Welcome to the Onshape forum! Ask questions and join in the discussions about everything Onshape.
First time visiting? Here are some places to start:- Looking for a certain topic? Check out the categories filter or use Search (upper right).
- Need support? Ask a question to our Community Support category.
- Please submit support tickets for bugs but you can request improvements in the Product Feedback category.
- Be respectful, on topic and if you see a problem, Flag it.
If you would like to contact our Community Manager personally, feel free to send a private message or an email.
Part going through other parts in simulation
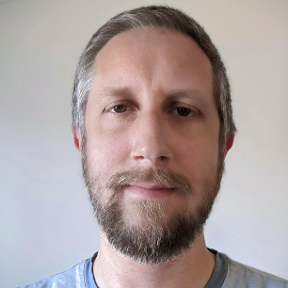
in Simulation
Is there a way to make this stop? Somehow I was thinking the system would automatically assume I did not want to allow parts to pass through another part when flexing. I'm sort of wondering if we can count on the simulation result we are getting. Is simulation considered stable or is it still more of a work in progress that we should not really use to get results for real applications? I also am not feeling certain how the simulation should behave when the mass of an item is manually overridden. For instance, I used a simple block part to simulate a weight and then I manually typed in the weight I wanted it to be in the parts properties. The difference in the simulation is noted. But, if I change the size of the block while leaving the weight the same, the simulation results change in an unexpected way considering the weight should be remaining the same.
Tagged:
1
Best Answer
-
chris_gromek_onshape Member, Onshape Employees Posts: 26
Greetings Shawn,
Without question, there is plenty of room for Onshape Simulation to grow, and general contact is one such area. For now, however, our structural analysis does not include the sort of "load stepping" algorithms which would be required to detect collision post-deflection. Instead, our linear static solver expects that boundary conditions and interactions remain valid before, during, and after the finite element analysis.
Within those range of assumptions, you can be confident in our simulation results. Of course, every simulation is just a "model", and there is more to reality than any simulation will ever capture. However, if you ever find that our linear static solution does not match what you have seen in another finite element analysis tool, please raise a concern. That should not be the case.
As for the question of simulation and mass overrides, I suspect that the value you typed did not have the intended effect. I say that because I have recently received suggestions that, in the future, Onshape Simulation be capable of applying mass property overrides toward rigid, lump masses. It is a good idea, and I am happy to know that at least one more person will benefit from it, but I believe that the weight interpreted by your simulation was a consequence of the Part's material assignment.
If you happen to be conducting a linear static analysis, then adding a force to the entire Part Instance, instead of its faces, will distribute the load evenly throughout its volume. This should give you similar control as overriding its total mass. Of course, if you are performing a modal analysis, then a custom material is going to be your best option.
Best Regards,
Chris Gromek2
Answers
Without question, there is plenty of room for Onshape Simulation to grow, and general contact is one such area. For now, however, our structural analysis does not include the sort of "load stepping" algorithms which would be required to detect collision post-deflection. Instead, our linear static solver expects that boundary conditions and interactions remain valid before, during, and after the finite element analysis.
Within those range of assumptions, you can be confident in our simulation results. Of course, every simulation is just a "model", and there is more to reality than any simulation will ever capture. However, if you ever find that our linear static solution does not match what you have seen in another finite element analysis tool, please raise a concern. That should not be the case.
As for the question of simulation and mass overrides, I suspect that the value you typed did not have the intended effect. I say that because I have recently received suggestions that, in the future, Onshape Simulation be capable of applying mass property overrides toward rigid, lump masses. It is a good idea, and I am happy to know that at least one more person will benefit from it, but I believe that the weight interpreted by your simulation was a consequence of the Part's material assignment.
If you happen to be conducting a linear static analysis, then adding a force to the entire Part Instance, instead of its faces, will distribute the load evenly throughout its volume. This should give you similar control as overriding its total mass. Of course, if you are performing a modal analysis, then a custom material is going to be your best option.
Best Regards,
Chris Gromek
Yes, I think in the future being able to apply an overridden mass to an object would be extremely valuable. In the meantime, it would probably quick and easy for the simulator to provide clear notification while setting up a study that some parts have an overridden mass and that the overridden value will not be used in the study. Right? The entire system leads you to believe overriding the mass means the part now has the assigned mass. everything in the system leads you to believe this is true. For the particular case that brought this up for me, I did end up just hollowing the dummy part out and going back and forth checking the weight until it was where I wanted it. Just using a force in this case was not enough because I needed to simulate gravity on the part using a vertical acceleration combined with a horizontal acceleration.
Do you know why the simulator will often fail to converge when a part deflects? I was struggling to get convergence even though the part was not really flexing that much. in my study, as one part would flex a little, the top of another tall part would move even more. Does the simulator not like to see very large displacement anywhere in the study?
I also am not completely sure I understand your details about parts going through other parts. It seems your saying the simulator simply will not account for flexing of one part being constrained by another part that is very close to it. Based on that, I am struggling to understand how the simulator could possible produce accurate result in any study that involves more then one part. If an item is bolted to a plate in 2 locations, the simulator is not accounting for the fact that the item having the force applied is resting on top of something? So the simulator is running the study as though the item is floating in space and only fixed by the two mated bolt locations?
I agree, a message to the user is a great initial step. I will see to it that we add such a warning before Onshape Simulation's Beta Label is removed.
For your specific case, would you try replacing all of the Accelerations with Forces? If the total load of the force applied is equal to the product of the part's mass and the magnitude of the acceleration applied, then both answers should be equivalent. That was actually one of the benefits we hoped people would enjoy about body-loaded-forces, as opposed to face-loaded-forces, since they behave similar to gravity loads. As an aside, there was some debate as to whether or not we should have named the Acceleration Load as "Gravity" instead, since Acceleration can imply a dynamic event, though we are restricted to static analysis. In the end, we decided to stick to standard terminology.
There are a number of reasons why simulations fail to converge, but three seem to stand out:
- The Assembly is not fully constrained. Often, the Assembly is positioned in static equilibrium, such that it appears to be "balanced". However, computationally, the open degree(s) of freedom as unstable and it is unlikely to properly converge.
- Displacements exceed the linear-elastic range or rotations exceed the small-angle approximation. These two assumptions are part-and-parcel for linear static analysis, so you are correct - simulations with very (proportionally) large displacements or rotations will be difficult to solve. Coincidentally, these often occur as a result of under constraining the Assembly, referring back to #1.
- One or more parts are very thin. This is an active area of development for us, and I hope that it will not be long before we have a robust and elegant solution. As of now, analyzing thin parts is possible, but computationally expensive. Sometimes they become so expensive that it stands in the way of convergence.
As for interactions between parts, the Connectivity Method and Visualization tool located in the bottom half of the Simulation Panel is the best means we have of illustrating how each simulation "sees" part-to-part interactions. As you pointed out, this visualization operates on the pre-loaded system and, under enough load, parts may flex/bend until they intersect. In that case, you can be confident that the parts are likely to collide in real life. However, the solution will not be valid past the point of collision, because this analysis does not take into account the new boundary conditions which arise mid-solve. There are methods that could do this, which equate to slowly "stepping up" the load and solving the system at each increment. Between steps, we could then re-analyze interactions and adjust to new contact regions. However, that enhancement will likely take some time to implement.I hope that helped, but sometimes words are not enough. In that case, please feel free to share your document with me at cgromek@onshape.com. Otherwise, please let me know if there is anything else I can clarify and thank you for the questions!
Best Regards,
Chris Gromek