Welcome to the Onshape forum! Ask questions and join in the discussions about everything Onshape.
First time visiting? Here are some places to start:- Looking for a certain topic? Check out the categories filter or use Search (upper right).
- Need support? Ask a question to our Community Support category.
- Please submit support tickets for bugs but you can request improvements in the Product Feedback category.
- Be respectful, on topic and if you see a problem, Flag it.
If you would like to contact our Community Manager personally, feel free to send a private message or an email.
CAD philosophy: Add or Subtract?
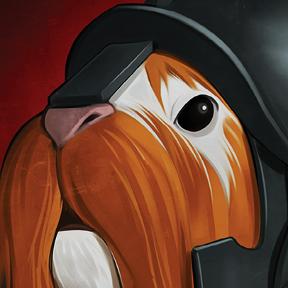
in General
Back in't day when 1gb of ram were more than tha'd need to run t'3D modelling package..(nostaga eh.. Anyway enough of typing in a bad northern accent)
I was always taught to model as if manufacturing... Start with the solid bar or block and take out your cuts, thinking about the machining process as you go.. As I've been out of CAD for a while before wandering back is this, given changes and advances in CAD, still a way to think about creating 3D models?
I ask because a lot of public models I've looked at start small and add extrusions etc on to produce the finished article.
Is this a better way to model??
Which way would produce a more robust model in terms of later edits, or is that dependent on something else entrely?
Any thoughts?
I was always taught to model as if manufacturing... Start with the solid bar or block and take out your cuts, thinking about the machining process as you go.. As I've been out of CAD for a while before wandering back is this, given changes and advances in CAD, still a way to think about creating 3D models?
I ask because a lot of public models I've looked at start small and add extrusions etc on to produce the finished article.
Is this a better way to model??
Which way would produce a more robust model in terms of later edits, or is that dependent on something else entrely?
Any thoughts?
Tagged:
0
Comments
I would say the best way to model is to make each step as uncomplicated and clear in intent as possible. In my opinion, it is best to have many simple, atomic steps that are easy to understand and change, rather than to have more complex and/or roundabout ones that more closely match the manufacturing process. However, the parts I design are mostly 3D printed, so I don't have many manufacturing constraints, and the process itself is not very "CAD-able," so please take this with a grain of salt.
Here are some examples of parts I designed for 3D printing. They don't always follow best practices, but might give you some ideas for when to use which extrude type:
https://cad.onshape.com/documents/979b91b2637f973de43dff83/v/d485743dad3eb77833f1fa9d/e/b4d167b4e0d2d449a92d4eac
https://cad.onshape.com/documents/dc7356dbbee6423ee7b91054/v/6e388e66f8153d2f0efcc377/e/eba6cd3f4bf529411209433c
https://cad.onshape.com/documents/213322230ca24e7ace62142a/v/99c5db7d58f66f03671a3c4c/e/916cfc1f57c7975f9ffb5368
Another thing you can do on more high stakes models is name each of the features to help clarify the intent behind what it's doing. For example, "lightening profile sketch," "lightening profile extrude," "mounting pattern layout," "mounting pattern hole," etc.
Of course, I'm no professional (still just a student), so it's possible none of this applies to your situation! Just my two cents.
@alnis is my personal account. @alnis_ptc is my official PTC account.
Just looking at one of the simpler parts there, the REV Hub Mount, I'd have done it completely differently!
I think I'd have had three separate sketches, one for the plate, and one for each set of holes!
A separate thing for each machining operation.
Possibly all dimensioned from a corner...
https://cad.onshape.com/documents/80f2af2747b90a04aeb200de/w/222d58bb8e0d79fa67c4301a/e/30ec4b6d0855c87683539443
The original and my take on it. The first is built up, mine cut down... the same result...but which is 'best'
This what set me thinking about this as the original here: https://cad.onshape.com/documents/54da0f97214591eff2d0163a/w/ad510a2cdb52e46bd7378b70/e/ca3d1e827171d557a085b62a
would be impossible to make traditionally.
You say you don't always follow best practice....what is current best practice? Just trying to work out whats the best way to teach my students!
