Welcome to the Onshape forum! Ask questions and join in the discussions about everything Onshape.
First time visiting? Here are some places to start:- Looking for a certain topic? Check out the categories filter or use Search (upper right).
- Need support? Ask a question to our Community Support category.
- Please submit support tickets for bugs but you can request improvements in the Product Feedback category.
- Be respectful, on topic and if you see a problem, Flag it.
If you would like to contact our Community Manager personally, feel free to send a private message or an email.
Offset Mate in assembly by Z axis in postive direction requires negative value
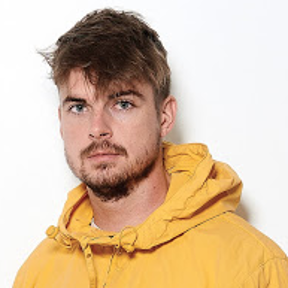
Hi just trying to understand the behaviour,
I have two mate connectors aligned with Z up as to global origin using a fastened mate when I input an offset I(I am desiring they move away from one another which is a positive value in terms of XYZ to global orientation) it requires me to enter a negative value.
Could someone explain the reasoning to this? Cheers
0
Answers
Applying an offset should be viewed as moving the second mate connector from the first mate connector by the offset amount in the direction you specify the offset for.
and I find that if I have 8 parts in total 4 of two different types and the mate connectors are all the same setup for each part as they are just a copy paste that sometimes i have to enter a positive value and sometimes a negative it changes randomly.