Welcome to the Onshape forum! Ask questions and join in the discussions about everything Onshape.
First time visiting? Here are some places to start:- Looking for a certain topic? Check out the categories filter or use Search (upper right).
- Need support? Ask a question to our Community Support category.
- Please submit support tickets for bugs but you can request improvements in the Product Feedback category.
- Be respectful, on topic and if you see a problem, Flag it.
If you would like to contact our Community Manager personally, feel free to send a private message or an email.
Splitting part after assembly - is it possible to relink mates?
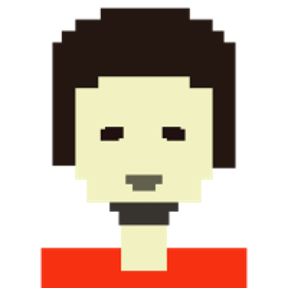
I think my problem is relatively simple problem. Example document: https://cad.onshape.com/documents/e54a188f695469ab600fefe5/w/7ea27d683f3bb7e915a1367e/e/d5536f4b1cbde0ee22c8b95a
As you can see there's a simple assembly, consisting of 4 rods and some case/block where they can slide:

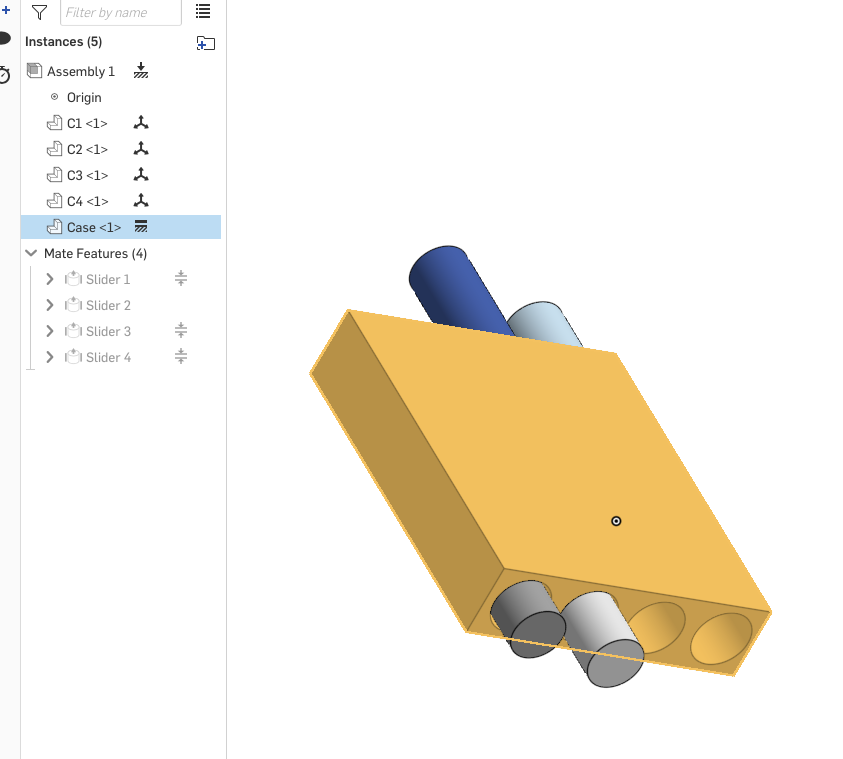
Now, lets say I want to e.g. use FDM and need to split the case part like so:
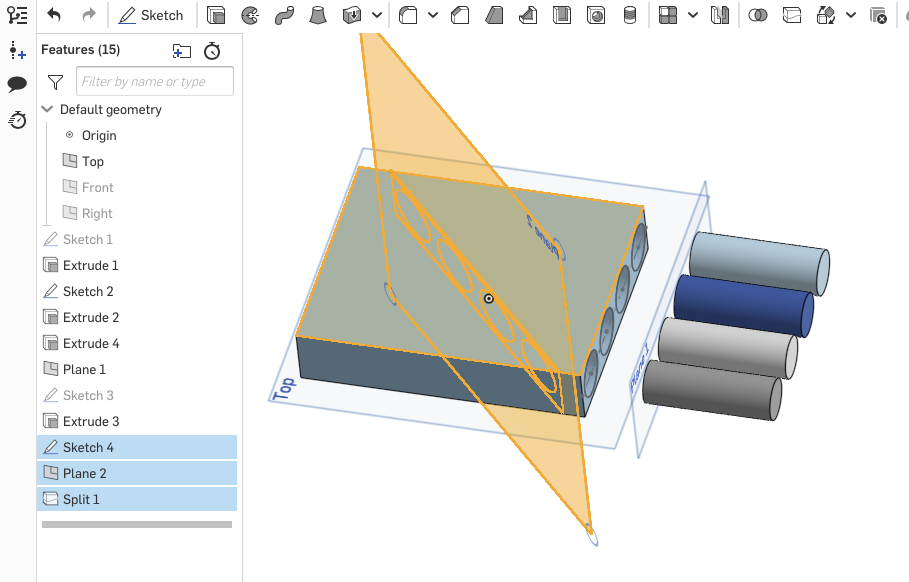
As I expected, this naturally breaks the assembly process as the original non-split part doesn't exist in the Parts Studio:
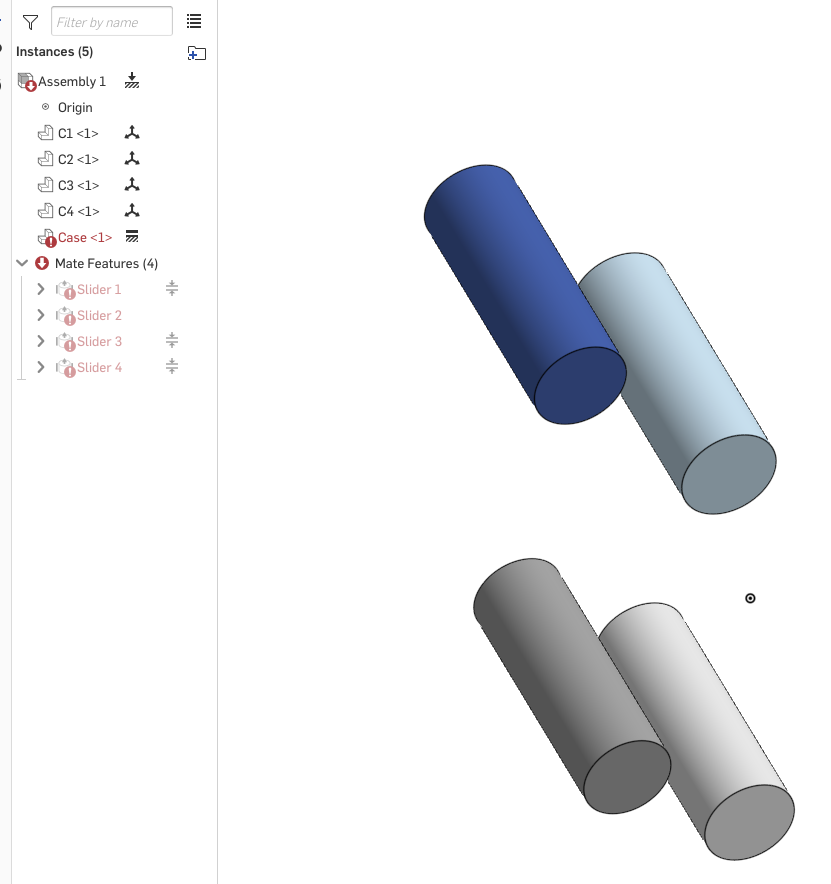