Creative design, where you don't quite see the full intent at the outset, doesn't lend itself to this approach though. In the case where I don't have a clear enough intent, I'll start with a 'first draft' model where I'll try things out, test them in an assembly, and get a rough idea of how things should work. After 'intent' can be discerned from the draft, I begin again from the ground up to make a 'production ready' model with a more appropriate feature tree. For many design projects, discovering a good approach is half the work, so starting the model over isn't really beginning all over again, more like taking a step back for a giant leap forward.
In all cases, best practice is to rename features and parts (not just part studios) appropriate to their purpose. If you are sketching a path for a sweep that will form a handle, rename it to "handle sweep path" and name the sweep feature to "handle" or some such thing. Name holes according to their use ("Mounting Bracket Hole pattern" etc.). It saves hours of time when you (or another draftsman) come back to a project after it has sat for a while, be it weeks or years. Named variables should have descriptive names, not "x" and "y" unless actually driven by a Cartesian formula. Naming is doubly important when using configurations.
Fill out the part property fields too, especially the description. Do not just describe a screw as "Screw #10" - describe the thread size, length, head type, drive, grade, and coating.
@alnis is my personal account. @alnis_ptc is my official PTC account.
A few thoughts come to mind for me on this subject (written as I'd try to explain it to an engineering student):
- Separate the concepts of "designing" and "modeling". Designing is the process of figuring out and documenting what you want to build. Making sure your part can be easily manufactured is definitely a part of design and can't be overlooked. In contrast, "modeling" is one way to capture or document your design. So much of actual design is done outside of CAD, so I think its important to separate these concepts.
- With #1 in mind, I think the best way to think about "modeling" is capturing your design intent in a clear, parametric way (i.e. driven by variables and relationships). Does your design require equally spaced holes? Does it required a 10mm clearance between two faces? Does your design require a feature to be symmetric? Those are the important things to capture in your model. Whether you decide to add or subtract material should be based on your answers to the those questions. How you set up your features (cuts, extrudes, reference planes, etc.) can also be used to capture design intent - for example, you may want to extrude up to some reference point rather than hard-coding in the extrude length.
All of that said, I think the others make good points as well - keep features and sketches simple, name things appropriately so that they can be understood,The Onsherpa | Reach peak Onshape productivity
www.theonsherpa.com
Pushing in a slightly different direction to perhaps unpick my ingrained ways.. Does the fact that Onshape doesn't currently allow you to use sketch /model dimensions in the drawing mode change the way models are dimensioned... Again, back in't day on Pro Engineer I tried to create models and dimension so I didn't have to do much on the drawing. As I think someone mentioned there is easy to model and easy to manufacture and these aren't always the same, does this help as your not trying to shoehorn one into the other? And finally. Are drawings as important as they used to be or does the cad file carry more weight?
PTC Creo (the step sibling of Onshape) has this capability. Time to migrate something like it to Onshape. I would love to right click on a dimension (driving or driven) and have a selection for "Add to MBD".
Use the MBD information to create 2D or 3D drawings.
So, I think the answer to your first question is "No". Whether dimensions/annotations are defined in the 3D model or in a 2D drawing environment doesn't have much impact on things. Either way, the goal of modeling should be to create a model that reflects design intent. The goal of dimensioning should be effectively communicating the design so that it can be manufactured and inspected (in addition to calling out non-tangible things like tolerances).
Regarding importance of 2D drawings - I think its a mixed bag, but more and more things are starting to make 2D drawings less necessary. Most of the things I make have complex, organic shapes that aren't easily dimensioned in a 2D drawing (an many are 3D printed). So in our case, the 3D model is absolutely required for manufacturing, but the 2D drawing is still used for documentation of other specifications, inspection criteria, and other relevant information.
Additive vs subtractive modeling is really dependent on what's easiest to model, not the manufacturing process. One thing to keep in mind, is that the more extra surfaces and shapes that get created and then cut away, the more extra work your CAD system is doing to regenerate the model. I've also seen additive models where people copy complex surfaces and then use them to create another solid which gets boolean-added to the previous. Any time your CAD system has to compute the boolean result with two coincident complex surfaces, it can take a lot of extra time.
Simon Gatrall | Staff Mechanical Engineer | Carbon, Inc.