Welcome to the Onshape forum! Ask questions and join in the discussions about everything Onshape.
First time visiting? Here are some places to start:- Looking for a certain topic? Check out the categories filter or use Search (upper right).
- Need support? Ask a question to our Community Support category.
- Please submit support tickets for bugs but you can request improvements in the Product Feedback category.
- Be respectful, on topic and if you see a problem, Flag it.
If you would like to contact our Community Manager personally, feel free to send a private message or an email.
Looking to quit Solidworks and 3Dexperience but need opinion
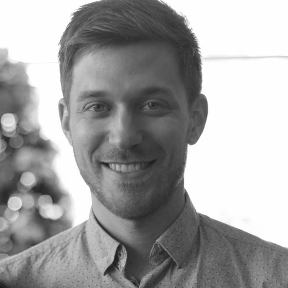
in General
Hello! I’m a new Onshape user I’m currently into a 6 month trial
First sorry for my english, french is my first language 

I’m reaching out to you today to have your honest thoughts to know if Onshape could be a good fit for my company from other people than the Onshape sale team :P
At this moment, I’m the only CAD user in my company. I’m using Solidworks and I did implement the 3Dexperience platform as a PDM recently.
The 3Dexperience is functional… but terrible compared to Onshape data management. This is slow, not user friendly, complicated, lacks options, not well integrated. It feels like a patch. In a couple of months I already lost data with this “cache download” and “server sync” and I often have errors when I save. This is without talking about the all display issue…
Things are going well and I plan to hire some people to help me with the CAD task. The thing is I want to make the choice if Onshape is good for me before hiring.
I Did spend 20 to 30 hours on Onshape and maybe 10 hours in the learning center. I have 15 years of experience on CAD. For me Onshape is very easy to learn and I had no problem doing an assembly of around 80 parts.
There is a long list of feature that i’m using on Solidworks that Onshape do not have but i’m ready to pass over them (but please… add mirror tool into assembly soon :P)