OnShape allows replacing the part with new one and it will restore all mates. However, there's an interesting head-scratcher: you cannot replace one part with two (i.e. a split one). I can insert two of them back and relink one but it will only relink a [small] subset of mates which are present on that fragment of the part:
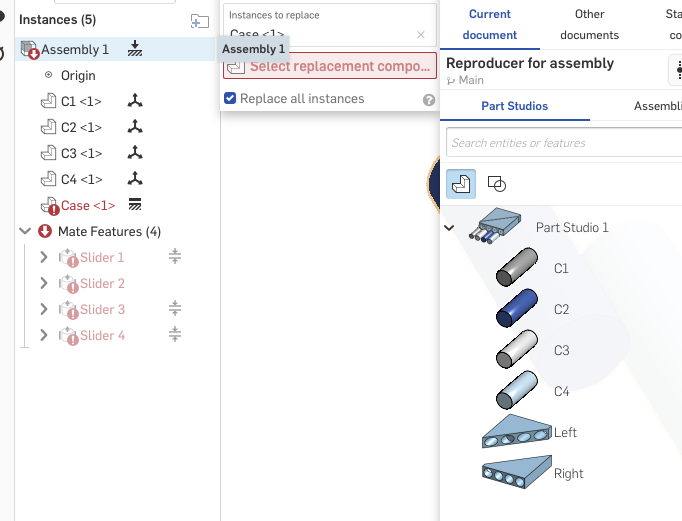
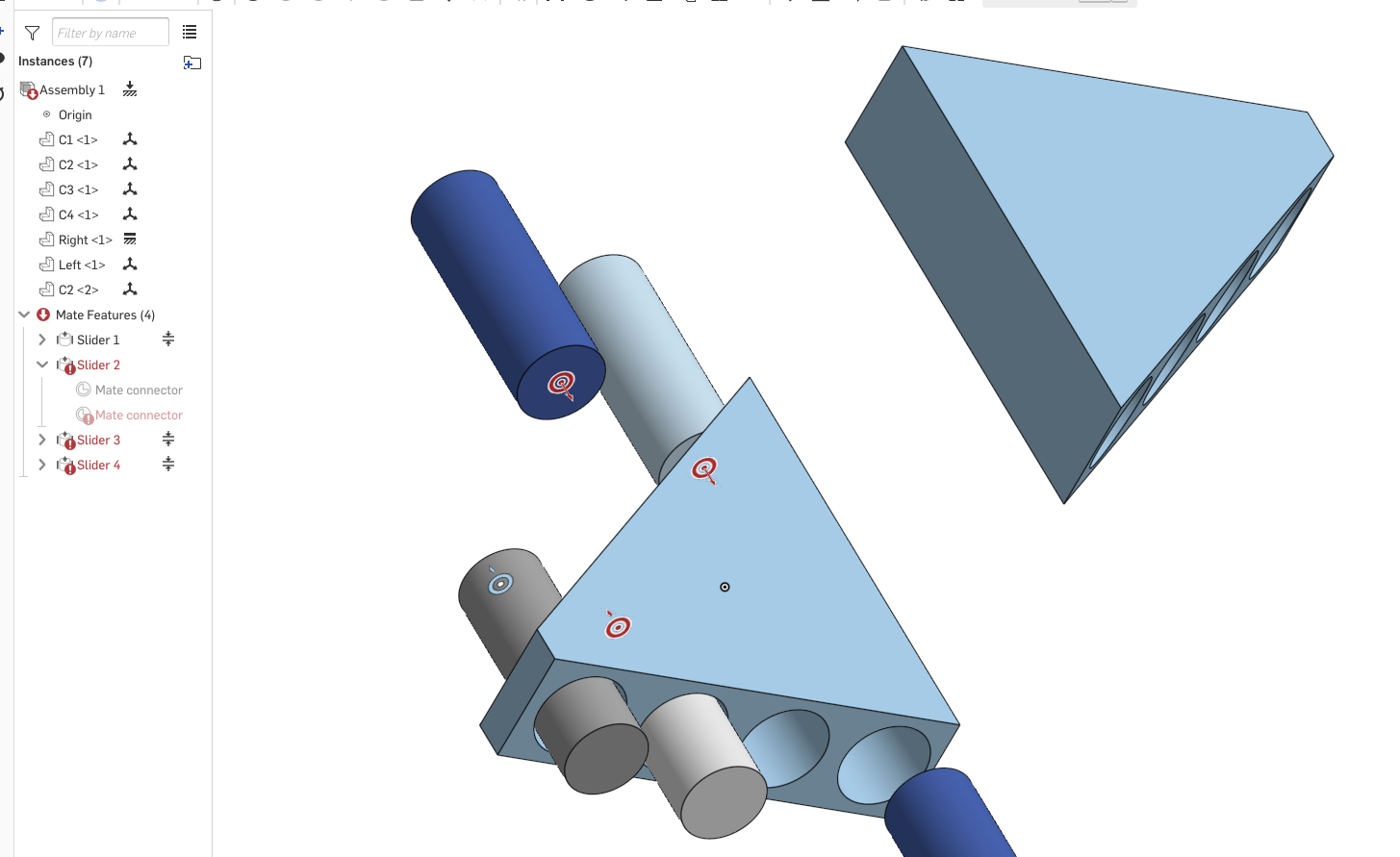
One workaround I found is creating a composite part in Parts Studio and replacing with the composite. However, this solution is also flawed: doing makes it impossible to do assembly of split parts (as the Assembly Studio gets a single logical entity - the composite part).
Is there something I'm doing wrong here?
