Welcome to the Onshape forum! Ask questions and join in the discussions about everything Onshape.
First time visiting? Here are some places to start:- Looking for a certain topic? Check out the categories filter or use Search (upper right).
- Need support? Ask a question to our Community Support category.
- Please submit support tickets for bugs but you can request improvements in the Product Feedback category.
- Be respectful, on topic and if you see a problem, Flag it.
If you would like to contact our Community Manager personally, feel free to send a private message or an email.
parts not auto inserting at the right place - in context modeling

Hey,
I'm having trouble with the "sync" between the part studio and assembly when I try to auto insert parts I created through "Create part studio in context".
After I move the "in context" parts in the assembly and update the context, the parts auto insert in the "old" position (?!).
without further ado watch the 3 minute video on YouTube detailing the whole concept.
https://www.youtube.com/watch?v=8GMTnojEHF4
I contacted support, but they currently can't fix/explain it.
anyone figured it out already ?
if I ignore that and manually mate the parts, is there a chance for future movement/problems with this assembly?
that's my main concern, the comfort of auto part insertion only comes second.
Regards
Yam
I'm having trouble with the "sync" between the part studio and assembly when I try to auto insert parts I created through "Create part studio in context".
After I move the "in context" parts in the assembly and update the context, the parts auto insert in the "old" position (?!).
without further ado watch the 3 minute video on YouTube detailing the whole concept.
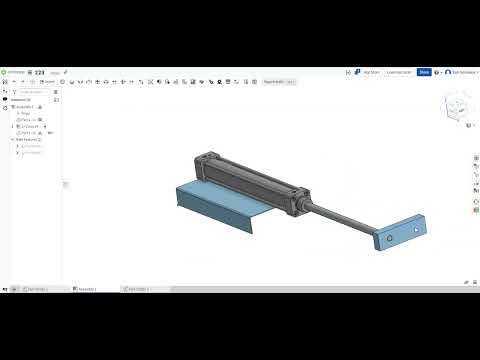
I contacted support, but they currently can't fix/explain it.
anyone figured it out already ?
if I ignore that and manually mate the parts, is there a chance for future movement/problems with this assembly?
that's my main concern, the comfort of auto part insertion only comes second.
Regards
Yam
0
Comments
Hey, thanks for the answer.
1. can you point me to the "multi mate" feature ?
I tried to search it but there are no results with these exact words.
2. Why is it like that ?
I mean the context update should re-orient the part's location relative to the assembly, that’s like….what the context updates are for.
moreover, in the "studio in context view" you can clearly see (watch the video it will clarify), that the software acknowledge that the part moved, and also that the added part are moving with it perfectly.
it's like the part studio image is spot on, but the assembly lost the orientation.
kind of weird, Isn’t it ?
that way the auto insertion of parts just fades away in the "in context" mode.
Here is the mulitmateconnector fs. Its super handy for other assembly situations also.
https://cad.onshape.com/documents/5d8da63844bedebe5cff72b1/w/96a36142be717fc84a504e3f/e/11dcab8f665add80b9aced0a
In your case, I see you did choose the assy origin as the mate connector for the context. But, look at your default planes in the context. They move when you move the piston. And the error in your part placement seems to be the distance the planes moved. I wonder if it has to do with the way you assembled part 1 in your assembly it looks like it's fixed. I wonder if you assemble that part to the origin instead of fixing it, if it will keep the default planes from moving in the context.
I've grown to avoid using "fix" and "group" both in assemblies. For me, they've caused more trouble than they are worth.
to the assy origin ?
didn't quite get what your were saying there, sorry.
actually no.
and I tried it again now to verify.
if the parts did not move from their exact coordinates, the insertion of the next part will be fine.
the motion doesn't have to be like the one in the rod, any placement change will do it, like lengthening of a part.
it was fixed (that's the way onshape instruct you to do in the learning center).
I unfixed it and fastened the part to the origin and.....the problem still exist.
the deviation of the planes clearly shows what I'm claiming, the PS origin and the assy origin lose their "anchoring" to one another.
but not entirely, the update context still "understands" the movement and follow it perfectly, as evident by the PS view being on the spot.
only auto insertion doesn't get it.
Well, just happend to me at the latest model, not sure why it happend now and not before.
but that too is defenetly a thing.
The solution is in the part studio, add a MC at the origin of the part studio. Then in the asm, mate that MC to the MC used to generate the context.