Welcome to the Onshape forum! Ask questions and join in the discussions about everything Onshape.
First time visiting? Here are some places to start:- Looking for a certain topic? Check out the categories filter or use Search (upper right).
- Need support? Ask a question to our Community Support category.
- Please submit support tickets for bugs but you can request improvements in the Product Feedback category.
- Be respectful, on topic and if you see a problem, Flag it.
If you would like to contact our Community Manager personally, feel free to send a private message or an email.
Splitting pipes based on a 3D curve, for 3D printing

Hi all!
I've just started designing some extractors for a case (mainly asthetic, and so I can learn more about creating pipes using curves in OS).
I'm looking at how I might split these up, so that I can print on a home-3d printer (200x200x200 ish build volume).
I'm starting stating at what I've called 'Extractor 1'. This is the most complex of the four.
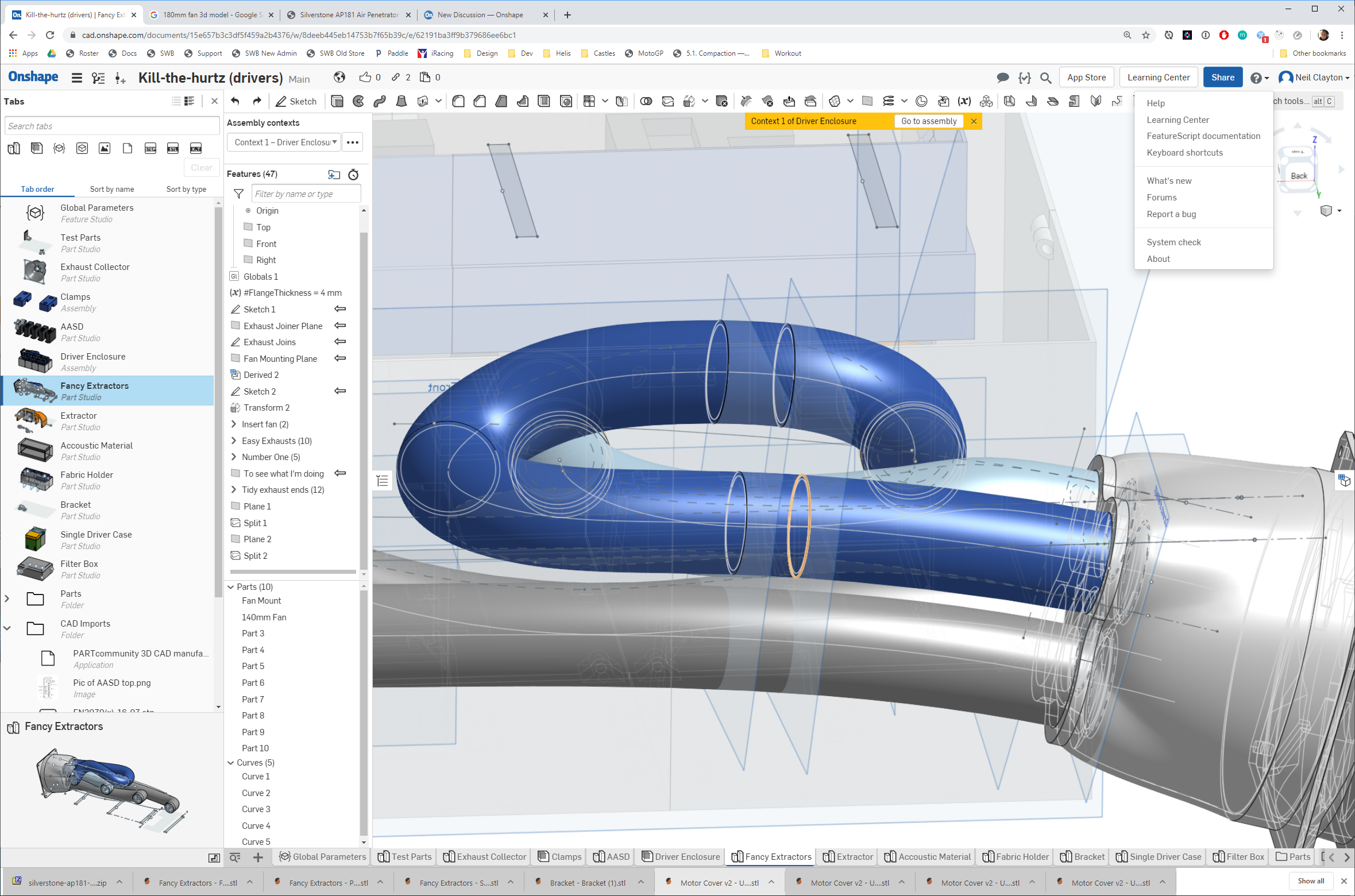
I started thinking I could use a new Plane (via Curve/Pt) to get a split in the right orientation (Plane1/Split1/Plane2/Split2 in the shot above). The 2nd one, not so sure about. I can create an offset plane from the 1st, but it's not quite in the right orientation since it's been offset, and doesn't follow the curve. I also couldn't work out how I might put additional points on the projected curve (that'd make creating the 2nd split plane same as the first). Makes me wonder if I'm going about this the wrong way.
