Welcome to the Onshape forum! Ask questions and join in the discussions about everything Onshape.
First time visiting? Here are some places to start:- Looking for a certain topic? Check out the categories filter or use Search (upper right).
- Need support? Ask a question to our Community Support category.
- Please submit support tickets for bugs but you can request improvements in the Product Feedback category.
- Be respectful, on topic and if you see a problem, Flag it.
If you would like to contact our Community Manager personally, feel free to send a private message or an email.
Cannot Hollow Out Airplane Wing in Onshape

Hi,
I am relatively new in CAD modelling and Onshape, so please forgive me if I do something wrong. I am trying to hollow out an airplane wing using the shell tool with thickness of 1mm. However, it just says "Shell did not regenerate properly: Could not shell part with selections."
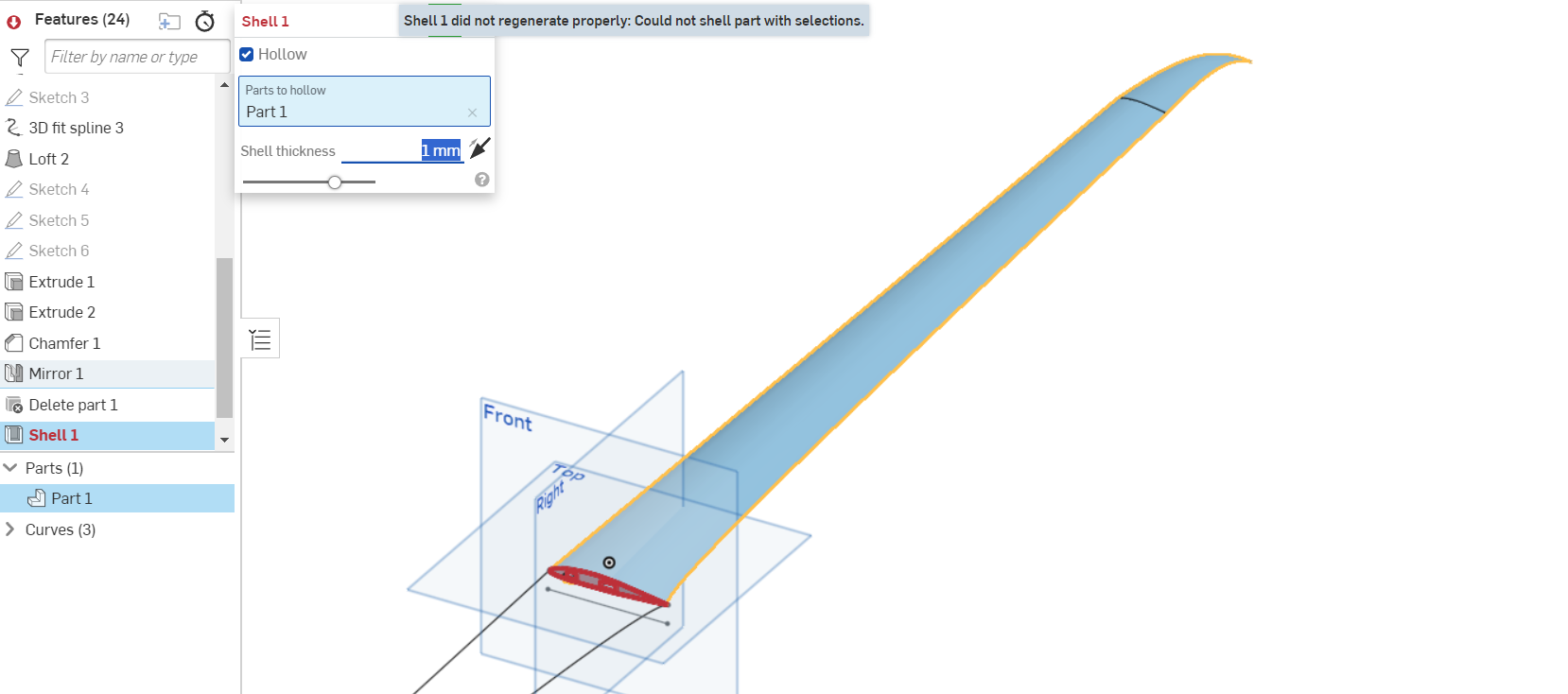
When I use the shell feature on an object without any loft, it works just fine.
The Onshape Project in question is linked below:
https://cad.onshape.com/documents/095333f1d5648663e6ed9298/w/613a00502683658c17564057/e/66be12b516ee5376dd0fdbc5?renderMode=0&uiState=65f4267ecdc0954490e68e50
Would Appreciate any assistance,
Soapy dog




I am relatively new in CAD modelling and Onshape, so please forgive me if I do something wrong. I am trying to hollow out an airplane wing using the shell tool with thickness of 1mm. However, it just says "Shell did not regenerate properly: Could not shell part with selections."
