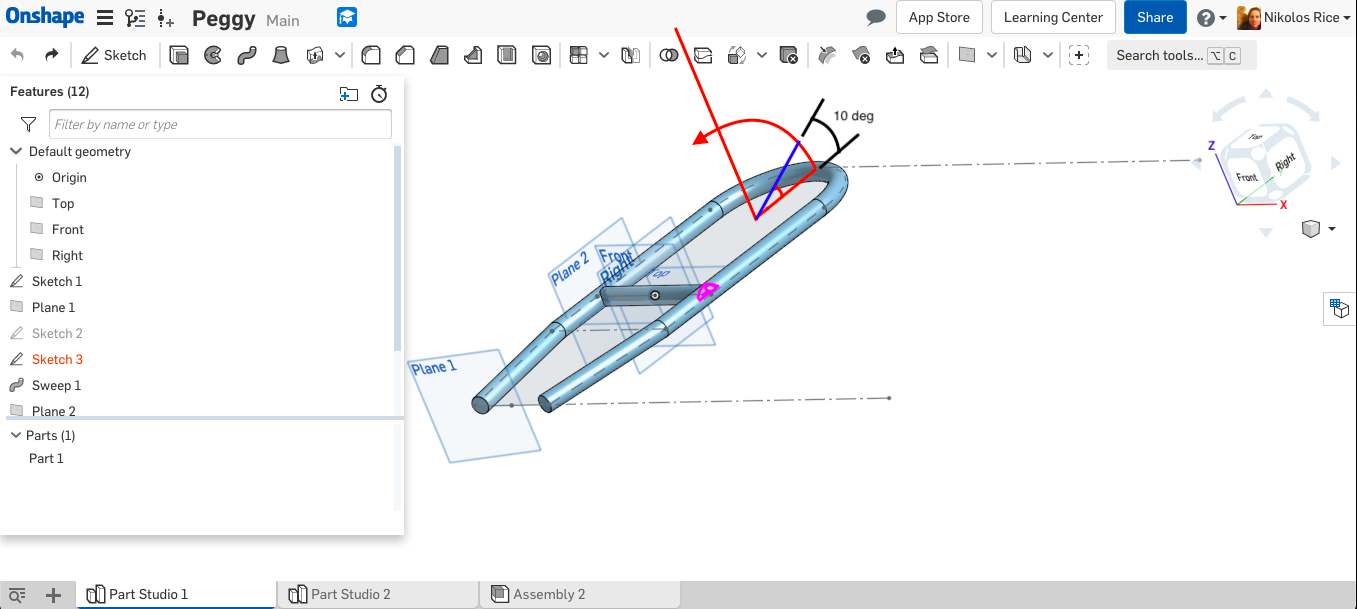
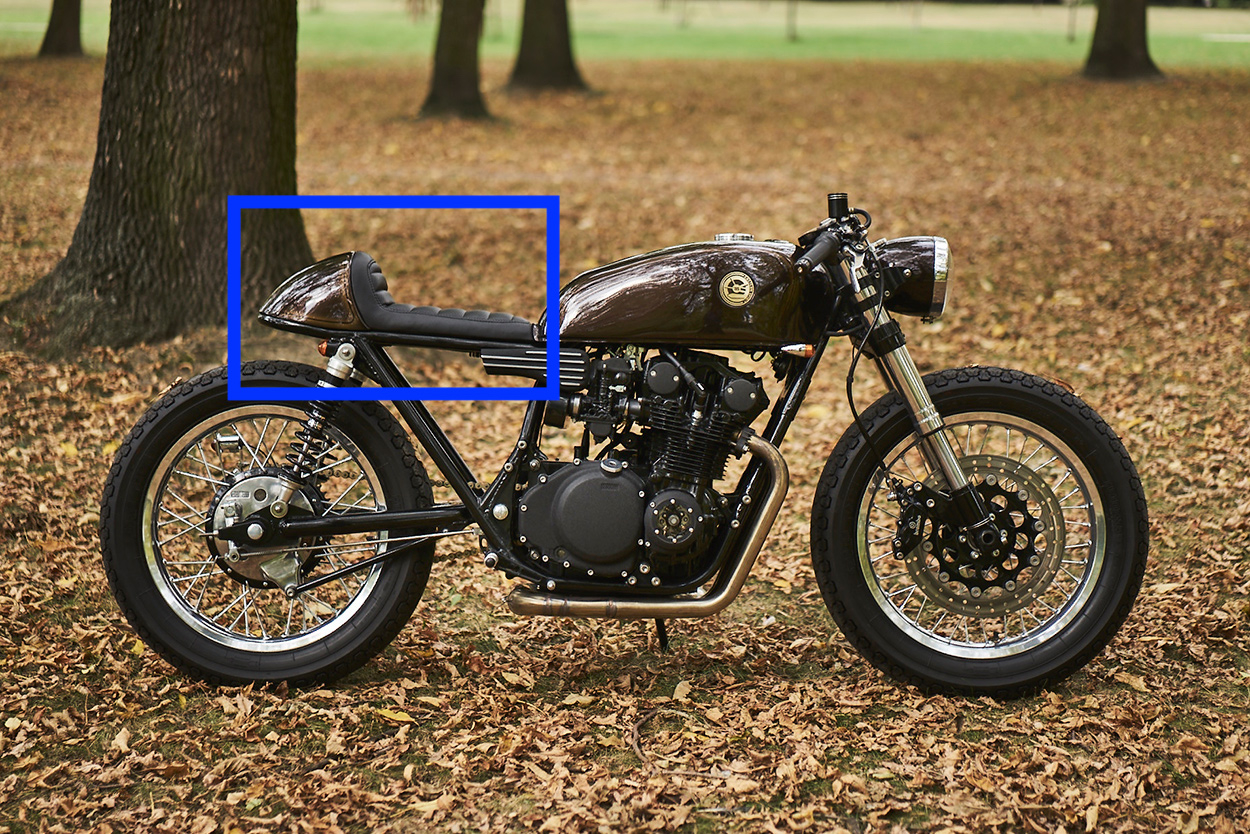
My question: I learned how to use the sweep function and modeled the part of the frame where said items of interest live. How do I bend the rear tail hoop ~10 degrees towards the front plane? I did my darnedest to draw a scribble on my screenshot to clarify my question.
Second question: On the crossbar in the middle intersecting the origin, I had to shorten the bar "artificially" because when it was true to sketch coincident points length, the tops of the tube stuck out above the tube perpendicular that it's intersecting. Note the pink semi-circle trying to clarify what I mean of the area where it would stick out before I shortened it. Since I plan on eventually trying to build the entire frame in Onshape, is there a more fluid way to connect intersecting tubes?
