Welcome to the Onshape forum! Ask questions and join in the discussions about everything Onshape.
First time visiting? Here are some places to start:- Looking for a certain topic? Check out the categories filter or use Search (upper right).
- Need support? Ask a question to our Community Support category.
- Please submit support tickets for bugs but you can request improvements in the Product Feedback category.
- Be respectful, on topic and if you see a problem, Flag it.
If you would like to contact our Community Manager personally, feel free to send a private message or an email.
Pawl and Ratchet Assembly
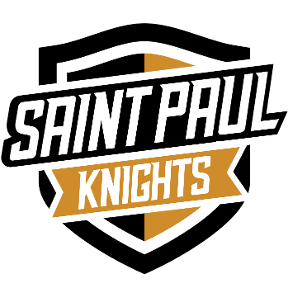
I'm trying to assembly a pawl and ratchet so I can animate it. I mated both the pawl and ratchet as revolute so they both spin (I restricted the pawl to only move back and forth about 10-15 degrees). Have tried several ideas (making them both gears, mating the pawl and ratchet as planar and or tangent along with revolute. None of these has proven satisfactory. Is there a standard way to mate a simple 1 tooth pawl to a multi tooth ratchet wheel? I haven't been able to find any detail on this in the documentation or on Youtube demos. Here's a picture to show what I'm trying to do. Thanks for any guidance on this.

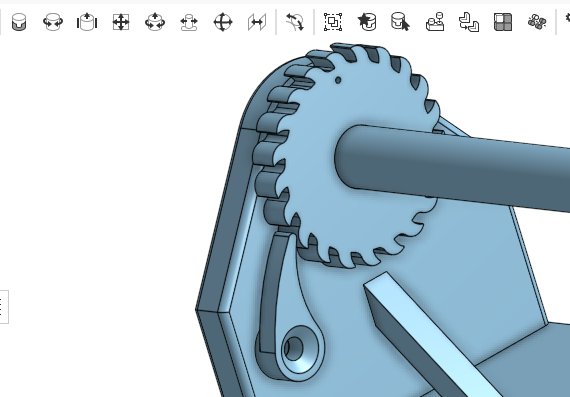
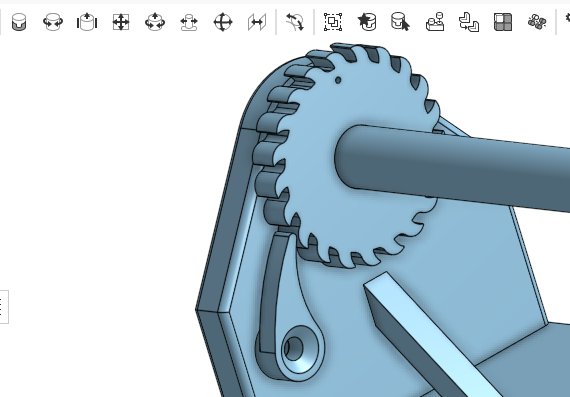
Tagged:
0
Comments
https://cad.onshape.com/documents/7c762df7e20860e995a1809f/w/3136126b5d9e49df8971eecf/e/0e901977c5810791c2d0173a
In the assembly, there’s a hidden part, Part 4, which is providing the path for tangent mate to work off of.
Is that Part 4 just an extruded sketch that encloses the whole gear?
I'll keep playing with it, but I can't seem to get the whole perimeter to turn gold on the ratchet piece. I'm only getting a single tooth, thus the pawl doesn't move to far.
I'll keep experimenting.
Thanks.
I’ve renamed Part 4 as TANGENT GUIDE - you'll have to click on the link above for the document, to see the changes.
In this case, you need to have a path that has tangency all the way around. That’s why I use a dummy GUIDE, in order to work with the tangent mate. So I’ve done this by filleting the outermost surfaces of the TANGENT GUIDE, in order to make a contiguous set of tangent surfaces - all the way around. This will allow for one surface of the pawl to be in contact with one surface of the guide at all times. Now during animation, the guide is HIDDEN, but it still provides the path for the pawl. The ratchet simply spins along with the guide, but is not interacting with the pawl. It just looks like it does.
And, you want to avoid anymore than that. That is, you want to avoid the mass of different parts from accupying the same space at the same time. No INTERFERENCE. That’s why I can’t use the pawl with the ratchet acting as a guide, because the teeth, turn back on themselves, so to speak, which would make for interference, if used for a path. And this is why all the outermost surfaces of the guide face the direction that they do, as this design keeps one part (pawl) from going through another (guide), which starts to confuse the animation program. The guides shape makes it so only one SURFACE of one part is touching one SURFACE of another part at any one time - and no more than this. Just a surface sliding across some other surfaces - and no contact other than this.
Take a look at the 2 GIF's below
In the document in my post above, all you have to animate is REVOLUTE 1.
The GIF directly below shows how I set up the TANGENT MATE for the pawl & guide in the assembly.
