Welcome to the Onshape forum! Ask questions and join in the discussions about everything Onshape.
First time visiting? Here are some places to start:- Looking for a certain topic? Check out the categories filter or use Search (upper right).
- Need support? Ask a question to our Community Support category.
- Please submit support tickets for bugs but you can request improvements in the Product Feedback category.
- Be respectful, on topic and if you see a problem, Flag it.
If you would like to contact our Community Manager personally, feel free to send a private message or an email.
Multi-body surfacing tactics/strategy
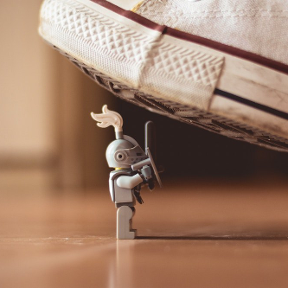
Hi all!
I'm on the verge of setting up a 'clean' model of a product we're developing and I'm trying to decide on a robust, efficient modeling strategy.
I tried finding info on modeling strategies/general guidelines/resilient modeling, but so far have not found much information specifically for Onshape. Hoping to get some input from the great hive mind 

The sub-assembly I'm focusing on can be compared to a computer mouse; three parts (lets assume; body, left mouse button (symmetrical to RMB) and scroll-wheel) that share surface continuity. Let's also assume there is some grip texture on the buttons which needs to be the same on the body:
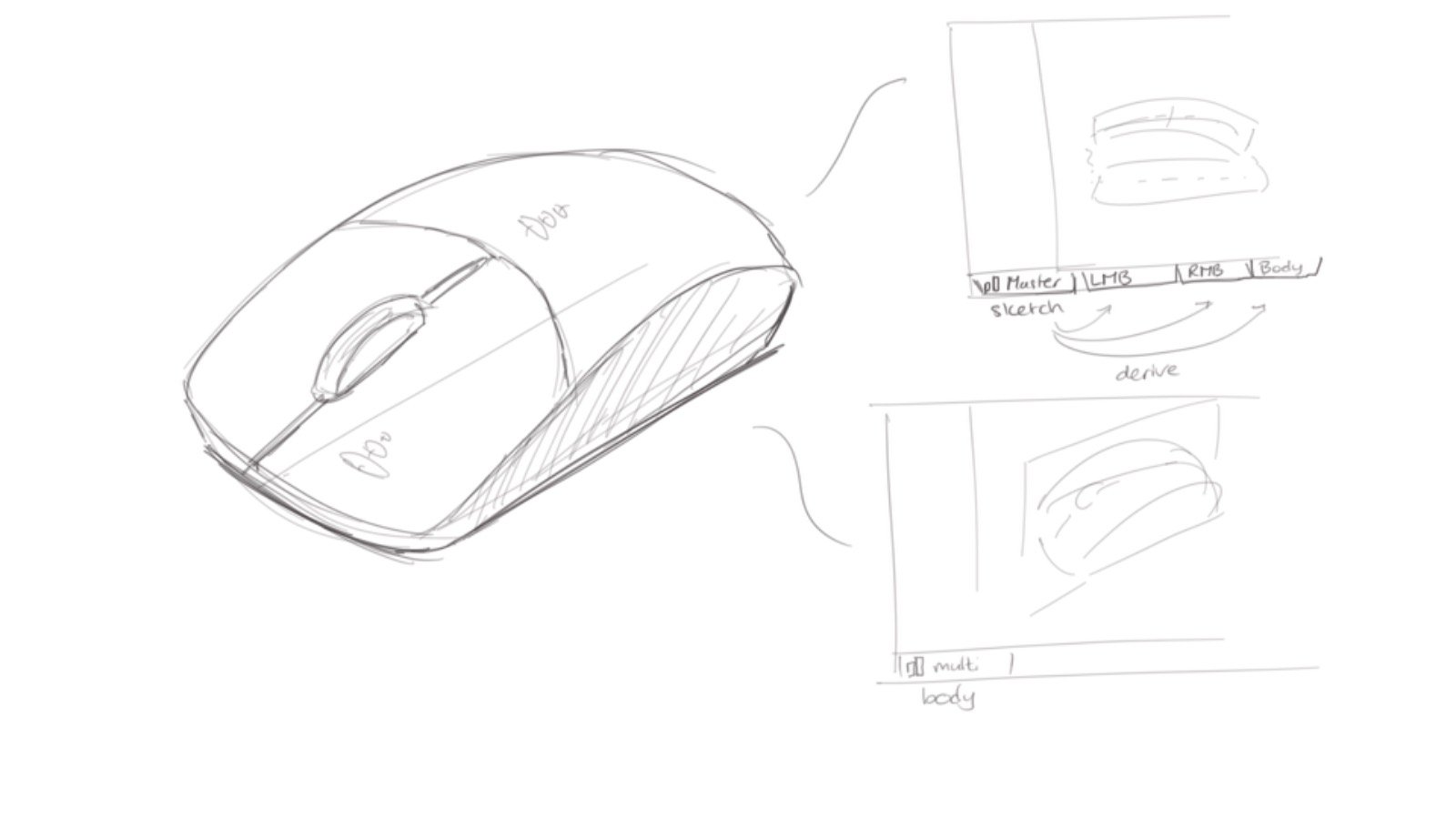
The goals to achieve and things to consider with the clean model are;
- Be able to quickly output several sizes of the product.
