Welcome to the Onshape forum! Ask questions and join in the discussions about everything Onshape.
First time visiting? Here are some places to start:- Looking for a certain topic? Check out the categories filter or use Search (upper right).
- Need support? Ask a question to our Community Support category.
- Please submit support tickets for bugs but you can request improvements in the Product Feedback category.
- Be respectful, on topic and if you see a problem, Flag it.
If you would like to contact our Community Manager personally, feel free to send a private message or an email.
How can I shell objects to maintain a XY dimension thickness to optimize for thin walled 3D printing
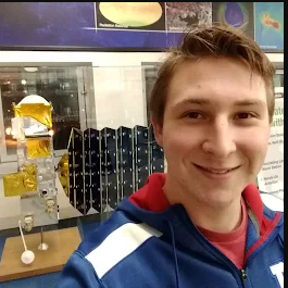
Hi all. I'm trying to design things for 3d printing. I want to be able to shell an object so that the on the plane of each layer, the thickness is equal to a multiple of the nozzle width, so that it can perfectly lay down a single or multiple perimeters perfectly. Currently, when I shell an object, it makes it so that the thickness is the value I set normal to the wall, which is obviously the intended behavior, but it means that for anything on an angle relative to the plane of the layer lines, the shell is thicker than the desired value. I could do some trigonometry to figure out the correct shell thickness to ensure a 0.4 XY thickness, but that wouldn't work for curved parts or parts with varying angles. Below is a very crude paint drawing to try to help visualize what I'm looking for.
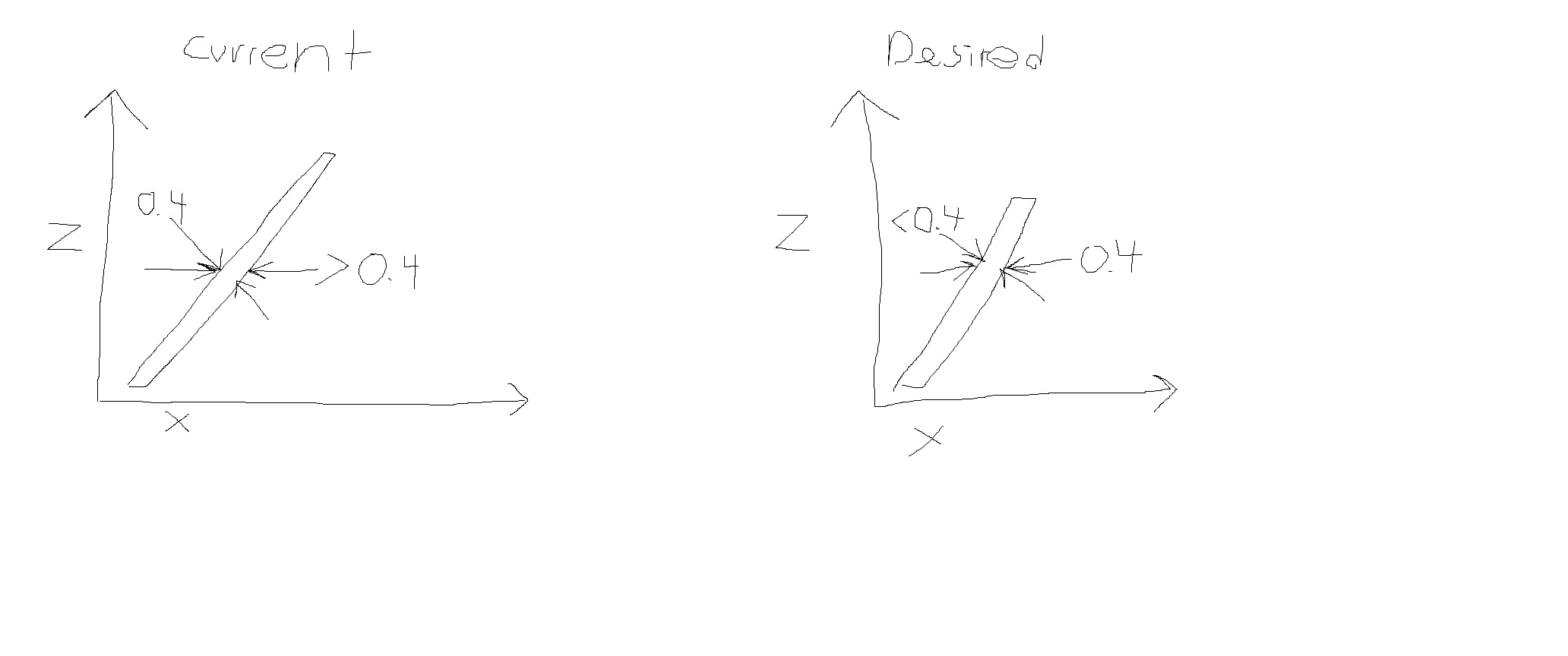
1
Answers
I don't know what slicer you use, but a few of them have a function to vary the line width to reduce unecessary infill.
In the Bambu Studio it is called "Arachne" and this was adopted from other slicers: