Welcome to the Onshape forum! Ask questions and join in the discussions about everything Onshape.
First time visiting? Here are some places to start:- Looking for a certain topic? Check out the categories filter or use Search (upper right).
- Need support? Ask a question to our Community Support category.
- Please submit support tickets for bugs but you can request improvements in the Product Feedback category.
- Be respectful, on topic and if you see a problem, Flag it.
If you would like to contact our Community Manager personally, feel free to send a private message or an email.
I have a tileable part that I want to test how it fits together. How do I do that?

in General
The part is hexagonal, and I want to test how it will connect together, but I don't know how to do that. I need to have some way of making sure the parts don't intersect. Does anyone know of a way I can do this? Thanks.
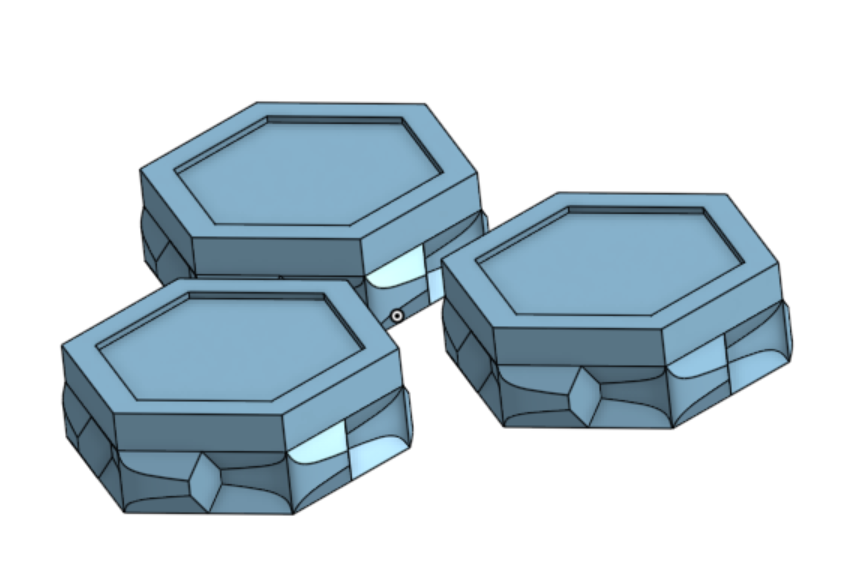
0
Answers
https://learn.onshape.com/learn/course/introduction-to-assembly-design/assembly-interface/introduction-to-assemblies
The first two maybe, but the third never.
Some faces need to have an offset.
And how do you want to produce these part,s, ??
Move faces ot the marked faces a bit out and you have control of the process
You have not shared your document so I cannot know.
And as I said before, if something fit,s exacly it doesn,t fit.
All that said, to be honest, printing is so fast and easy, I'd just print it. In general it's best to get designs to printers asap, with the printer next to your cad computer, while you keep working on improving the design. Keep the prints short and fast, cutting the parts much smaller to just test a specific area of interest, so the print just takes 15 min.
I'd still print asap though. (now). Unless you don't own a printer and have to pay someone else. Then, its a different situation.
https://www.makersmuse.com/clearance-and-tolerance-3d-printer-gauge