Welcome to the Onshape forum! Ask questions and join in the discussions about everything Onshape.
First time visiting? Here are some places to start:- Looking for a certain topic? Check out the categories filter or use Search (upper right).
- Need support? Ask a question to our Community Support category.
- Please submit support tickets for bugs but you can request improvements in the Product Feedback category.
- Be respectful, on topic and if you see a problem, Flag it.
If you would like to contact our Community Manager personally, feel free to send a private message or an email.
Sequential Part Number
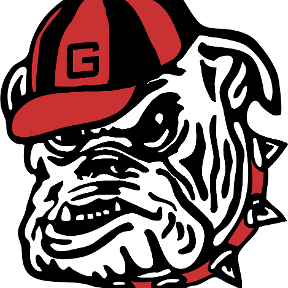
I like the built in numbering scheme but is there a way to have more options for sequential numbering? For example:
9000-XXXX is for top level master assembly
9000-XXXX is for top level master assembly
Weldment Assemblies: 1000
Manufactured Parts: 2000
Sub Assemblies: 3000
Sourced Parts: 4000
Purchased Component: 7000
Spec Components: 8000
Any help or suggestions are welcome. Thank you in advance for any contributors
Tagged:
0
Comments
Simon Gatrall | Staff Mechanical Engineer | Carbon, Inc.
So you don't have the need to learn the meaning of the codes and can directly choose what type of part it is. It is also possible to make it a required property.
@philip_7 I appreciate your contribution as well, sounds like a conversation I will be having in the near future, and you gave me some great talking points
What's missing is kind of a Onshape integrated PLM with only core PLM functionality at a cost smaller companies can bear. There was a sneak peak of that a few years ago at the first Onshape Live event. Unfortunately never heard of this again.
Maybe Duro could be this or also OpenBom has an interesting approach.
In my company we want part number schemes very similar to the ones you list in your original message.
I am currently working on setting up a Onshape-OpenBOM integration for my company. OpenBOM uses catalogs as databases, and each catalog can be linked with a catagory in Onshape. And you can have a unique part number scheme for each catalog.
For instance our Weld Assembly category in Onshape is linked with the Weld Assembly catalog in OpenBOM, and has a serial part number WLD-XXXXX.
Regardless of what option you choose, it looks like you should start to use Onshapes categories, if you haven't done that yet.