So, here I am
Goal:
1) split the pipes into printable sections so that
2) I can add joins to each pipe so they can slide together.
Anyone got some suggestions for how I might achieve nice (perpindicular to the pipe direction) at each cut point?
And if there are suggestions for creating the slip joints; that'd be useful as well. I had intended to either loft or sweep inside the cut piece to create the inner joint but I'm not sure a sweep would work since the curve extends well beyond the two cut points I've shown above.
super thank you's in advance
URL is .... here: https://cad.onshape.com/documents/15e657b3c3df5f459a2b4376/w/8deeb445eb14753b7f65b39c/e/62191ba3ff9b379686ee6bc1
I've just started designing some extractors for a case (mainly asthetic, and so I can learn more about creating pipes using curves in OS).
I'm looking at how I might split these up, so that I can print on a home-3d printer (200x200x200 ish build volume).
I'm starting stating at what I've called 'Extractor 1'. This is the most complex of the four.
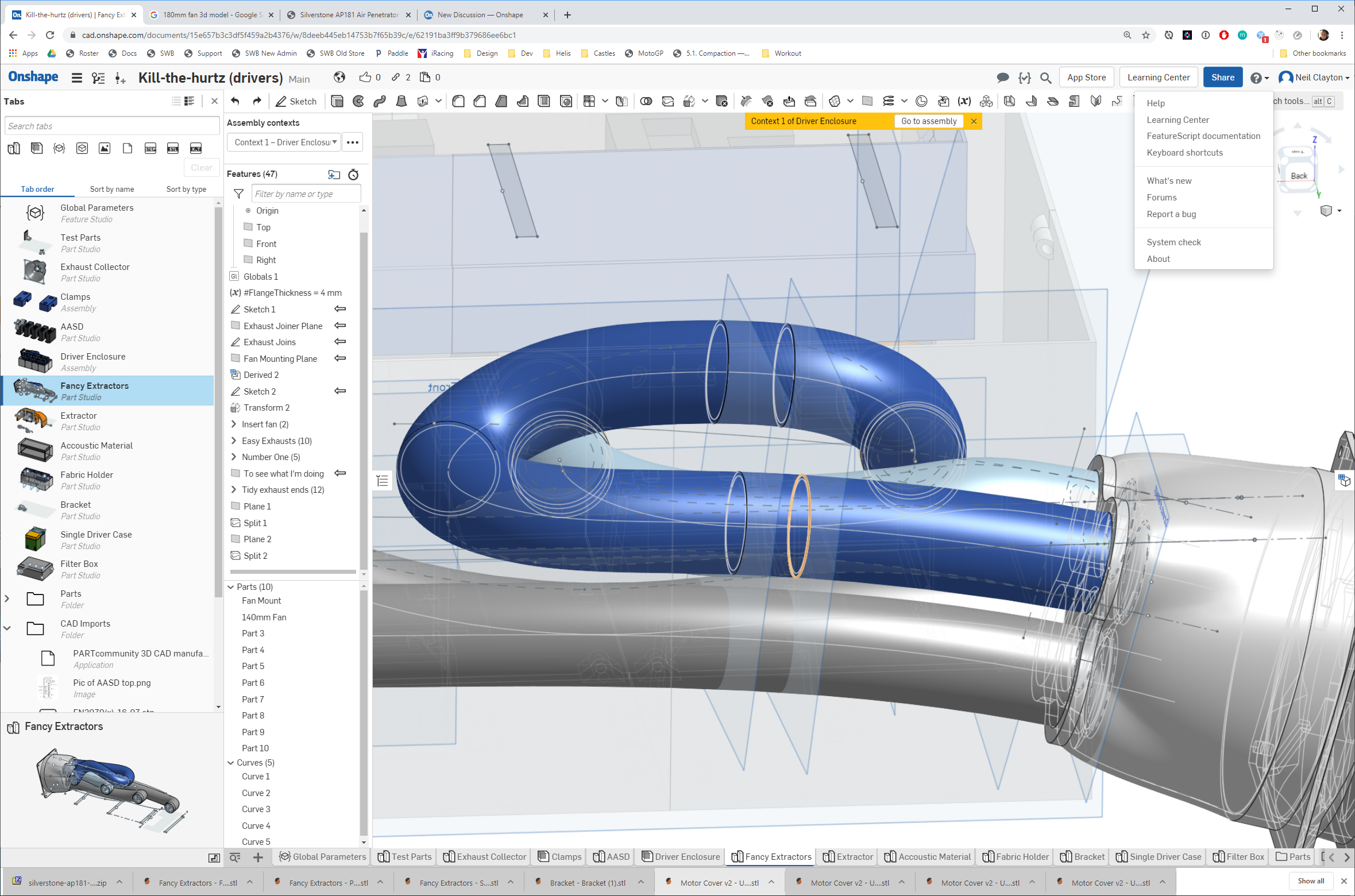
I started thinking I could use a new Plane (via Curve/Pt) to get a split in the right orientation (Plane1/Split1/Plane2/Split2 in the shot above). The 2nd one, not so sure about. I can create an offset plane from the 1st, but it's not quite in the right orientation since it's been offset, and doesn't follow the curve. I also couldn't work out how I might put additional points on the projected curve (that'd make creating the 2nd split plane same as the first). Makes me wonder if I'm going about this the wrong way.
So, here I am

Goal:
1) split the pipes into printable sections so that
2) I can add joins to each pipe so they can slide together.
Anyone got some suggestions for how I might achieve nice (perpindicular to the pipe direction) at each cut point?
And if there are suggestions for creating the slip joints; that'd be useful as well. I had intended to either loft or sweep inside the cut piece to create the inner joint but I'm not sure a sweep would work since the curve extends well beyond the two cut points I've shown above.
super thank you's in advance

URL is .... here: https://cad.onshape.com/documents/15e657b3c3df5f459a2b4376/w/8deeb445eb14753b7f65b39c/e/62191ba3ff9b379686ee6bc1
0
Comments
