Welcome to the Onshape forum! Ask questions and join in the discussions about everything Onshape.
First time visiting? Here are some places to start:- Looking for a certain topic? Check out the categories filter or use Search (upper right).
- Need support? Ask a question to our Community Support category.
- Please submit support tickets for bugs but you can request improvements in the Product Feedback category.
- Be respectful, on topic and if you see a problem, Flag it.
If you would like to contact our Community Manager personally, feel free to send a private message or an email.
Design paradoxes in 3D modeling
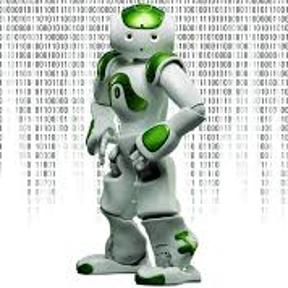
in General
Does anyone ever feel the need that to design a specific group of parts they must model one part that at some point needs to rely on measurements of a later part?
The easiest way I would describe it is a design paradox. Like those time travel ideas, the initial part relies on a later part to function, but the later part was designed based off the initial part, and it seems to be an infinite cycle to us humans. This could also be compared to quantum entanglement, though I'm not sure how comparable that is.
I have tried and failed on more complex models with this idea. What I end up doing is going back and forth with the rollback bar, trying things until a part matches up with a later designed part.
I realize that at some point this would break Onshape (or any other CAD program), since almost nobody can deal with or design in time paradoxes like this. The closest I've found to a paradox with Onshape involve Assembly Contexts. Contexts capture an assembly design at a specific time, but they mostly remain untouched unless someone manually updates the context (and breaks the model).
I am wondering if people have any tips or ideas related to this.
Tagged:
0
Comments
In short, it helps to first create layouts using sketches & other skeleton geometry, then create interfaces between parts, and finally add the finishing details.
For the paradoxical issues you describe, you can often find a way to set the problem up at a high level with a layout sketch, and use the sketcher's solver to rein in parameters and determine the layout so things fit together.
There isn't a silver bullet to doing this type of design in general, but you'll get the hang of it over time.
Also, a pro tip: something that helps solidify your understanding of new modeling strategies is to go back to old models and re-make them using new approaches you've learned, emphasizing a model that is easy to work with and self-explanatory. Revisiting your old work to improve it is a great way to build familiarity with CAD, solidify your understanding of (& practice application) of more advanced modeling techniques, and gives a confidence boost when you see how far you've come!
Finally—remember that CAD is a means to an end. Your ultimate goal is (probably) a working product, not a beautiful CAD model, so don't fret about having some hacky/manually bodged stuff once in a while, as long as it's not making a negative impact on future iterations & product functionality
I'll get off my soapbox now
@alnis is my personal account. @alnis_ptc is my official PTC account.
With variable studios you can capture some of this kind of info in one place, but it's not visual or spatial. Variables are good for highlighting things like overall sizes, key dimensions of important parts/features, nominal wall thickness, draft, etc.
Assembly contexts are well done in Onshape, but I would still only use them when they are critical for things like clearances for mechanisms which have multiple positions.
Simon Gatrall | Staff Mechanical Engineer | Carbon, Inc.