-Nikolos
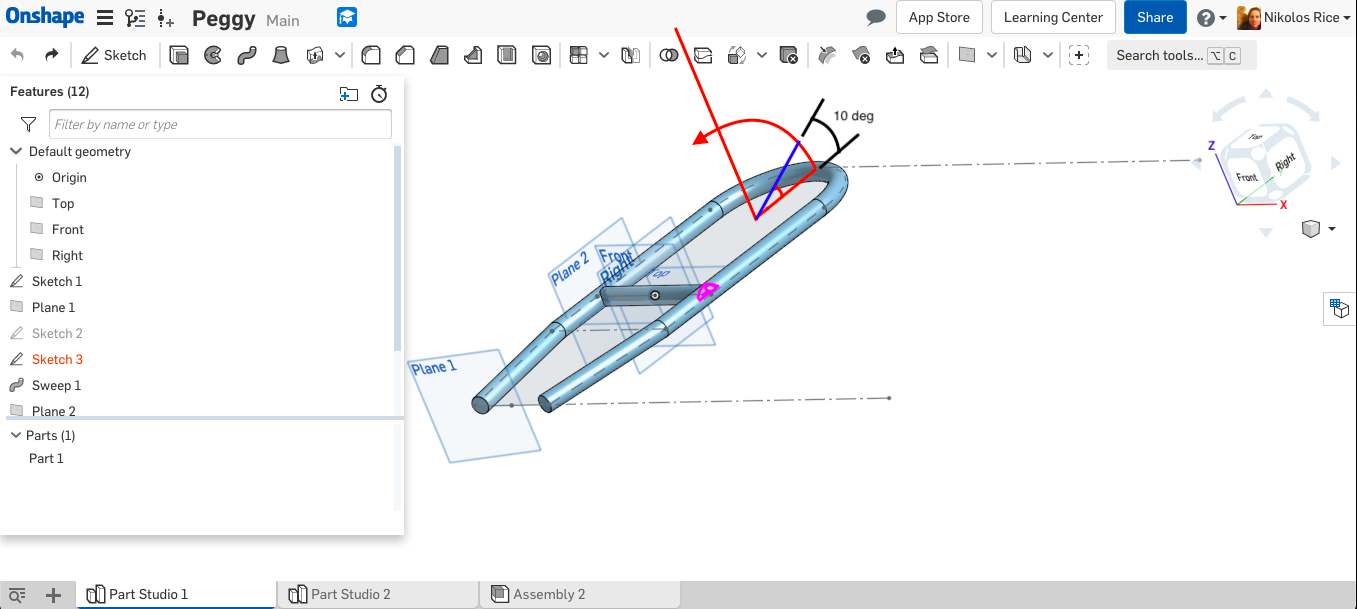
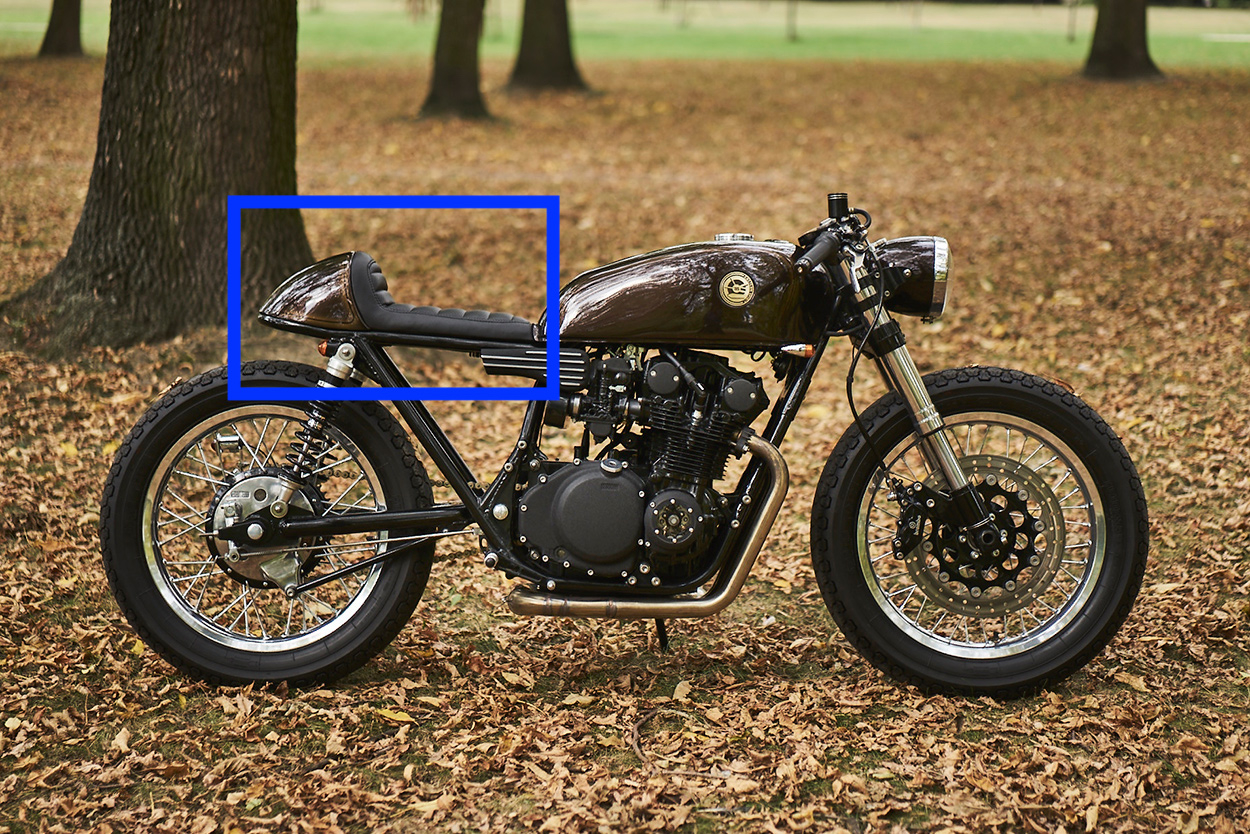
Tagged:
0
Best Answers
-
bradley_sauln Moderator, Onshape Employees, Developers Posts: 373
Here is one way to do it. The main thing is how to get that angle created.
My approach was to design the flat part of the seat/frame and stop where you'd like to bend to be made. At this stopping point, I created a line where I would create a "Line Angle" plane to design the rest. Feel free to layout the rest of the design here to reference but keep in mind this transition point.
On this new, angled plane, I designed the rest of the plane. As long as the sketch points are coincident or intersect (I did this by "Use" - ing the endpoint of the flat frame design in my second sketch) the sweep will work out.
For the true to length problem. I would use construction lines to get your true measurements but then just design the sweep path to the point of intersection. That way you can sweep the solid so it merges all the tubes correctly but then also have the flexibility to perform a second sweep to get your "as cut" geometry to reference if needed.
https://cad.onshape.com/documents/2fb1e8b1832c38c58b49b889/w/d9e51d06323c51bef3e95e72/e/24ee2c4e70be30142c4ef9e7
5 -
philip_thomas Member, Moderator, Onshape Employees, Developers Posts: 1,381
As with all things Onshape, there are 10 ways to do anything. Here is an example using the 'projected curve' method