Below is a GIF that shows how there is a round on the rip of the pawl, so made to avoid there being any INTERFERENCE with the rest of the pawl and the guide. In other words, I only wanted one surface at the tip of the pawl to come in contact with the contiguous surfaces at the outermost of the guide.
Here I use a selection filter set to TANGENT
And that’s because of the fillets that you see at the start of this GIF. Those fillets make each surface tangent to the next adjoining surface
I really appreciate all the help here. Know that you are helping a group of 2 dozen future cad engineers in my intro to Cad class.
https://cad.onshape.com/documents/aa3518f6b5cabb68bad2ef7d/w/b6ea5d741a75f829717be9a2/e/bce456912212cf07f9dacda0?renderMode=0&uiState=637fa51562a1d9465e3b4afc
Thanks.
In the GIF — the 2 arcs that I select — looks like they are not tangent, from what I see in your screen capture. So the first thing I would do is, I would use the selection filter, to see if things are tangent all the way around. If not, then you will either need to modify a sketch, or the settings of some fillets.
If you give permission to copy your document, we can take a look at things.
That first document I posted, was done in haste, as it was just for testing an animation I did way back when.
Made a new document from the ground up. Easier to understand. Not looking for the least amount of features, but rather, something that is easy to decipher.
New document has better part studio and assembly. You can step through the features and dialog boxes to see how things were set-up.
https://cad.onshape.com/documents/7c762df7e20860e995a1809f/w/3136126b5d9e49df8971eecf/e/0e901977c5810791c2d0173a
As to the assembly ——
Once you get tangency all the way around ———
The shape of your ratchet might give you some problems with interference.
But this is a guess at this point because I have not played with such a shape.
It might be solved buy making the tip of the pawl larger and bulbous to where it sticks out.
Here is how it should look when you are setting up the tangent mate and animation
Still can't get the ratchet to select the whole perimeter of the track.
On a brighter note, I can see and understand everything you have done and very much appreciate the help.
Maybe my parts are still just not meshing for some reason.
I have added export to the drawing, so if you have a chance, would appreciate any further help.
In any case, thanks for the time you have given. I've got a much better understanding of the whole situation.
Thanks very much.
-https://cad.onshape.com/documents/aa3518f6b5cabb68bad2ef7d/w/b6ea5d741a75f829717be9a2/e/bce456912212cf07f9dacda0?renderMode=0&uiState=6380d3a4389e514782e5dac8
Not really looking for an export
A copy will give me a lot better insight into what is going on
Imported your Ratchet & Pawl
Made both parts the same thickness.
Still didn't work
So I modeled the ratchet,
and imported your pawl that I modified the thickness of.
That worked.
https://cad.onshape.com/documents/a8dd5c6fb4d72db67892e59a/w/2bb110106b0e3ce630c7ac34/e/2cfacb691b58e1ea70a67d20
I’ll throw in a little bit more
I rely heavily on feature patterning as opposed to sketch patterning. Feature patterns work better for me. So if I have to use a few more steps within the feature tree, that’s OK by me
The other thing is that I make sure that all my connections of lines to arcs or circles within sketches, have tangency at each end on a thing like this.
I also like to mirror within sketches and when doing features
But without having a copy of your document, It’s gonna be hard to help any more than this.
Make a copy of your document. Then in that copy, delete every part studio and assembly except for the ratchet
In other words — send me a document that has one part studio only — that part studio being the ratchet
I want to see how you make that ratchet
I left just the base, pawl, and ratchet.
https://cad.onshape.com/documents/151c0b7066de13cd91629c66/w/6ec262820d6e9544d86b38c4/e/12707c27f144913d76ead624?renderMode=0&uiState=6382333e9035af22fc5b6c05
I'm glad you sent the 3 part studios
Doing this earlier on would have likely cut to the chase much sooner and without all my blathering LOL
https://cad.onshape.com/documents/0c0a142c886a304df0aaa628/w/320ece8786143d34b1c06bd0/e/a9f40f65c7dda35847fbba0d
That's the proper link above NOW
I think it might be easier for the animation program to have a pawl with a general orientation somewhat like what is shown in the sketch below
Main part of pawl arm closer to 90° to the 9 o’clock position in this case.
In other words, you want the main part of the pawl arm to be closer to perpendicular to what is NORMAL TO the circle.
I am guessing that maybe a hook of sorts on the end of the pawl NORMAL TO the circle of the ratchet MIGHT help in your pawl design.
And off course the pawl doesn't have to be as basic as I made here.
Have not done much experimenting at this point, so take these statements with a grain of salt.
Nonetheless, give this a try.
You might also want to take a look at how the ratchet was sketched as your teeth were not constrained.
NOTICE the edge of face segment on your ratchet
On the other hand, below is something fully constrained
The main part of the pawl is straddling the horizontal in this case
Which is roughly perpendicular to a vertical line coming off the center of the ratchet
Seems to work