As you can see there's a simple assembly, consisting of 4 rods and some case/block where they can slide:
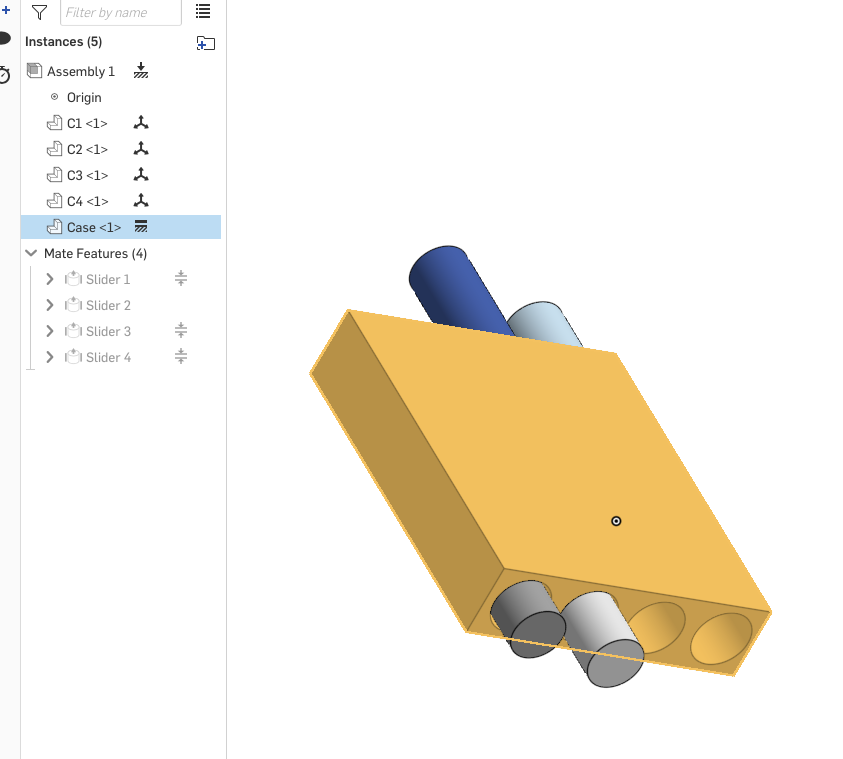
Now, lets say I want to e.g. use FDM and need to split the case part like so:
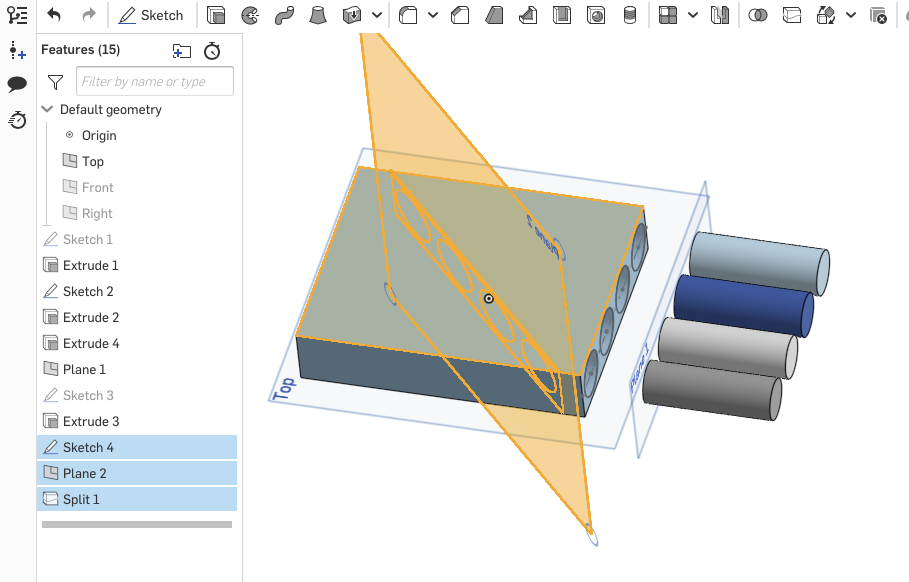
As I expected, this naturally breaks the assembly process as the original non-split part doesn't exist in the Parts Studio:
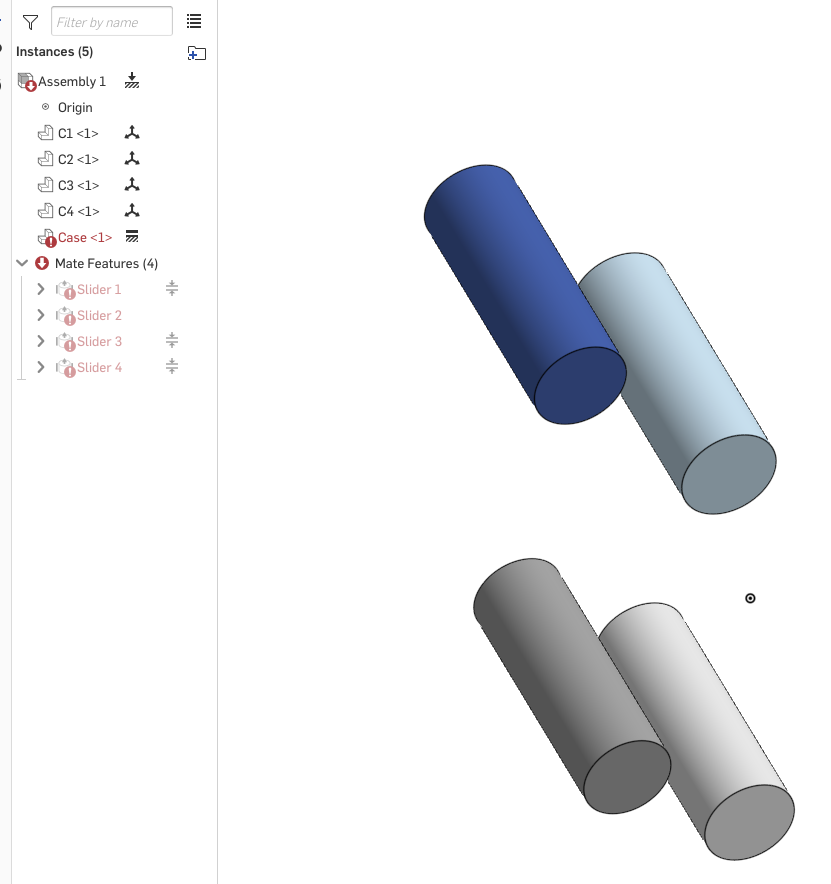
OnShape allows replacing the part with new one and it will restore all mates. However, there's an interesting head-scratcher: you cannot replace one part with two (i.e. a split one). I can insert two of them back and relink one but it will only relink a [small] subset of mates which are present on that fragment of the part:
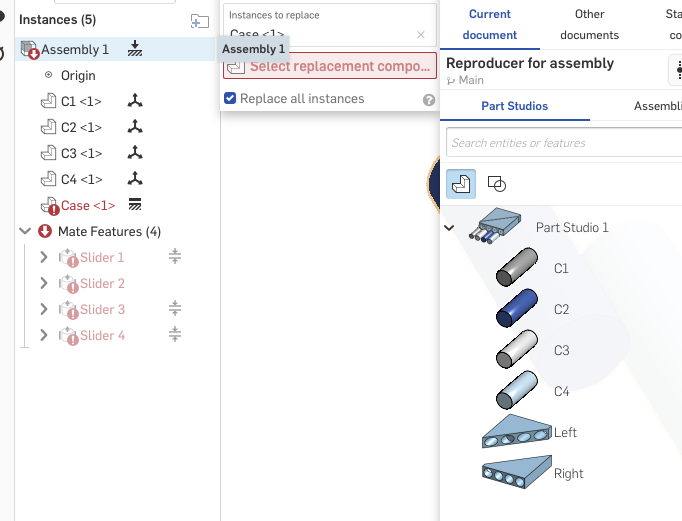
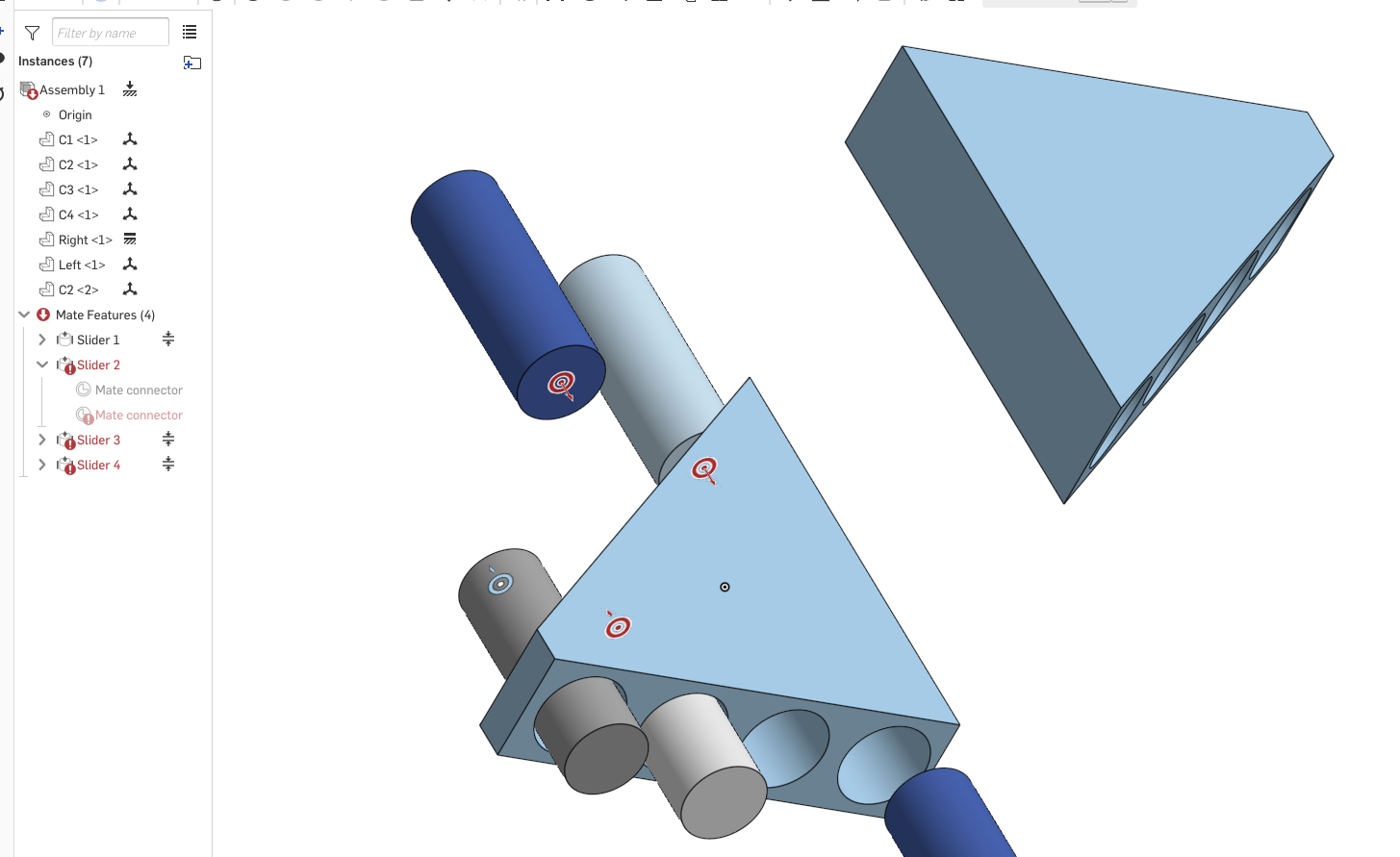