There is my 2 main concern I would like to know your opinion :
1. Performance for a project around 10 000 parts. I joined some pictures of STEP I imported from a typical project I do. The STEP is not functional for editing.But I imagined this possible to do better with multiple Onshape documents but on the other hand, I know STEP imported parts are easier to manage than native parts with features to rebuild.
2. Stability and robustness : I already experience some issue around sheet metal (I’m glad to have been able to test the good customer support :P ). I have read about some bugs appearing randomly. I see that as a high risk of a potential error during the fabrication or lost time waiting when the issue is solved.
I would like to have feedback from people doing similar projects than mine. Thank you for your help.
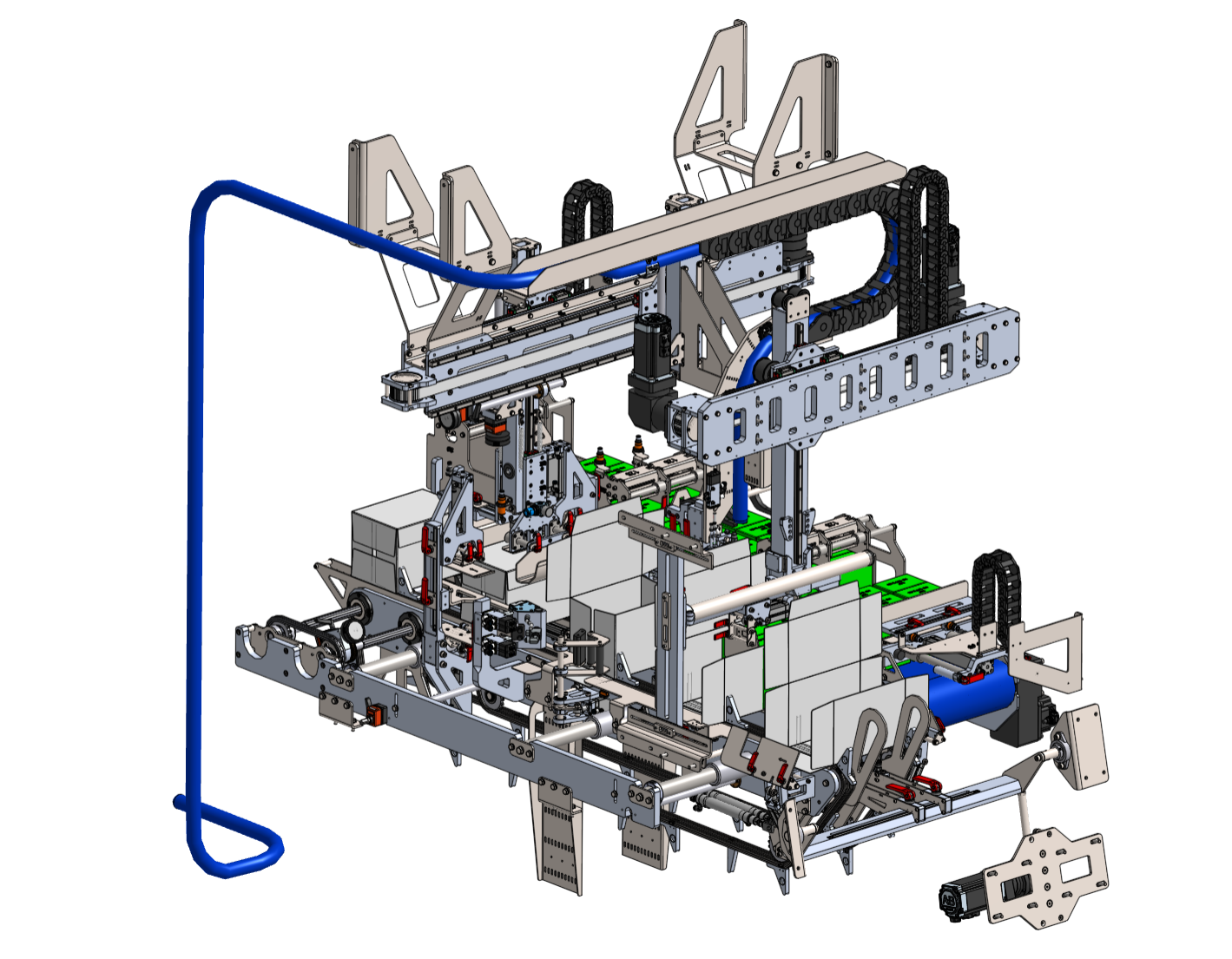
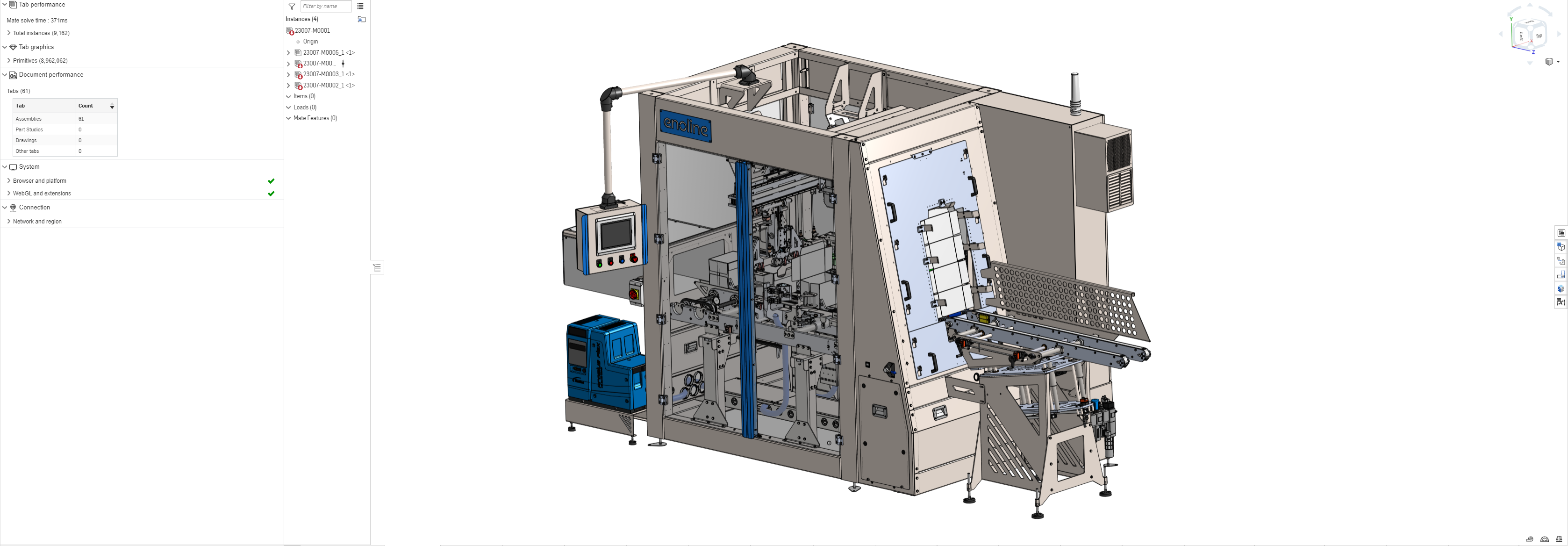
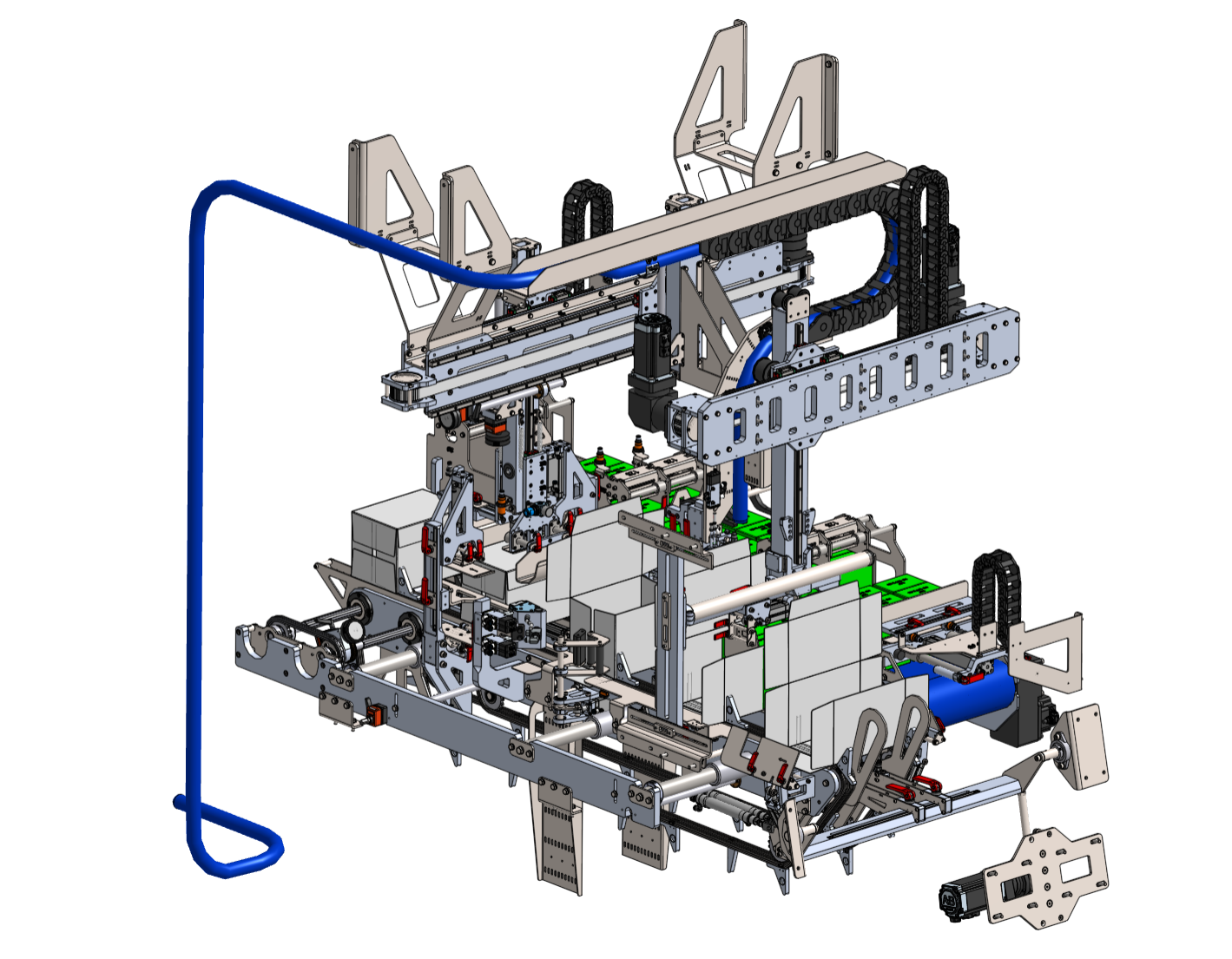
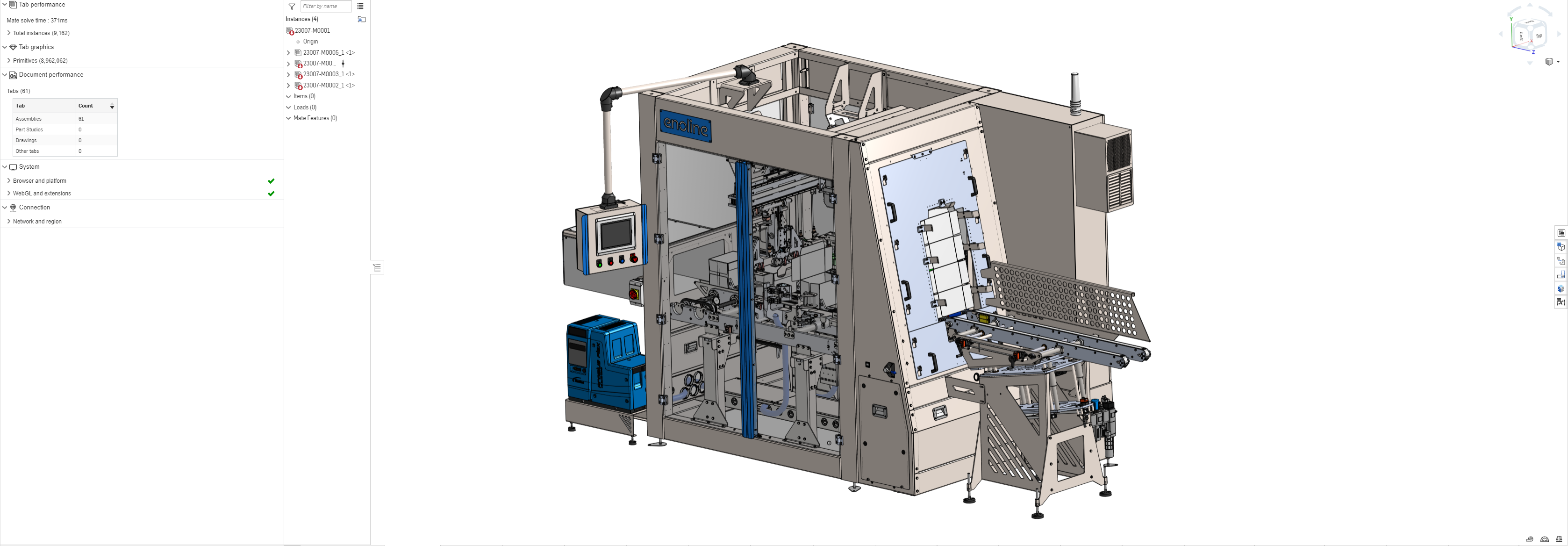
1
Comments
I was responsible for evaluating Onshape as a replacement for SolidWorks at our company so I can offer some input...
On the performance front, I haven't actually worked with this size assembly in Onshape. However what I can say is that with a bit of planning assemblies will perform the same with "native" files than "dumb" STEP files. So if the performance is acceptable with your STEP file test, it will be similar with native files.
The reason for this is that you can manually control by using versions so you only need to worry about the rebuild time of the parts that are in the same workspace as you assembly.
One thing to be aware off is that assembly mates are always solved for all assembly levels so if you have many degrees of freedom in your sub-assemblies, you may start seeing some slower mate solve times (especially if you use limit in your mates as these are "expensive"). However this can be managed by using grouping or configurations in your sub-assemblies.