To create the slip joints I swept the inner circle along the path, and delete the left/right portions leaving only the bit overlapping the split. I then unioned thta and subtracted the union from the OTHER side, so as to create clearance. It works, but it's really fiddly.
I see you are creating side views and top views of all of your tubes. One option would be to split your curves in the 2D views and create a separate projected curve for each segment. This would probably require you to manually re-draw some curves, but you'd be able to more-accurately control your split points.
For the slip joints, one approach you could take is to:
- model a single split joint in another part studio (you'll probably want to add a mate connector at center "split" location). In my test model, I made the ODs of my joint a little bigger than the tube to try to avoid issues during later boolean operations, but this may not be necessary.
- derive your joint into the studio with the tubes already split.
- Then use the mate connector to position a copy of your new split joint at each of the split locations and use Boolean operations to integrate your joints with the tubes.
The downside to this approach is that the split joint would not match the curvature of each of your splits exactly. But, maybe that could be an acceptable trade-off for you.Here's my test document:
https://cad.onshape.com/documents/a4df65aaec676caa33f189ea/w/477088a56d7f1a9aad9bd3d4/e/27b19cbcd9b7c697a7c57da6
Then take the centre bit and copy it in place.
Use a thicken on the new part.
Boolean it onto one of the pipes.
Boolean the other middle part back onto the other pipe.
(We should now have just the two pipes and they should overlap where the join is with one being thicker than the other.)
Finally Boolean one from the other with the keep tools option checked, and an offset face set to around 0.2mm to give a bit of tolerance to the fit.
HWM-Water Ltd
HWM-Water Ltd
I'm deciding where to split by eye, based on print volume and where the pipe is 'straightest', in most cases.
I ended up making a couple of sketches facing the curves, that container linear patterns of points. This allowed me to use the curve point a bit more effectively, and from there using the same idea as owen suggested.
Thanks for the help, it's nice to know I'm on the right track.
It'd be great for this case to be able to "pull" and push 3d vertices around, but I get that's not very parametric and quite likely not at the top of anyones list