Welcome to the Onshape forum! Ask questions and join in the discussions about everything Onshape.
First time visiting? Here are some places to start:- Looking for a certain topic? Check out the categories filter or use Search (upper right).
- Need support? Ask a question to our Community Support category.
- Please submit support tickets for bugs but you can request improvements in the Product Feedback category.
- Be respectful, on topic and if you see a problem, Flag it.
If you would like to contact our Community Manager personally, feel free to send a private message or an email.
CAM for sheet goods/routers, what do you want?
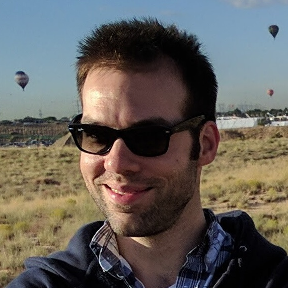
in General
Onshapers!
As you all know right now to nest/machine an Ohshape model like cabinets, sheet goods, sheet metal, etc you have to get your model out of Onshape and use a 3rd party CAM tool. If you could imagine your ideal CAM utility for Onshape what would it look like? What are some must haves, if you use another CAM tool for this sort of thing now what do you like about it, and what do you dislike about it.
Below are 3 examples of different CAD>CAM tools nesting and toolpathing complex models for sheet goods. I have my own opinions and thoughts on these, but I'm interested in hearing yours!
SketchUp/Fabber
https://youtu.be/ug3TvrJtVLQ
Fusion 360
https://youtu.be/UH3RhTTp30k
Mastercam:
https://youtu.be/ne-ZAe9GGsk
@bryan_lagrange @MichaelPascoe I know you've weighed in on other discussion threads but I'd be interested in hearing you chime in here if you can spare the time.
As you all know right now to nest/machine an Ohshape model like cabinets, sheet goods, sheet metal, etc you have to get your model out of Onshape and use a 3rd party CAM tool. If you could imagine your ideal CAM utility for Onshape what would it look like? What are some must haves, if you use another CAM tool for this sort of thing now what do you like about it, and what do you dislike about it.
Below are 3 examples of different CAD>CAM tools nesting and toolpathing complex models for sheet goods. I have my own opinions and thoughts on these, but I'm interested in hearing yours!
SketchUp/Fabber
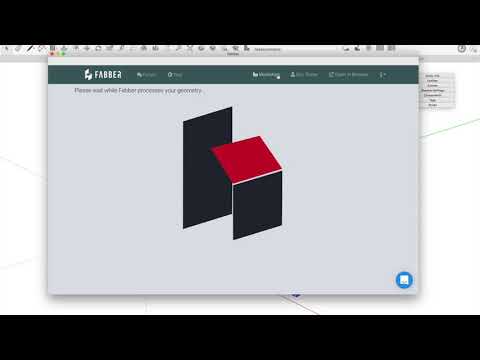
Fusion 360
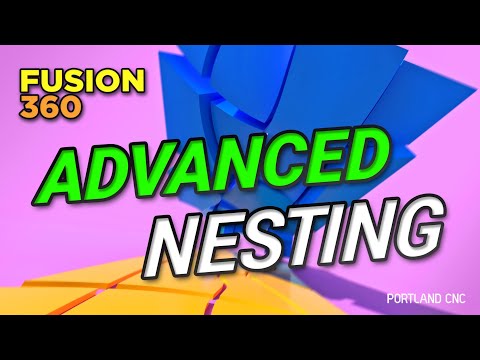
Mastercam:
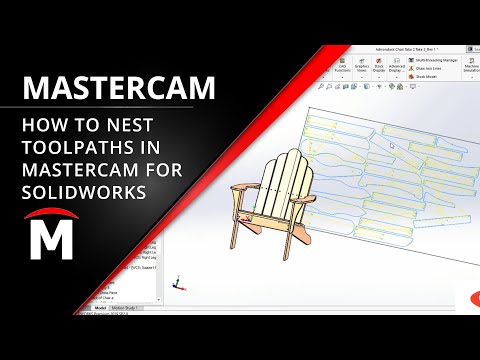
@bryan_lagrange @MichaelPascoe I know you've weighed in on other discussion threads but I'd be interested in hearing you chime in here if you can spare the time.