This should take into account that for example, a mouse button will become shorter and narrower, but its overall thickness stays the same for manufacturability.
- Eliminate errors and failing features.
Our models are a hodge-podge of features resulting from an elaborate prototyping and testing phase. This has created unstable surfaces/features which unexpectedly break down. I want to prevent errors in say, the mouse button, causing errors in the body.
- Capture design intent.
Models can get individual revisions, but stick to overall shape. So there's curvature continuity between mouse button and body. Also, say the grip texture is adjusted, it should be updated on both the mouse button and the body.
- Speeeeeed
Who doesnt? :P
But we also use these parts to create Tooling. Currently we Derive the part from its Functional design Document into a new Manufacturing design Document. Getting a short regeneration time on this Derive is a huge bonus.
I'm thinking of two approaches:
1) Setup a Master sketch/studio with all Sketches/Reference planes etc. in one Part Studio. Then import and use accordingly for each part in their respective Part Studios.
Pros:
- Each Part has its separate Part Studio, minimizing risk of one part failing leading to all parts failing.
- Can just Derive the one part we need for Manufacturing.
- Master sketch contains the features which should be the same across parts.
Cons:
- There's probably a ton of reference features in the Master sketch document..
2) Have one massive Part Studio using Multi-Body modeling.
Pros:
- There are quite intricate mating surfaces between the parts, next to the shared surface continuity
- Clearly visible that similar features share similar dimensions (grip texture)
Cons:
- Loooooootts of features
- Deriving to tooling will import all Parts, then deleting the ones not needed for Derive (see Turbocharging Onshape). Causes increased regeneration times.
Looking forward to input/advice, tips&tricks, whatever you feel like sharing 

1
Comments
I'm curious to see if others have experience with approach 1, but it just seems so much easier to control design intent, and consistency with approach #2.
If you judge your part complexity to be pushing your luck working in one studio, then some kind of Master Model approach is good. I often end up splitting the difference between workflow 1 and workflow 2. You don't have to go all-in with either. I'll model in a multi-part Master Studio, but am careful to only include features that define the part's interactions (over-all form, joints, screw bosses, surface transitions etc), but wouldn't include all of the details that only impact one part (fillets, label recesses, textures, stiffening ribs, hole patterns, etc). If I can only model half or a quarter of the model in the Master Studio, even better. The derivative studios can have a few parts too if that makes sense for the project. There's no rule about "one part per studio". Having a few parts in a studio does get you some efficiencies in the ability to fillet and mirror multiple parts at once. Once the Master Studio starts to solidify, it could be worth making the derive features reference a version for performance. You mentioned wanting similar grip textures across parts. I'd delay that step for as long as possible and when it has to be done, I'd set up variables with featurescript to drive it so you can reference the variables in multiple part studios. Or if the texture is more of an identical stamp in a few places, model it in a separate studio and use Super Derive to add it where you need it.
The Onsherpa | Reach peak Onshape productivity
www.theonsherpa.com
The Onsherpa | Reach peak Onshape productivity
www.theonsherpa.com
Consider making a Version of the document and Deriving the Version of the top level reference parts into the Child studios....then when you make changes to your top level design intent - you can Version & Update the children again.
For some complex interrelated Part Studios this can make a significant improvement in overall speed.
You don't get instantaneous update of downstream parts when you change the parent, but you DO get snappier performance throughout (and it's WAY faster overall than designing in-context and updating contexts, which is inexplicably slow).
I'd recommend doing this step (deriving Versions rather than Workspace parts) only after you've done most of the basic layout work...and when you shift your design time to the child Studios. That's when the document starts to slow down.
One nice thing about this workflow is that, even though you don't get live, instantaneous updates of child studios, you DO get a nice blue dot reminding you to update the Derived features.
Good luck!
Learn more about the Gospel of Christ ( Here )
CADSharp - We make custom features and integrated Onshape apps! Learn How to FeatureScript Here 🔴
The Onsherpa | Reach peak Onshape productivity
www.theonsherpa.com
Learn more about the Gospel of Christ ( Here )
CADSharp - We make custom features and integrated Onshape apps! Learn How to FeatureScript Here 🔴
The Onsherpa | Reach peak Onshape productivity
www.theonsherpa.com