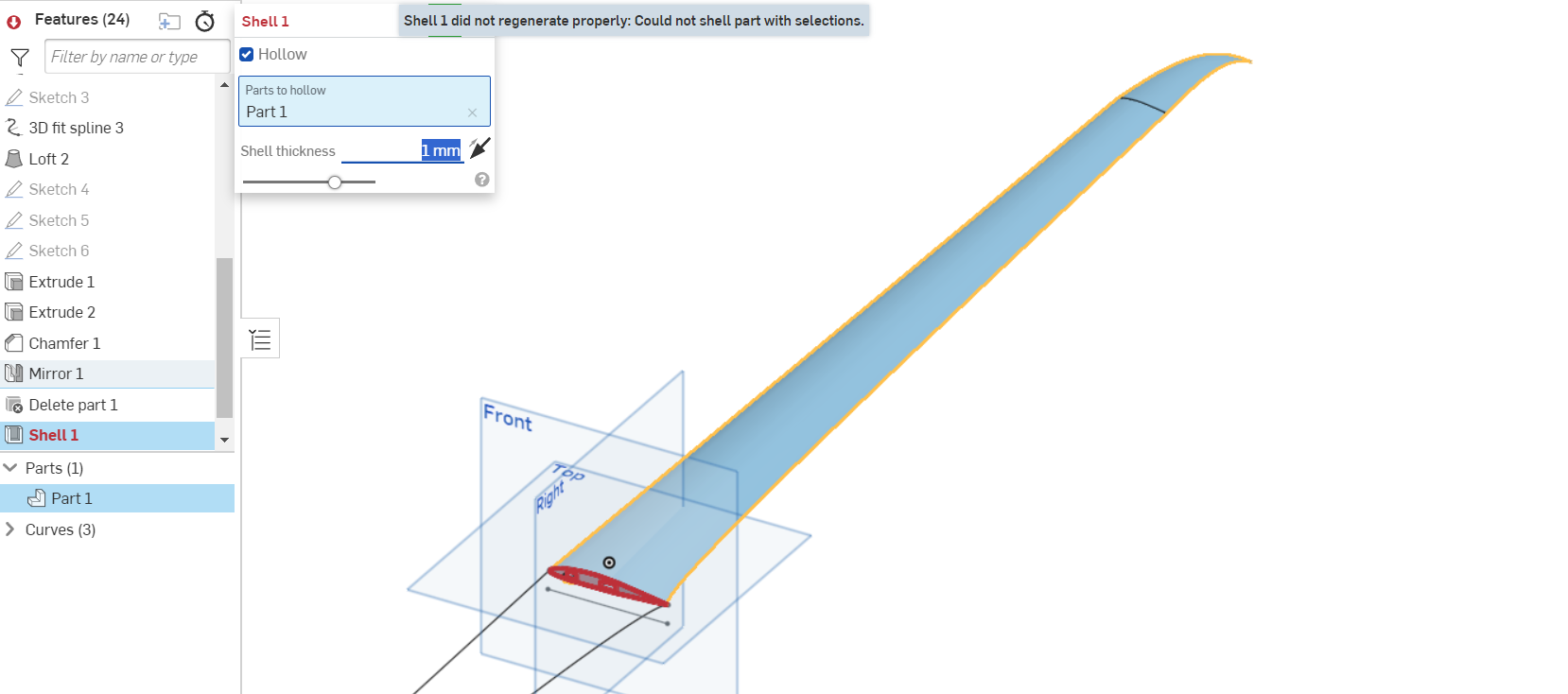
When I use the shell feature on an object without any loft, it works just fine.
The Onshape Project in question is linked below:
https://cad.onshape.com/documents/095333f1d5648663e6ed9298/w/613a00502683658c17564057/e/66be12b516ee5376dd0fdbc5?renderMode=0&uiState=65f4267ecdc0954490e68e50
Would Appreciate any assistance,
Soapy dog
0
Best Answers
-
martin_kopplow Member Posts: 858 PRO
Yeah, that's a difficult shape. It might be a good approach to surface-model that, maybe keep top and bottom separate at the chord for now, and then thicken, unite.
2 -
john_lopez363 Member Posts: 130 ✭✭✭
@Soapydog
Here is one approach! Perhaps not ideal, but it's a work around.
- Create a second set of airfoil profile sketches that is somewhat smaller than the originals. You will need to create the root profile sketch offset from original so that you can retain the notch and tab you've modeled.
- Loft Remove using the smaller profiles sketches.
0 -
rick_randall Member Posts: 402 ✭✭✭
martin_kopplow said:Yeah, that's a difficult shape. It might be a good approach to surface-model that, maybe keep top and bottom separate at the chord for now, and then thicken, unite.I'm with martin on this one. Start with inside profile, loft as a surface, and then thicken. With airfoil shapes, I can tell you the problem issues always seem to show up at the trailing edge ( usually in the form of self-intersecting profiles). working from inside to outside will eliminate most of these issues ( but not always). Also use guide curves with lofts - this seems to make lofts more stable. And as Nick states - model with tiny radii on trailing edges.Keep going, you will get there. Just wait till you try propellers lol.0
Answers
Even for an experienced user, which I consider I am, this is a difficult shape to work with.
I tested some approaches with a copy of your model and I'm not sure you will be able to hollow it.
@martin_kopplow wrote, a surface-model approach is the best way to go.
Here is one approach! Perhaps not ideal, but it's a work around.
- Create a second set of airfoil profile sketches that is somewhat smaller than the originals. You will need to create the root profile sketch offset from original so that you can retain the notch and tab you've modeled.
- Loft Remove using the smaller profiles sketches.