Tagged:
1
Comments
Onshape needs modern cam that is equally as innovative as Onshape.
As a general scope, to do this right, you will need to:
Learn more about the Gospel of Christ ( Here )
CADSharp - We make custom features and integrated Onshape apps! Learn How to FeatureScript Here 🔴
My first must-have is a tool that works within Onshape but I guess that is already in the plan
1. I would need to specify my own machine as it is home built!
2. If a project had different thickness boards, it would need to separate those out to different CNC jobs
3. For some projects, grain direction won't matter at all, but for others it will. We need to specify grain direction for the part and the material. To do this an option that says "align longest dimension of parts with board material grain" would be useful for the majority of cabinet parts but would need an override for specific parts where the longest dimension goes across the board grain. This would need somehow to be specified in Onshape or remembered by Fabber as it would be tedious and error prone to spedify every time a change was made in Onshape!
4. An ability to identify parts once cut. For some projects, this needs to be a CAD issue with a part ID engraved into the part, but for furniture, is there a better way than a board layout drawing with the part names and counts drawn on?
5. Job run time estimates.
1. Full cloud enabled that works in Onshape. Have direct link so CAM updates as models update.
2. Able to create code for the large production metal cutting manufacturers (We have Trumpf for laser, Flow for waterjet, Messer for plasma)
3. Automatic cutting path creation (smart to etch/scribe first, cut inside geometry next, cut outside geometry last). Logical/sequential path taken from feature to feature in a part and from part to part in a nest.(Not a random path that moves all over the sheet like Fusion does).
4. Automatic nesting of parts
5. Automatic detection of material thickness, and type that is set in model.
6. Grain direction, control of rotation of part in a nest
7. Ability to ignore features such as the counter sink/Counter bore outer diameter and just cut the though hole.
8. Ability to set or recognize etch/scribe geometry on a part.
9. Since Onshape does not have a dedicated sheet metal environment, it will need the ability to use the flat pattern generated by Onshape.
10. Ability to load an assembly, the software extracts only items to be cut and discards hardware/bought items. Might need to have a property field created in the model that distinguishes this that the software can reference.
11. Set shear paths/cuts on the sheet to run after nest is run to create drop blanks that can be used on future jobs. Primarily square/rectangle shapes.
12. Ability to set tabs on internal geometry on a part and external geometry. Very useful when running lights out manufacturing.
13. Ability to set curve width cuts, used in the aid of hand bending items and or relieve areas that would cause deformation of geometry during the bending process.
14. Common edge cutting.
We are not an OEM manufacture so we receive all types of files. The most common are .dxf and .dwg files of flats to cut. So the ability to work with non native Onshape 2D geometry is a plus. More information will need to be entered by the operator but .dxf and .dwg is still a standard that most 2D cutting CAM software accepts.
Future enhancements I would say is to then provide/store/add information to other manufacturing steps such as inventory control, run time, etc. that could be connected to a companies ERP system.
Probably will have more to add later.
Twitter: @BryanLAGdesign
I'd love to dig into some of those specific features (and I will for sure!) but let me ask you a couple high level questions:
Of these three which do you think you could envision yourself using? And for this answer use your imagination a little bit. I don't think any of these solutions are perfect right now, in fact some can't even work with Onshape at all.. But what you can see in each of these is the way they envision the workflow. Some are more complex than others, and some are dead simple. So if one of these were massaged to include some, if not all of your feature requests which one would it be?
And for a more specific question: If you look in the Onshape app store under CAM: https://appstore.onshape.com/apps/CAM?sort=featured
You'll see save for KiriMoto the rest of the options are just connectors for desktop apps. How important is having something that's cloud based and really "built in" to Onshape?
And last one: Did any of your try and use VisualCAM C when it was on the app store, if so, thoughts?
