Welcome to the Onshape forum! Ask questions and join in the discussions about everything Onshape.
First time visiting? Here are some places to start:- Looking for a certain topic? Check out the categories filter or use Search (upper right).
- Need support? Ask a question to our Community Support category.
- Please submit support tickets for bugs but you can request improvements in the Product Feedback category.
- Be respectful, on topic and if you see a problem, Flag it.
If you would like to contact our Community Manager personally, feel free to send a private message or an email.
Cubic trisection (helicoidal dissections) challenge

I wonder if it is possible to recreate a cubic (or other shapes) dissection using Onshape?
In this thing on Thingiverse, the author made an OpenSCAD customizable version of this: http://www.thingiverse.com/thing:753002
He also provides some links with info, perhaps this paper is the best one: http://www.cs.berkeley.edu/~sequin/PAPERS/2012_FASE_Dissections.pdf
Here's another thing, this author used Solidworks to re-create a particularly appealing Cubic trisection: http://www.thingiverse.com/thing:629887
His inspiration was the design presented by Oskar van Deventer in this video:
https://www.youtube.com/watch?v=fD-zIUYhHps
I have a strong feeling that this is acheivable in Onshape, but I don't (yet) have the necessary skills to do it, so I present this as a challenge (or perhaps it isn't really a challenge) to the more experienced modellers here. Keep in mind that the final object also should have some tolerance added, so that the final design can be 3D-printed and assembled without having to sand the parts.
In this thing on Thingiverse, the author made an OpenSCAD customizable version of this: http://www.thingiverse.com/thing:753002
He also provides some links with info, perhaps this paper is the best one: http://www.cs.berkeley.edu/~sequin/PAPERS/2012_FASE_Dissections.pdf
Here's another thing, this author used Solidworks to re-create a particularly appealing Cubic trisection: http://www.thingiverse.com/thing:629887
His inspiration was the design presented by Oskar van Deventer in this video:
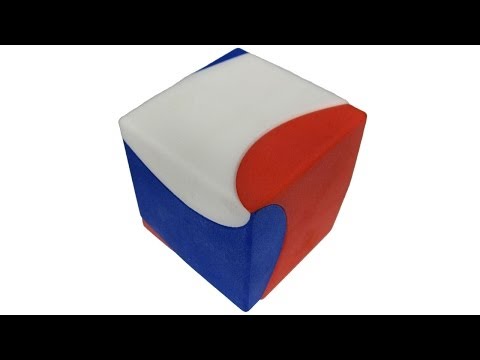
I have a strong feeling that this is acheivable in Onshape, but I don't (yet) have the necessary skills to do it, so I present this as a challenge (or perhaps it isn't really a challenge) to the more experienced modellers here. Keep in mind that the final object also should have some tolerance added, so that the final design can be 3D-printed and assembled without having to sand the parts.
0
Comments
The three parts don't meet to a point at the cube corner (if you see what I mean), but I'm certain it is otherwise correct and workable. Some more experimenting, and I could probably also get it to look like the example.
The solution is easy enough once you figure it out, but basically it involves three helices that share a common axis which is a line from opposite corners of the cube. Then a cutting profile is swept along each of those helices, and hey presto!
What is slightly non-obvious at first, is that the very first cutting sweep does not split the part in two, it is still one solid part. The second sweep cuts it in two, and the third cuts it in three.
I think the problem is that Onshape does not support splitting by multiple surfaces. I can create the three required helical surfaces to split with, but since the cube stays a solid part if I try to split with just one of these surfaces, it isn't really feasible. Being able to simultaneously select all three surfaces to use as splitting tools would have fixed the problem (I think).
To further elaborate, my "solution" was to create a profile normal to the end of the helix, and then sweep that to carve a helical slit in the cube. It still stays a solid after the first sweep, but then the second and third sweeps will actually split into multiple parts. This leaves some odd surfaces at the corners, but it still works when the helices start at 0, 120 and 240 degrees (they are always offset by 120 degrees). However, to recreate the trisection in the video, they need to start at approximately 25, 145 and 265 degrees, but doing that causes one of the sweeps to fail.
I'm not entirely positive that this is unfixable, but I am quite sure the problem would have been solved if splitting could be done with multiple surfaces.
Would you be willing to share your document with the surfaces? I'm wondering if you could use a loft between the multiple surfaces to stitch them together, but I haven't gone through and figured out/seen the geometry yet.
However, keep in mind that I might have done something wrong also. The three cut surfaces aren't actually used for anything now, I just added them to illustrate how I think they should be. Instead, I had to sweep a profile to cut the part, as you can see.
To get the cube close to what I'd really want, I think the helix_start_angle variable needs to be somewhere around 20 degrees, but as you can see, if I do that one or more of the cutting sweeps break.
However, since the cube cannot be split in two parts by just the one helicoidal surface, I'd assume that means you will also have to implement split by multiple surfaces at the same time? Or did you think about some workaround to somehow connect the splitting surfaces to allow them to be used in the same splitting operation?
Thinking about it more, if you turn the 3 surfaces of one face into 2 surfaces each with two faces, then the split should succeed.
I'd still like to see splitting by multiple surfaces, though. :-)