Regarding stability, if you are used to SW, you'll be more than happy with Onshape!
Yes, there is the occasional new bug introduced with a release, and I also have a current ticket open related to an "unstable" sheet metal model... My guess is that this is a result what I am assuming was some significant code changes in the sheet metal area to add support for countersinks, counterbores and other "3D" geometry in the flat patterns.
One thing that is very different from SW is that Onshape takes bugs seriously and actually fix things quickly when there are issues. I have reported quite a few things over the last couple of years and even fairly minor bugs are usually fixed within a couple of months at most while more serious ones are fixed in a few days (or even hours), plus some of the issues can be resolved "on the fly" by allowing Onshape to directly get into your document through the "back door" and fixing things (no sending files back and forth over FTP for troubleshooting, etc...). Overall we spend way less time dealing with bugs or lost work in Onshape than we did when using SW.
My experience has also been that using Onshape saves so much time on a daily basis that even if you had a serious issue once in a while, you would still be way ahead! The ability to have infinite undo and access to your history at any time plus branching and merging, is extremely liberating especially at the "conceptual design" stage of a project. I recently did some design on a legacy product in SW and it felt like I was using have my brain capacity constantly trying to figure when to save, when to "save a copy", when to "close without saving" vs "manually reverting some changes", etc... In Onshape you can just go ahead and try things and you can check what your design looked like at any point in time in just a few clicks and look at it side by side with your current state, and restore to any previous state at any time. This ends up saving a lot of time and effort and makes it a lot easier to explore alternate designs.
One thing about "missing features" (compared to SW) that might be worth pointing out is that when I was at your stage (i.e. a couple of weeks of using Onshape), I also though quite a few things were missing. However most of these are actually because the workflows a bit different and I found later that the majority of these have a reasonable (workaround/workflow) or there is a Featurescript that provides the functionality, that was also 3 years ago and a lot of things have been added since so I suspect that your "long list" is actually quite a bit shorter than you think!
Going back to sheet metal, this is the area I found has had the most "glitch" and also has the most "slow downs" so I find myself often having to refrain from creating too many sheet metal parts in a single part studio as the performance just gets unacceptably slow (but it is very tempting because it's so convenient!). Learning the various top down design workflows is a must if you are going to be doing larger projects.
One area you may need to look at carefully is 2D drawings. Not that the functionality isn't good but if you have specific requirements for 2D drawings and the functionality isn't there, it much more difficult to work around than in 3D world. Since you are a French speaker, I'm guessing you are going to be more interested in ISO standards and it seems the implementation of such features lags a bit behind the American standards where the bulk of Onshape users are.
Drawing performance is also a bit sluggish when working with larger data sets so that is something you should definitely evaluate.
I hope that helps and feel free to ask any specific questions you may have!
This is inconvenient that I'm testing onshape and there are some issue with sheet metal at this moment. This is maybe 50% of all the parts I design. This weekend I did some more stress test and I got some more strange behavior with some features... The sheet metal flat pattern tab even disappear some time and I need to refresh the page to make it appear. That will be a good opportunity to see the responsiveness of the Onshape team on this
I did try a little bit the 2D drawing and that is ok for me. Sure, there are a lof of feature missing but I will be able to pass over this.
I don't know... maybe a i get use to Solidworks and I really know his general behavior but I find the software pretty stable in my opinion (3Dexperience is something else :P)
Thank you again for your help in this decision.
The performance is probably my biggest gripe. Some things really slow down. In ProE/Creo, you could have a 700 feature tree. One or two features might be really slow, but the rest fast, even if they are after the slow feature. In other words, each feature is "independent". In OS, the features seem to build on top of each other, when they are on the same body. So if the body gets slow, adding a few simple holes will actually make those holes very slow to regenerate as well. I see this in sheetmetal models the most. I "think" this may have to do with OS using Parasolid, while ProE used something else (I forgot which now).
The PDM system is way better. On ProE/Creo/SW, and I think most others, the CAD system and the PDM system were developed separately, then merged years later. In OS the PDM was developed together with the CAD. They really work well together. That also saves a lot of money, as the other systems charge another license fee for the PDM.