Example: Our operators of the cutting machines create the code to run the job. When they are out due to illness, vacation, or in these times ,stuck in quarantine, we need to keep the machines going. With our current CAM software if you have not used it much there is a high learning curve just to generate code for a simple part. The approach you have with Fabber looks logical, user friendly, and the knowledge to run it can be easily retained no matter if you use it every day or once a quarter. That is one key aspect we are looking for in a CAM software.
It being cloud based and hopefully connected to Onshape will allow someone to generate CAM code no matter where they are. If for example in quarantine and stuck to work at home I could design at home and then generate code for the machine. With a simple e-mail to the link of the Onshape document, the operator can access the code, download it and keep the machine running.
I could see accessing Fabber in Onshape similar to the attached image.
Twitter: @BryanLAGdesign
For Fabber on we're obviously trying to make it as easy to use as possible in a shop, ands your use case is definitely one we've thought of... Letting a designer/engineer setup not only the model, but the feeds/speeds/cutting strategy for a model so that can be shared as a preset of sorts to people running the machines.
In the current situation the world is in, in theory this means that someone like your self could setup jobs and have a small crew head into the shop and make them...
Having something built in to Onshape is fundamental - there is no point in moving from VCarve so anything that is not! Also, I would hope that a part in Fabber would maintain its Onshape identity too!
I did download and play with Visual CAMC but didn't make much progress - I don't remember from this far away whether that was my lack of effort of their steepness of learning curve! (see all the comments above about the importance of ease of getting started, or re-started, even if you can subsequently refine choices as you progress).
Let's say you upload a model from SketchUp and start getting it setup and you then realize that you forgot a part, need to change something, etc... You can go back to your model and re-upload it (With the changes) and Fabber will recognize what's different. It will re-nest parts of necessary but it won't make you re-work all of the settings in the job.
I'd like to do something similar to that in Onshape. Like you (and I from what I've found a lot of other users) I'm taking my Onshape files and bringing them into something like Fusion to toolpath. Not idea because that connection isn't there not to mention that you have to buy another program.
Twitter: @BryanLAGdesign
I work with high school students on a robotics team; we design and cut our own parts on a couple of different CNC routers (and would like to be able to expand to plasma and laser cutters too). We'd love to have a good connected or integrated CAM solution that can understand and separate parts of different materials and thicknesses and nest them separately. It would also be really useful to be able to designate which machine a particular part should be sent to so the nesting can differentiate that way too.
Right now we're using Fusion 360 to do our CAM; the auto-nesting from the assembly view that they just released looks really nice, but we're not willing to move away from Onshape for design, so that's likely a non-starter for us.
And of course cheap or free for edu users would be awesome as well.
Thanks in advance for listening!
1. Automatic tool selection & tool speed setting.
This has never been done because of the variation in the work piece material environmental conditions and machine capabilities. An experienced person has always been required to test a tool per application starting with conservative settings then adjusting closer and closer to aggressive until satisfied. In the end this is incredibly time wasting and has to be repeated with every new tool / material. Make it so there is a way to collect data such as material hardness / Grain properties / Machine limits / Tool-bit characteristics etc and have the nester calculate optimal settings.
2. Don't make damaging the machine, material or Machinist an option (Automatic Test piece)!
It's imperative that nothing other then manual G-Code adjustment can result in damage, no setting, feature or override should ever exist that allows accidental mistakes. It's so easy to forget you made a setting as a workaround previously and forget later resulting in thousands worth of damage. To achieve this emphasize the importance of a test pieces and make them automatic. For example recognizing a new tool has been entered and offering to include a standard route test that uses an/a variety of intended types of materials.
