Welcome to the Onshape forum! Ask questions and join in the discussions about everything Onshape.
First time visiting? Here are some places to start:- Looking for a certain topic? Check out the categories filter or use Search (upper right).
- Need support? Ask a question to our Community Support category.
- Please submit support tickets for bugs but you can request improvements in the Product Feedback category.
- Be respectful, on topic and if you see a problem, Flag it.
If you would like to contact our Community Manager personally, feel free to send a private message or an email.
Bug blocking progress on model

Hi all,
I'm currently working towards a model that will be 3D printed in spiral mode/vase mode. As a result I need to make cuts to connect the outer surface of a model. Also, my model is symmetric. If you're not familiar with the process, don't worry about it, this is just a bit of context, but that explains why I'm completely blocked from making progress on this one.
Hence: I've modeled one side of my part, pushed back some surfaces on the mirror plane, and ran a mirror feature on it.
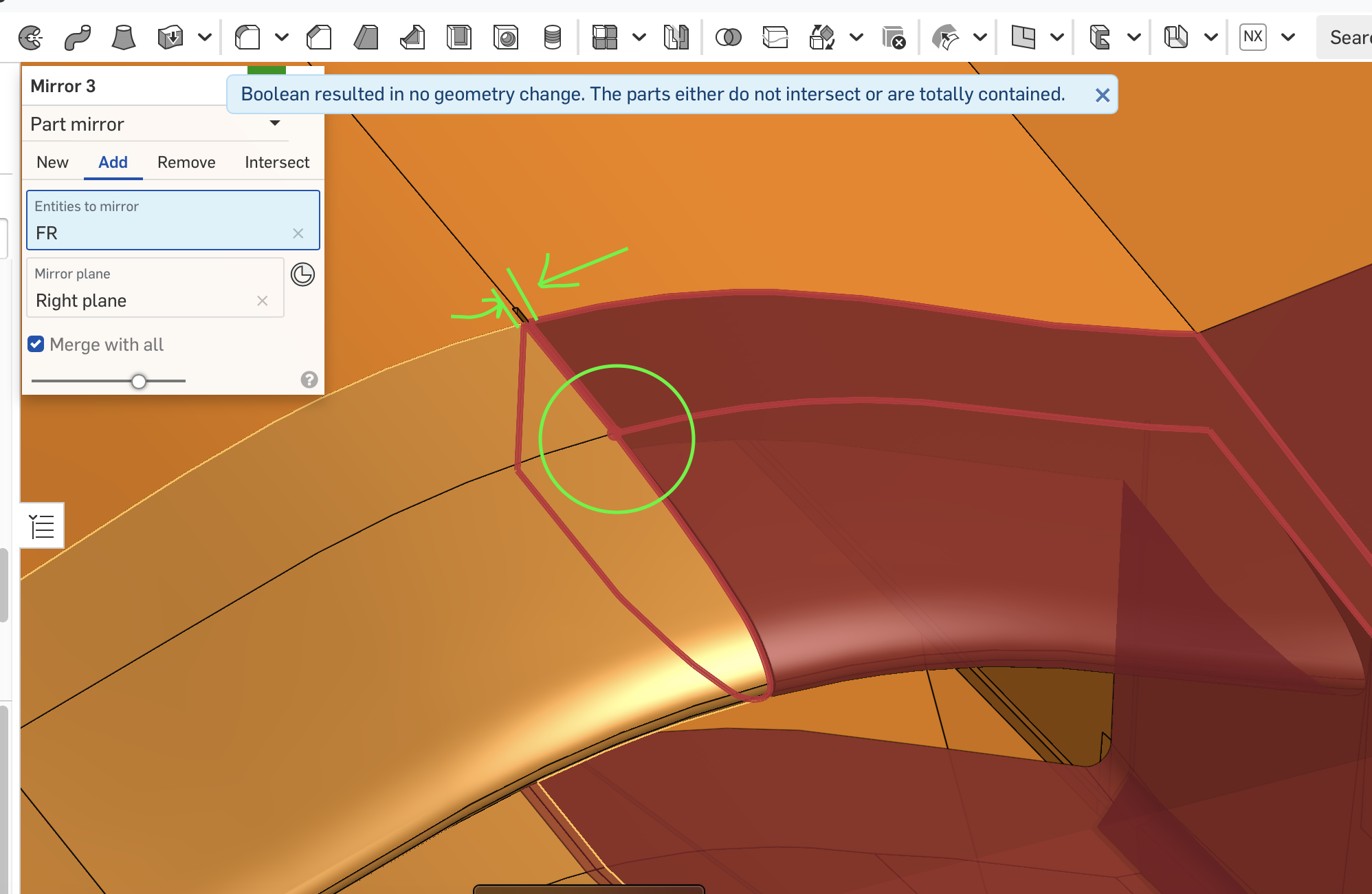
I'm currently working towards a model that will be 3D printed in spiral mode/vase mode. As a result I need to make cuts to connect the outer surface of a model. Also, my model is symmetric. If you're not familiar with the process, don't worry about it, this is just a bit of context, but that explains why I'm completely blocked from making progress on this one.
Hence: I've modeled one side of my part, pushed back some surfaces on the mirror plane, and ran a mirror feature on it.
However, no matter what I do or which approach I take, if I somehow cut/cross the point in the middle of the circle here, the big red DOT, it will not 'Add' the mirror feature no matter what. The side is overlapping, that's not the problem, even enlarging parts or using a boolean instead, it will not join the halves whatsoever.
What is the issue here and how to fix it? Is this kind of thing a known bug?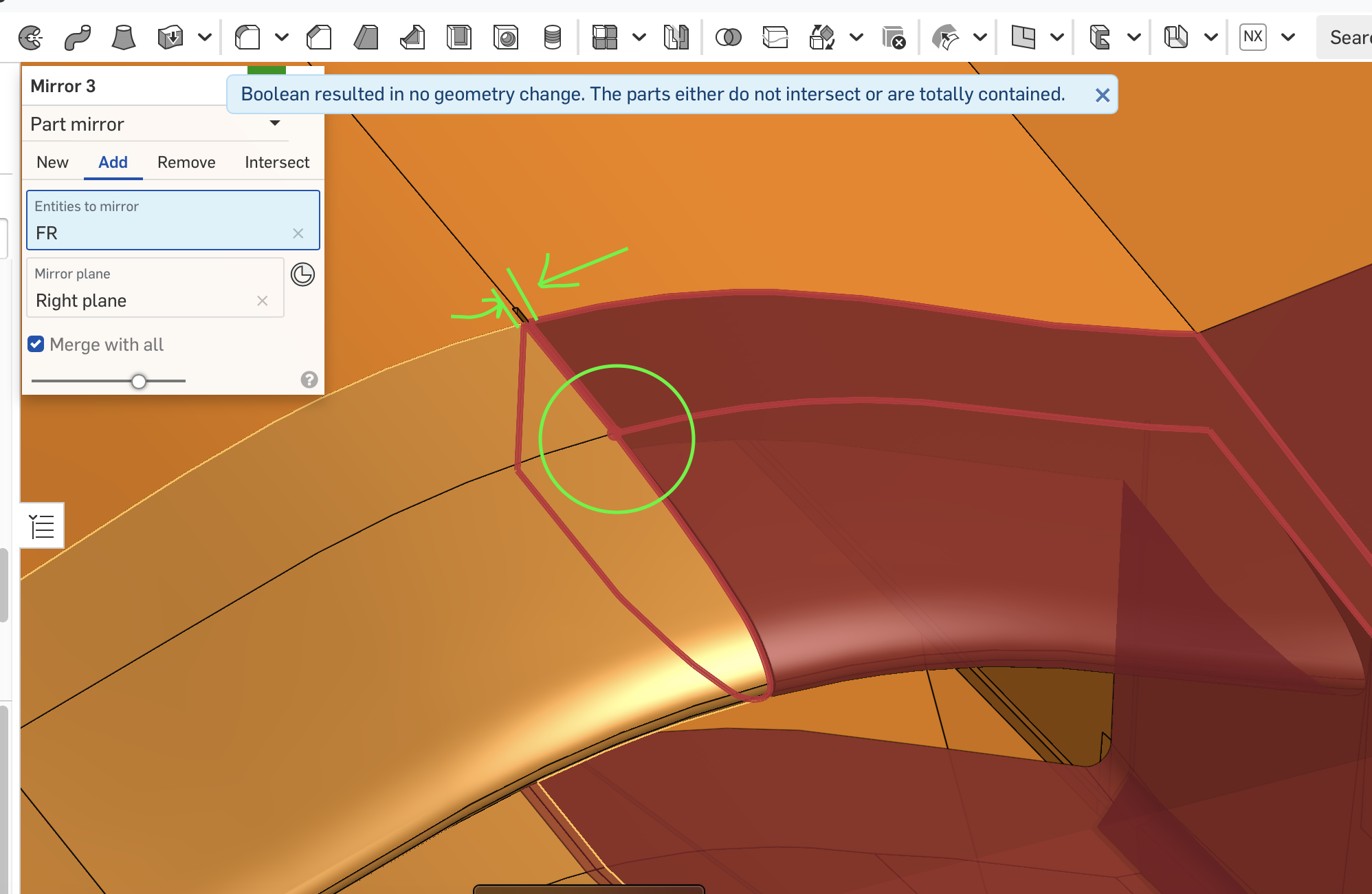
0
Answers
I've tried different ways of making said cut: thicken, move face, extruding. Same with variations of trying to get it to merge: I tried side-stepping the issue with a boolean of a new part. I've tried a new mirror feature instead of re-trying the same old one, and then some.
Interesting observation: I was just messing around with a chamfer, on that edge/through that point, initially it all converged to that one point, but when I changed the chamfer size, all of a sudden it all worked
0,2mm chamfer:
*EDIT*:
Just recreated the convergence when I further reduce the chamfer. It's hard to get a good capture, but here you go:
Turns out that any chamfer smaller than 0,05599 mm will do this
And another thing, what is wrong with sketch 50, every sketch that,s turned red has some fault,s.
I'm not able to reproduce that now, but I did try it that way around as well, but that also didn't work.
Sketch 50 is just a remnant of all the things I've tried to get the cut/mirror to work, and from the top of my head actually the sketch I used to make the cut post-mirror. Hence also all the supressed features in there, I try to go back to clean these kinds of things up as I'm already drowning in features. All-in-all, basically, sketch 50 is nothing to worry about.
Dat de versie met chamfer wel werkte kwam pas na wat spelen met functies
So, what you’re saying then comes down to the software using a point on an underlying sketch of a loft(-guideline) as some kind of reference when generating the solid body for the mirror/extrude/chamfer/etc, causing this bug to trigger?
Because making a cut in my model specifically when that point and that point only is involved causes this to upset the Boolean/mirror.
I,m using Onshape since the beginning and also reported a bug or something weird.
After you report the bug Onshape will come back to you with a solution and explanation of the thing,s that wrong and your document stay,s private.