One workaround I found is creating a composite part in Parts Studio and replacing with the composite. However, this solution is also flawed: doing makes it impossible to do assembly of split parts (as the Assembly Studio gets a single logical entity - the composite part).
Is there something I'm doing wrong here?
0
Comments
You could put in mate connectors after the split in the part studio, and have them all owned by the right-side part. Then mate the cylinders to the mate connectors in the assembly. You would have still had to redo your mates, however, unless you had pre-planned to do that.
Coming from software engineering background, this is understandable. However, I think I'm missing an option like "relink all selected to this part" - I don't have a problem hinting CAD that mates just moved somewhere else, this is logical. However, the only option I see is to replace missing part with new one (in which case all mates are linked back as they were), and then manually re-do mating of all other parts for the other side of the split. While in this case with 5 parts total it's easy, doing this with 50+ parts is going to be tedious to say the least
So what you're saying, I should define manual mate connectors in the parts studio(s) for every part, and then use these mate points in assembly to quickly re-do mating if a major change like split of a big part happens? While this will not help me a lot here saving time, it will be a great lesson for the future if this is the case
I guess the magic auto-creation of mates bit me here then.
https://cad.onshape.com/documents/cfc51e9ec1a584a29cd7e254/w/5e19cec11feaa5a72e38acd6/e/5e71e4e2d5c67471812f6dfb