Welcome to the Onshape forum! Ask questions and join in the discussions about everything Onshape.
First time visiting? Here are some places to start:- Looking for a certain topic? Check out the categories filter or use Search (upper right).
- Need support? Ask a question to our Community Support category.
- Please submit support tickets for bugs but you can request improvements in the Product Feedback category.
- Be respectful, on topic and if you see a problem, Flag it.
If you would like to contact our Community Manager personally, feel free to send a private message or an email.
Feature Request: Curve-like mate connectors (line, circle, arc, etc)

I would like to be able to define curve-like mate connectors (MC). In this case, when I say "curve" I mean a 1D object which could be straight. So this could include lines, arcs, circles, splines, lines along surfaces, a tangentially connected sequence of other curves, etc. The curve MC would be oriented so that at any intermediate point could be thought of as it's own point MC with an X, Y, and Z axis. This would be a building block for automatically inferring certain mating types to more quickly build up assemblies.
One possible application is to automatically define slider or pin-slot mates with limits when a point MC (the current type) is connected to a curve MC. Alternatively, the point MC could be a fastened with an offset set to a certain distance along the curve MC. There could be shortcut to define the mate at either end or at the midpoint along the curve.
Two curve MCs could also be connected together in interesting ways. For example, a shorter line MC could be mated to a longer line MC with a slider mate and the limits of of travel could be set so the smaller line MC can't leave the longer one.
This idea came up when I was making an assembly from t-slot extrusion (see image below). I'd like to be able to quickly mate the MC on the plate to the line between the MCs that I defined at the end of the extrusion. The line between the MCs at the ends of the horizontal extrusion hovering in air. There are ways to define a slider with a single mate here but it can require a lot of precision clicks and mating to weird things like tangent points. I rarely use limits for slider mates, but having them automatically inferred would be awesome. For common, configurable parts like this extrusion, it would add a lot of value to set up the part so that all future assemblies can go quickly.
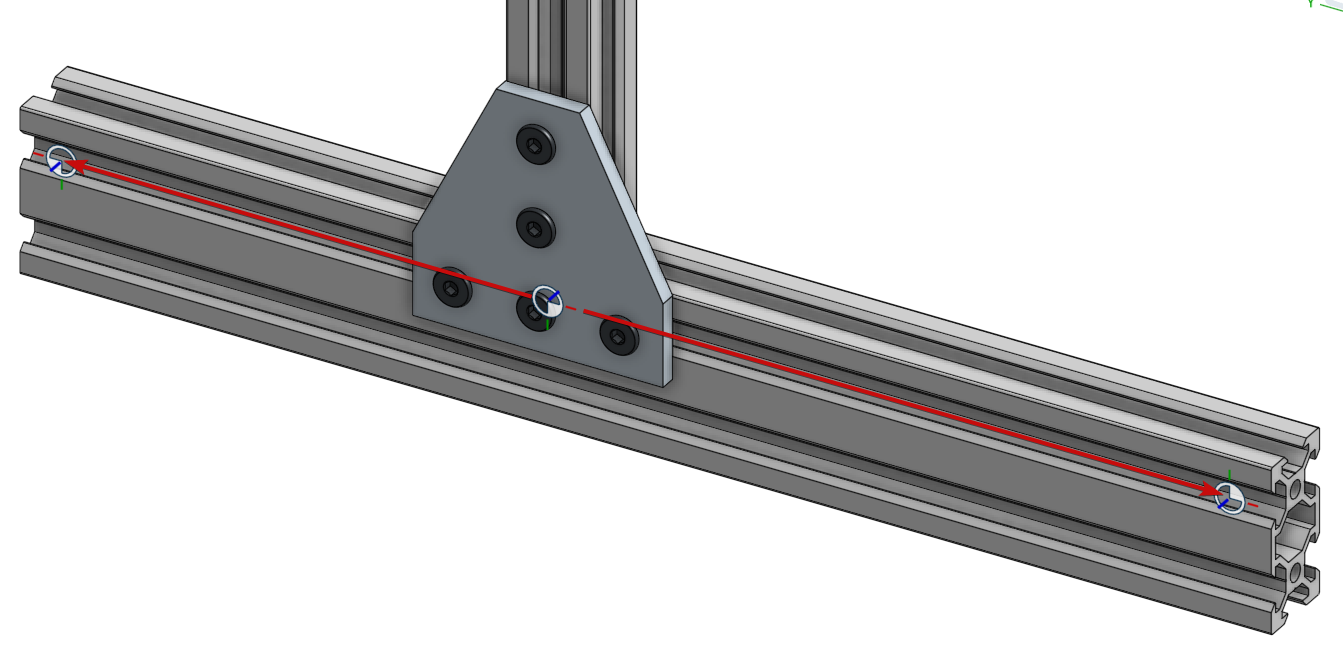
For a reference, Vention.io has a dedicated (closed) design tool for their extrusion system. Extrusions can snap to other extrusions and a slider mate is automatically inferred. I'd rather work with in a more open design platform like OnShape, but I would like the option to build up this kind of intelligent mating system into my own parts.
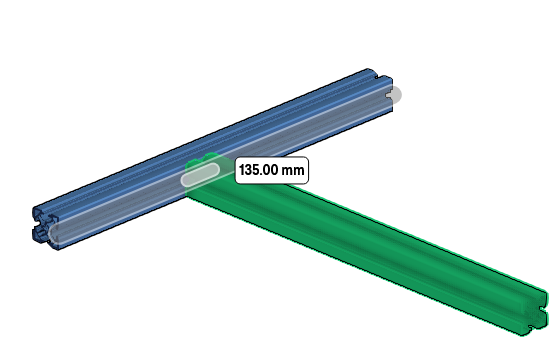
0
Comments
For example if you create a Mate Connector 1/2 the width away from the end of that profile you can very quickly mate it to the center of another existing exiting profile using the snap function (and change it to a slider):
And here's what some MCs in a bracket can do for you:
Reminder: "ctrl" cycles through the reference MC in the part you are inserting, "a" flips the Z alignment and "q" rotates in 90deg increments.
Here's the example assembly:
https://cad.onshape.com/documents/7dde71c7350454606a95cb3e/w/6bc23be9bf2088505e317eeb/e/4c5381a7ba276aa77a639882