3. Automatic setup and jig work & small part management.
Not every piece cut has machining on one side, is large enough or non-porous enough to stay fixed in place while being worked on, or can be cut on one pass from one side with enough distance between parts for tool width. More often then not a lot of manual work goes into creating one use jigs, adjusting G-Code, and Double processing parts on a machine that may have recently become unaligned with router-head to origin. Accounting for unique processing as a built in feature, similar to the way support material is made in 3D printing, would greatly distinguish your nester. An example would be a report that stipulates order of actions such as router tool adjustment, Part tool flipping, jig creation and exact part orientation to take a block of timber and machine it either side to create a handle profile. All one would have to do is setup jig settings once and whenever a piece is nested that would require one it would be included in work order along with clear instruction.
4. Complex Grain matching , Stock & off-cut management.
Most nesters manage stock and grain matching in one way or another, but none of them take into account the specific pattern on each piece, the side of the material which is decorative, allow for damaged surfaces & zones and/or allow for each piece to be any shape other then a rectangle. I've also never seen a nester that could grain match two pieces on two different sheets that have the same printed pattern. Accounting for relative part alignment, Stock and off-cut shapes, prints & workable zones would be invaluable and save hours of time. Also with stock management I strongly recommend creating a system that integrates with an app as well as IOT devices to automate stock keeping on the floor. The hardest part in keeping this feature relevant is making sure the information stored reflects reality on a consistent basis.
Was wondering if there is any update on this project?
Thanks,
I know it's been a WHILE, but we are taking another at the possibility of bringing Fabber to Onshape.
We had done some preliminary work on it several years ago, and for a variety of reasons we had to go in a different direction.
There's a small chance we might resume development on Fabber in Onshape again… I am curious what the interest level would be if we did?
You have my interest.
Twitter: @BryanLAGdesign
It's hard to say @eric_schimelpfenig, Onshape will be releasing CAM Studio in the near future, it would be good to check with them to make sure your app won't be redundant.
CAM Studio will not be automated. At least not at launch, and I doubt it will have API or custom development tools like FeatureScript at launch either. But we can hope! I think I already created an improvement request for this but I lost it.
Learn more about the Gospel of Christ ( Here )
CADSharp - We make custom features and integrated Onshape apps! Learn How to FeatureScript Here 🔴
My guess is CAM Studio is more like Fusion in that it's great for metal machining and fixtured parts. Fabber is much more geared towards flat/nested parts. Think plywood, plasma cutters, water jets, etc.
@eric_schimelpfenig You have my interest big time.
We currently use a custom feature to layout the parts flat, and then an annoying workflow to take DXFs to Vcarve.
Would love to help/give feedback in anyway to get a better system in place.
Glad to hear you guys might do something for Onshape. I spent a lot of time researching and there are no viable options for this process (Onshape to CNC sheet cutting). The only solutions I found are very expensive.
@ben_partouch Have you ever tried going out to Fusion 360?
@bryan_lagrange What's your process now? You design something (assumably something that's some kind of flat part for plasma or waterjet) and then you… Have to flatten it in Onshape? Bring it to another CAM software?
@MichaelPascoe What about you? Are you using VCarve too or something else?
We export .dxf of flat patterns and send it to be CAM software for the laser, plasma, or waterjet.
Twitter: @BryanLAGdesign
What CAM software do you send it too?
We send to the folllowing:
Trumpf laser: Sigma nest
Bystronic laser: Bysoft
Flow waterjet: Flowcut/Flowpath/Flownest
Messer plama: Omniwin
Twitter: @BryanLAGdesign
@eric_schimelpfenig Their Nesting feature requires additional payment and I don't like Fusion so much generally speaking. Vcarve is not intelligent but the simplicity can be an advantage in many cases for our use of it. Working with Fusion will also require export/import as well.
So overall I don't see the reason to work with Fusion.
The ultimate solution will be something similar to Vcarve (simple and straight forward) that can import 3D assembly, then flat, nest and apply a toolpath template. Cloud based will be even better :)
Something like this?
Let me ask you this:
CAM Studio (what Onshape is working on) :
https://www.onshape.com/en/features/cam-studio
Looks very similar to the direction Fusion is heading.
If you had the choice of CAM studio or Fabber in Onshape, which would you pick for large nested work?