Welcome to the Onshape forum! Ask questions and join in the discussions about everything Onshape.
First time visiting? Here are some places to start:- Looking for a certain topic? Check out the categories filter or use Search (upper right).
- Need support? Ask a question to our Community Support category.
- Please submit support tickets for bugs but you can request improvements in the Product Feedback category.
- Be respectful, on topic and if you see a problem, Flag it.
If you would like to contact our Community Manager personally, feel free to send a private message or an email.
Options
Trouble making a circular ratchet type shape with a hole in the middle
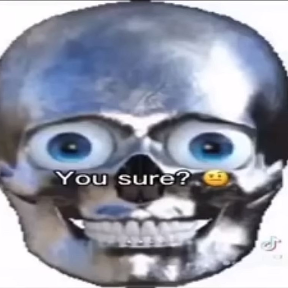
As a first little project to learn how to use the software I decided to do my best to remake a revolver cylinder from a colt single action army (I think guns are very cool from a mechanical point of view) and I'm like 1 or 2 steps away from finishing it but on the bottom of the cylinder is supposed to be 6 teeth that are shaped like curved ramps (Reference photos below, first is an image off of google the other two are the physical part I have) and I'm really struggling to recreate that shape. I have tried using the loft tool but it either ends up trying to make it go over the edge of the hole or makes the outer edge curve in too much towards the bottom. Is there something I'm missing or is this just an impossible shape to make cleanly.
Link to my current part: https://cad.onshape.com/documents/7173d0187578090432e23ba9/w/5ee65da55319d2cd310ba62a/e/a1d6a51f0ce91668dda20a95

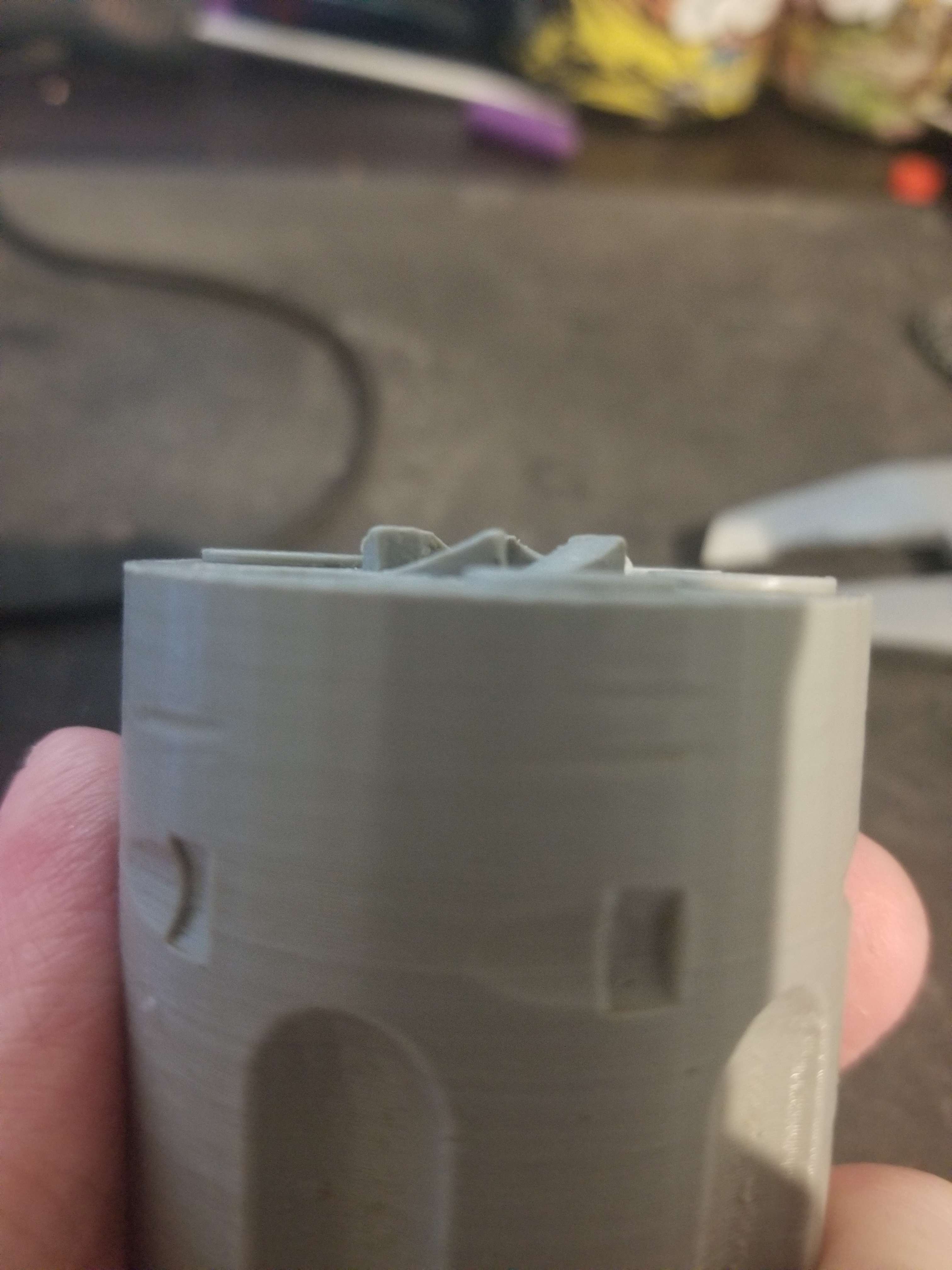

0
Best Answer
-
EvanReese Member, Mentor Posts: 2,461 ✭✭✭✭✭
Here's one way that I think should be pretty good. I'm using the wrap tool to make one of the teeth, and patterning the rest. Be sure to click into some of the dimensions to see some of the equations I'm using to find some distances (like the length of the pre-wrapped tooth). Wrap is going to be better than something projected since the ramped parts really should be helical.
Also, not what you're asking about, but that print looks like a good candidate for adaptive layer height, so you can print the ramps with a much finer layer height than the rest and get a smoother sliding action.
https://cad.onshape.com/documents/7fe36b1b5c99aef1e332a691/w/60587a507a05d3b7c6f77e28/e/c81af24d486ff3fd00cbff59
0
Answers
Also, not what you're asking about, but that print looks like a good candidate for adaptive layer height, so you can print the ramps with a much finer layer height than the rest and get a smoother sliding action.
https://cad.onshape.com/documents/7fe36b1b5c99aef1e332a691/w/60587a507a05d3b7c6f77e28/e/c81af24d486ff3fd00cbff59
The Onsherpa | Reach peak Onshape productivity
www.theonsherpa.com
About the actual part though, I had printed that part very early on in my 3D printing hobby career and so did not know about adaptive layer height but you're absolutely correct that it would be the perfect place to use it.
Also the acute angle between the top of one gear and the vertical wall of the next.