The helpdesk is top notch. Any bugs get taken care of quickly. Users are able to submit feature requests, and some of mine have actually made it in. Problems with modeling (especial when you don't have a coworker with years of OS experience sitting next to you) can be sorted out via help.
The custom features are great. They allow anyone to make their own features. That's above my pay grade, but I have used other's custom features a lot, and really appreciate how OS opened up the whole programming to anyone that is into that.
OS makes it super easy to design "everything" in the same part studio. For real products with multiple subassy's, you must learn the top-down design methods OS provides. If you do everything in one part studio, it will be too slow. Some up-front planning is necessary to break out your design into manageable part studios.
The training is top notch, all built in, and free.
The browser based system is top notch. That alone might negate any of the disadvantages. Not having to install and maintain the system is a HUGE advantage. Although I "think" SW 3d experience is the same?
Branching is another HUGE feature. No one else has that as far as I'm aware (except PTC just added it to Creo, using OS technology). That is so handy for exploring design alternatives.
Working in teams is much better in OS than Creo (with Creo's PDM system). From talking with my coworkers, Creo is a lot better with that than SW.
Assemblies I've gone about as big as about 1000 parts, if you count hardware, and maybe 100 "real" parts if you remove all the hardware. The asm performance is pretty good at that level. That's also about as big as I went with ProE/Creo, and I'd say the asm performance was about the same.
I would def recommend it to most of my former coworkers, and have. I would be slightly hesitant to recommend it to very complicated injection molding companies. The last company I worked at made children's car seats, that would routinely have 3000-4000 long feature trees. The molds were very complicated. I don't know if OS would be able to handle that. The biggest I've gone is about 700 features in one tree, and it was quite slow.
My advice on larger projects is to keep each Onshape document manageable in size and if using Release Management, releasing each Document independently from the bottom up in your assembly structure might be your best way to manage larger assemblies. Some of our more complex assemblies might have up to 5-10 subassemblies within the product structure with each subassembly being limited to maybe 200 parts including small fasteners like rivets and releasing from the bottom up has been the best way for us so far.
I hope this helps and please keep us updated as your journey continues.
About stability, I would like to have your thought about the situation I encounter that do not help me in the decision process. At this moment, on the platform, when you do the feature "mirror" of a sheet metal body with an hole feature on it, the holes from the feature do not mirror as they suppose to do. See picture below for more details. This is a known bug and they are working on it (since 1-2 weeks).
There are workaround but during the time they fix it, I may need to do 35 sheet metal parts with mirror feature. Should I use the workaround and someone else question myself about this wrong workflow in the future when I they come back to my design?
What if I had a lot of parts into workspace in progress, with the mirror feature done before the bugs occur, and now because I do a rebuild, all the holes disappear from the mirror side?
This bug is kind of obvious, but imagine a very large part with very small holes and the parts going into production 300 copy with the missing holes because we did not notice the holes was missing?
Is it a bug I should consider not major? In my opinion kinda major because I use those features several time by day and also that can lead to fabrication error. I do not remember experiencing a bug as critical as this one in Solidworks.
Is it one of a kind bug and I'm just not lucky to experience it 5 hours after using Onshape?
I agree this is pretty major, and this level of "severity" of bugs is quite rare in Onshape so I would say you are very unlucky in your timing! That said I am pretty sure it shouldn't take too much longer for a fix (I'm actually a bit surprised this one snuck past QC and it has taken this long before it's fixed)...
One thing Onshape is generally good at is keeping things "intact" during version updates (part of the reason is that they can run automated tests with "real data" during QC to make sure geometry hasn't changed after an update). I just did a check and I do have some existing mirrored sheet metal parts with holes that are regenerating just fine (but would fail as you are seeing if I created them today):
This means this issue only affects holes/mirror features created since the update and any pre-existing parts would not be affected and wouldn't affect any existing "production" parts. This sort of issue in SW would cause the error to "show up" as soon as you saved it to the latest version (or even upon opening the part) but that's not the case here.
There have been other instances of things behaving "differently" after an update but I can't think of a single example where an "old" document didn't look exactly as I left it regardless of the number of updates since the last edit.
I can definitely understand how this would be concerning as you are evaluating things but definitely not representative of what you'd normally expect.
CAD Engineering Manager