Welcome to the Onshape forum! Ask questions and join in the discussions about everything Onshape.
First time visiting? Here are some places to start:- Looking for a certain topic? Check out the categories filter or use Search (upper right).
- Need support? Ask a question to our Community Support category.
- Please submit support tickets for bugs but you can request improvements in the Product Feedback category.
- Be respectful, on topic and if you see a problem, Flag it.
If you would like to contact our Community Manager personally, feel free to send a private message or an email.
Lofting hollow faces

I must be blanking out, but I'm hoping a quick jog will get me going.
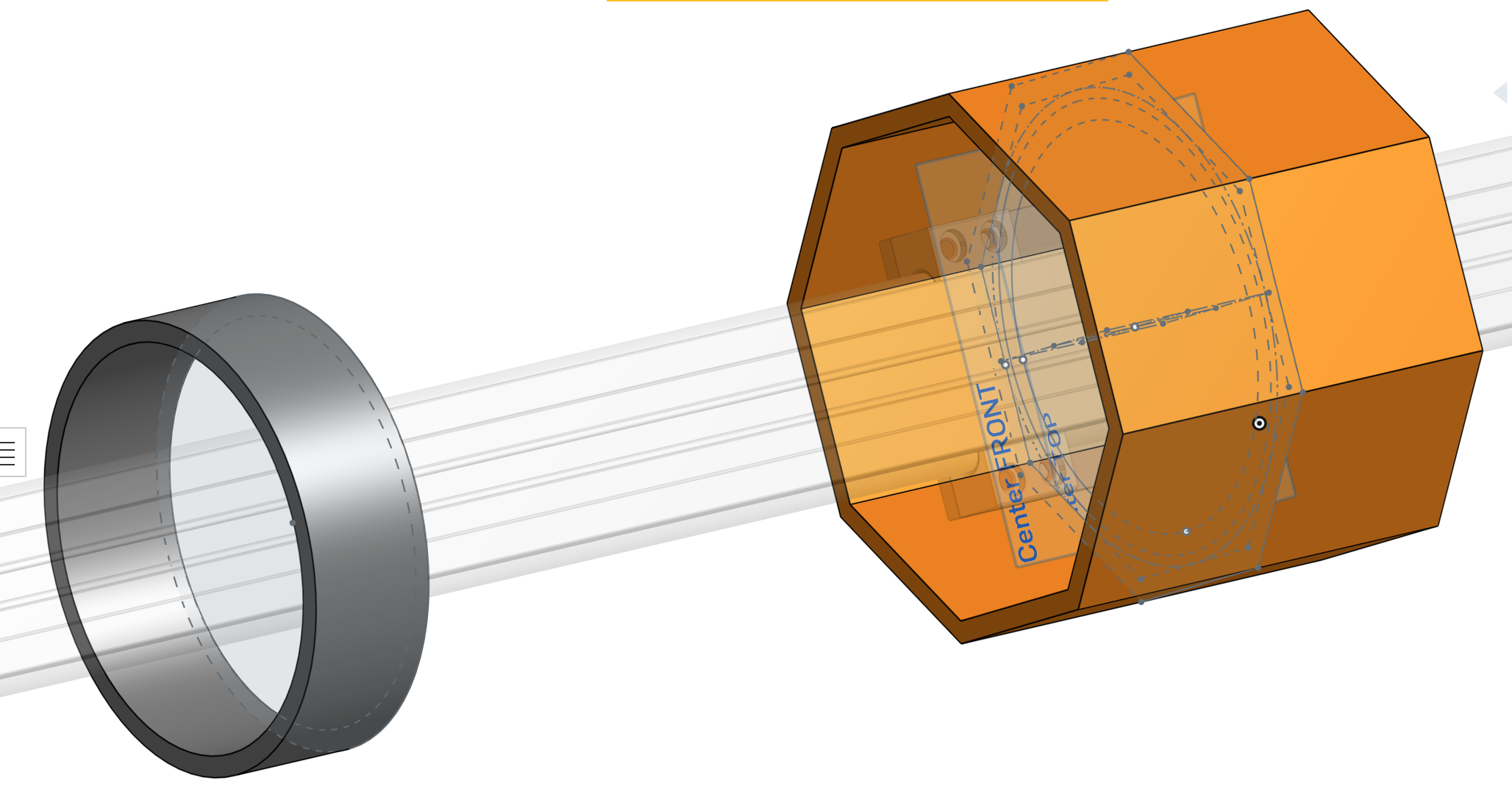
Trying to connect these two using loft. I can't loft a hollow solid it appears (inner loop), and, whilst I can create two surfaces (inner and outer), I don't know how to convert them to a (hollow) solid afterward. I know I can just do the outer and then thicken but I'd rather not. What am I missing?
Tagged:
0
Best Answer
-
romeograham Member, csevp Posts: 715 PRO
Here is a very simple Part Studio that may help - I'm not sure if I've captured your design intent, but you can see some of the options required to make it work here: https://cad.onshape.com/documents/cb88cc98359cc555d3f37f08/w/e9d4e656351e1b7fc03bc2e5/e/2cf677c0dbeb958a080e9d36?renderMode=0&uiState=61bf89f55fd10b7f07d6acd6
Note that you need to make sure that your first parts are solids (Extrude >Solid) and your Loft is set to "Add".
Good luck!0
Answers
You can create the Octagon and Circle features as solids first. Then do the loft, and then shell afterward. If you don't want the three parts to be combined into one, then make sure you have 'New' selected in the scope of the loft feature.
Hope this helps!
Note that you need to make sure that your first parts are solids (Extrude >Solid) and your Loft is set to "Add".
Good luck!
It looks like you're trying to loft the whole thing, instead of just creating the transition as a loft. This is why you had to crank up the magnitude to 2.0 and it's still not doing the same thing that @romeograham did.
Simon Gatrall | Staff Mechanical Engineer | Carbon, Inc.
Thanks for the input @S1mon - can you maybe elaborate a bit? I selected the face of the cylinder and the face of the octagon solids and lofted those two, nothing more - isn't that what you mean by the transition?
Looking at in more carefully, I see that I confused the picks for the thicken with with loft.
- @romeograham just had tangency conditions for both ends of the loft. You have curvature for one of them. Normally curvature is smoother, but there's something else going wrong here.
- It looks like you may be thickening to the outside, which is often less likely to give the best results on the outside, but again this isn't the issue.
- Shell is a much more robust way to get the wall thickness, since you only need to pick two surfaces to remove, instead of all the surfaces to thicken.
- It looks like you have created two parts instead of one. Perhaps your loft was only merged with one of the two extruded parts?
It would be a lot easier to help with this if you shared a public document.I think I've recreated the mistake you made. It seems like you picked the wrong end of the octagonal extrusion to loft. If I pick the far end, and use curvature/magnitude 2, I can almost get the loft to line up where you want it, but it has the step, just like yours.
What you want to do is loft the faces that you're trying to connect:
Simon Gatrall | Staff Mechanical Engineer | Carbon, Inc.