Welcome to the Onshape forum! Ask questions and join in the discussions about everything Onshape.
First time visiting? Here are some places to start:- Looking for a certain topic? Check out the categories filter or use Search (upper right).
- Need support? Ask a question to our Community Support category.
- Please submit support tickets for bugs but you can request improvements in the Product Feedback category.
- Be respectful, on topic and if you see a problem, Flag it.
If you would like to contact our Community Manager personally, feel free to send a private message or an email.
Linearly Variable Scale Transform
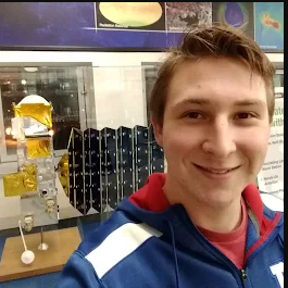
Hi all, I'm pretty new to CAD in general, and even newer to Onshape. I've realized that in one of my designs, I made one of the parts a bit too small, and want to scale it, rather than rolling everything back and re-designing much of the part studio, as there are many dependencies on the part in question. I know that simply scaling after the fact, isn't the best practice, but I'm not really going to feature efficiency, especially because the design of the entire part studio is finished, I just want to scale one part. For context, I'm designing an aircraft, and have found that the horizontal stabilizer is too thin at the trailing edge, but is satisfactorily thick at the leading edge, therefore, rather than scaling the whole part and making the whole thing thicker, I want to apply a variable scale factor that increases linearly as you travel down the chord length of the stabilizer/elevator, so that the leading edge doesn't scale at all, while the trailing edge scales by a factor of 2 or 3. Is this possible?
0
Comments
Depending on how the part is modeled, a change like that could be modifying one number or it could be hours of work. It’s hard to say without seeing the model. Can you share a public model?
Simon Gatrall | Staff Mechanical Engineer | Carbon, Inc.
Simon Gatrall | Staff Mechanical Engineer | Carbon, Inc.
Also @S1mon 's tip about using two windows is a great one and you might find that it looks a lot worse than it actually is. It's quite common when you have a broken thing high up in your tree and a whole bunch of red downstream to find that fixing the first one makes a whole bunch of problems go away!
If it is really too much of a mess a "backup" option is to use some "delete face" at the end to remove your "wrong" part and re-draw a new part that is correct in its place. It's not "best practice" but if you really are in a bind it could help.