https://cad.onshape.com/documents/f6790d1710663f6f0bc3c5b6/w/13231fa5c331d6b9843163b3/e/ed8fb5a576880e61b719bf97
Philip Thomas - Onshape5 -
mahir Member, Developers Posts: 1,316 ✭✭✭✭✭
If you want the closest approximation, it would be handy to take pictured directly from the side/above. You can then insert and scale them for reference while using @philip_thomas 's projected curve method.5
Answers
My approach was to design the flat part of the seat/frame and stop where you'd like to bend to be made. At this stopping point, I created a line where I would create a "Line Angle" plane to design the rest. Feel free to layout the rest of the design here to reference but keep in mind this transition point.
On this new, angled plane, I designed the rest of the plane. As long as the sketch points are coincident or intersect (I did this by "Use" - ing the endpoint of the flat frame design in my second sketch) the sweep will work out.
For the true to length problem. I would use construction lines to get your true measurements but then just design the sweep path to the point of intersection. That way you can sweep the solid so it merges all the tubes correctly but then also have the flexibility to perform a second sweep to get your "as cut" geometry to reference if needed.
https://cad.onshape.com/documents/2fb1e8b1832c38c58b49b889/w/d9e51d06323c51bef3e95e72/e/24ee2c4e70be30142c4ef9e7
Twitter: @bradleysauln
https://cad.onshape.com/documents/f6790d1710663f6f0bc3c5b6/w/13231fa5c331d6b9843163b3/e/ed8fb5a576880e61b719bf97