Welcome to the Onshape forum! Ask questions and join in the discussions about everything Onshape.
First time visiting? Here are some places to start:- Looking for a certain topic? Check out the categories filter or use Search (upper right).
- Need support? Ask a question to our Community Support category.
- Please submit support tickets for bugs but you can request improvements in the Product Feedback category.
- Be respectful, on topic and if you see a problem, Flag it.
If you would like to contact our Community Manager personally, feel free to send a private message or an email.
Shelling and tips

Hi!
I'm quite new to onshape, and I'm working on an RC sailboat model that you can find here (Everything is in french, sorry...).
I have this shape for a keel balast that I need do hollow, with a 0.4mm wall thickness. Sadly, I get this error: "Cannot shell parts with selections".
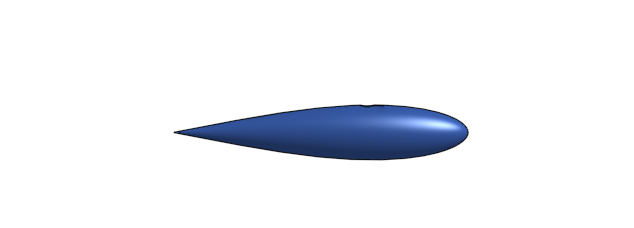
According to this thread, I should cut the model to try and find what part causes this. I thought that the pointy end would be the problem, but surprisingly, when I separate the model in half, I can hollow both parts! I'm a bit confused...
So sure, I could hollow the two parts and then join them back, but I still would like to know if someone has another idea.
To see what I tried, you can just unsuppress this:

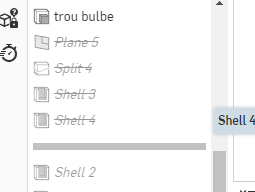
I'm quite new to onshape, and I'm working on an RC sailboat model that you can find here (Everything is in french, sorry...).
I have this shape for a keel balast that I need do hollow, with a 0.4mm wall thickness. Sadly, I get this error: "Cannot shell parts with selections".
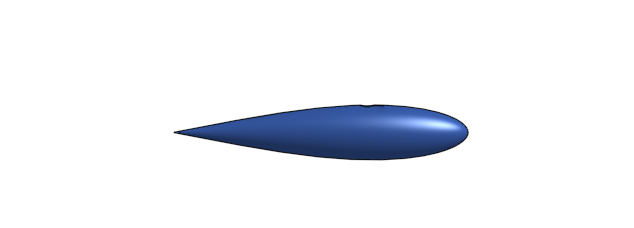
According to this thread, I should cut the model to try and find what part causes this. I thought that the pointy end would be the problem, but surprisingly, when I separate the model in half, I can hollow both parts! I'm a bit confused...
So sure, I could hollow the two parts and then join them back, but I still would like to know if someone has another idea.
To see what I tried, you can just unsuppress this:
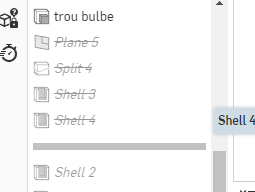
0
Comments
I cut off the very tip, shelled it, and then delete face (with heal) to get back the point on the outside.
Here's my copy of the document.
Simon Gatrall | Staff Mechanical Engineer | Carbon, Inc.
Used the hollow option with shell and it's working fine and holding steady no matter the dimensional changes. I'll have to go further back to see if I can find my previous problem when I have some time.
I would add though that you wouldn't build it with a perfectly sharp point anyway so if you cut it off a short distance away you don't need to "restore" the point afterwards, even 0.5mm away is enough for the shell to work as shown below.
Note that @S1mon's method can be simplified if you use the split directly with a mate connector (eliminates the sketch and extrude features):
I sometimes forget that mate connectors can be used to split things. I also really still think that split part should take a sketch and not need an extrude to create a surface. Coming from Pro/E and Solidworks where you can extrude a non-closed sketch to create a cut, I still really miss that way of thinking.
Simon Gatrall | Staff Mechanical Engineer | Carbon, Inc.
I agree splitting directly with a line would make a lot of sense (it works for surfaces so why not for parts!)
I really like splitting directly with a mate connector as it's "even better" in many cases!
The Onsherpa | Reach peak Onshape productivity
www.theonsherpa.com