Welcome to the Onshape forum! Ask questions and join in the discussions about everything Onshape.
First time visiting? Here are some places to start:- Looking for a certain topic? Check out the categories filter or use Search (upper right).
- Need support? Ask a question to our Community Support category.
- Please submit support tickets for bugs but you can request improvements in the Product Feedback category.
- Be respectful, on topic and if you see a problem, Flag it.
If you would like to contact our Community Manager personally, feel free to send a private message or an email.
Countersink with head relief
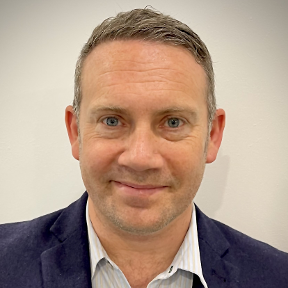
in General
I cannot see that the hole tool for countersink has head relief. I.e. ability to add a small pre-counterbore same size as the c'sink OD that drops the screw in slightly. Is this the case, that this is not in the tool?
1
Comments
Simon Gatrall | Staff Mechanical Engineer | Carbon, Inc.
I thought only 60 deg lathe center drills came in this form factor, and that the c-sinks for screws were all the one-size fits all oversized variety. Good to know if I have a need for this:)
Simon Gatrall | Staff Mechanical Engineer | Carbon, Inc.
I already changed some screw types on another assembly from countersunk to socket head caps because they're holding a plastic part which was cracking (definitely not my original design). Cast aluminum parts probably have some risk at the extremes for the reasons you stated, but we've never seen failures in this application. There is a possibility that they are post machining the holes to improve the flow, but I haven't seen the tool design.
Simon Gatrall | Staff Mechanical Engineer | Carbon, Inc.
The enemy of the good is the perfect.
It would be great to have some defaults which make some sense and are related to real hardware, but it's likely that "head clearance" height dimension is going to be highly dependent on the context and design goals, not the hardware itself. Right now, I can't use the hole feature to make this shape, and unlike a regular counterbore, there's no quick hack with move face to get this geometry from a countersunk hole. About all I could do is use a counterbore and add draft, or I just have to revolve a cut and pattern it.
Simon Gatrall | Staff Mechanical Engineer | Carbon, Inc.