Welcome to the Onshape forum! Ask questions and join in the discussions about everything Onshape.
First time visiting? Here are some places to start:- Looking for a certain topic? Check out the categories filter or use Search (upper right).
- Need support? Ask a question to our Community Support category.
- Please submit support tickets for bugs but you can request improvements in the Product Feedback category.
- Be respectful, on topic and if you see a problem, Flag it.
If you would like to contact our Community Manager personally, feel free to send a private message or an email.
Face Shield Model
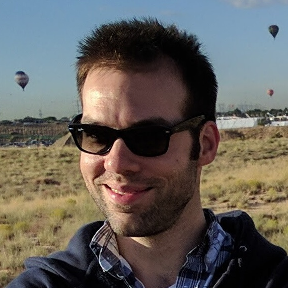
Hey all! I realized I never posted this here:

https://cad.onshape.com/documents/3eb48dd2e897742bfd684ccd/v/e104c3a0953f7996ac8c7787/e/f88ff88aa0fe388898bb902b
I designed and created a reusable, serviceable face shield a few months ago. It can be cut on a CNC using HDPE and some thin polycarbonate sheet. The whole design is meant to be serviceable so one can break it down, clean it, replace parts and keep them in service.
If anyone wants to make some of these go for it. I've been donating them to people that I know that need them.

https://cad.onshape.com/documents/3eb48dd2e897742bfd684ccd/v/e104c3a0953f7996ac8c7787/e/f88ff88aa0fe388898bb902b
I designed and created a reusable, serviceable face shield a few months ago. It can be cut on a CNC using HDPE and some thin polycarbonate sheet. The whole design is meant to be serviceable so one can break it down, clean it, replace parts and keep them in service.
If anyone wants to make some of these go for it. I've been donating them to people that I know that need them.
2
Comments
That's a good tip for sure. In this particular model the tool enters and exits at pretty good angles so there's not too much of a slowdown when you're in the corners. I had pretty good luck cutting runs of these pretty aggressively. The hardest thing is hold down!
I think a 1/4" bit is the best compromise of detail and speed. Although I've seen people use 1/8" bits at full depth through this stuff with good success...