Welcome to the Onshape forum! Ask questions and join in the discussions about everything Onshape.
First time visiting? Here are some places to start:- Looking for a certain topic? Check out the categories filter or use Search (upper right).
- Need support? Ask a question to our Community Support category.
- Please submit support tickets for bugs but you can request improvements in the Product Feedback category.
- Be respectful, on topic and if you see a problem, Flag it.
If you would like to contact our Community Manager personally, feel free to send a private message or an email.
Options
best way to force mate connectors on an imported stl?
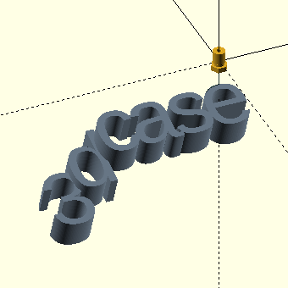
This is a strange question perhaps, but my entire history modeling in 3D has been with Openscad. I therefore have many such files, which cannot be imported into Onshape. So I use the STL files often to make it again with some modification or to design something that will fit together with an existing STL.
The trouble is the STL files are just a great mess of meshes with points that do not seem to follow any logical positioning.
This makes positioning of mate connectors very difficult. More often then not I cannot find the same location on an imported file, which I would need for correct mating with another part. I need to use manual offsets most of the time and this is not very accurate nor convenient.
So, my question is if there is a better way of doing this?
I have till now simply attempted to place the mate connector somewhere on the piece by trying to find some mesh point close to where it needs to be. Very rarely do I find any right on the spot, and more rarely do I find symmetrical mesh points to use in the "in between" feature.
Any help would be greatly appreciated.
0
Best Answer
-
matthew_stacy Member Posts: 489 PRO
@kees_bijker, STEP would likely be a better option than STL for what you are trying to do. The imported solids will still be non-parametric, but significantly easier to use than mesh geometry.Onshape also has a competent suite of direct editing tools (e.g. move face).0
Answers
But yes, STL in general is harder to work with. It was really developed as a way to 3D print things, not a basis for modeling.