Welcome to the Onshape forum! Ask questions and join in the discussions about everything Onshape.
First time visiting? Here are some places to start:- Looking for a certain topic? Check out the categories filter or use Search (upper right).
- Need support? Ask a question to our Community Support category.
- Please submit support tickets for bugs but you can request improvements in the Product Feedback category.
- Be respectful, on topic and if you see a problem, Flag it.
If you would like to contact our Community Manager personally, feel free to send a private message or an email.
Tie-Rip / Cable-Tie / Zip-Tie FS?
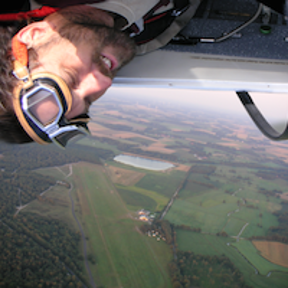
Has anyone ever considered making a FS for creating Tie-Rips? They're such a common thing in tech.
They all have similar shape, and only differ in width and lenght. There should be a way to create them from a cross section of what the're meant to hold, shouldn't it?
Tagged:
2
Comments
Not aware of it but that's a pretty neat idea!
We use a configurable model with config variables so we can do any rectangular and circular shape which is "close enough" but a FS that would take a path and generate the right geometry would be really cool!
That would really be pushing beyond my FS skills though so it would probably take me forever to come up with that! I'm also not sure how it would work in BOMs… Right now with the newly added "exclude properties" we can finally have all of the ties show up in one line on the BOM regardless of the shape they are in, which is nice!
Yes, the exclusion from BOM is probably very helpful with this. I would still want to know how many ties are in any one design. I was thinking about making my own configurable ties yesterday, but today it struck me and I thought: "Hey, I probably know about less than 5% of all FS existing, so chances might be it already exists!"
Unfortunately, I am not good at scripting myself. :0/
Sounds like the same issues I had when making hose clamps, except hose clamps almost always stay round. If you get these issues resolved, keep us informed please - I'm curious about the workflow. Thanks
If you assume it's going to stay round then using a config variable and the new "exclude" option works great.
You can create a single hose clamp model with configuration for band width and length (that are not excluded) and a config variable for the installed diameter and then you can change the size as needed in you assembly without having to replace the part or anything…
Hey Eric, That is the way I do it with hose clamp configurations, as of now - but it's the workflow for configuring odd shapes, that interest me. Would it be better to have a separate file for each shape (e.g. square,triangle oval), or would it be better to bundle them into one part using configs and lots of suppression? Which begs the larger question - from a library stand-point, which workflow is better practice, (many simple parts, vs. single part with lots of configurations)? Any ideas anyone? Sorry if this is starting to go off topic. +1 vote for zip tie F.S.
I wouldn't add an oddball shape to a library part... Instead I would derive the original (maybe in a special config that doesn't include the "path") into a PS in doc where it's used.
Since we don't release OTS parts you can give it the same PN with no conflict. It won't group with others in the BOM but until now it wouldn't anyway...
… but reading the quantity required for an assembly from the BOM would be one of the main points, wouldn't it? For me, all cable-ties of he same size (and thus PN) are just configurations of the same part.
As for how to incorporate the odd shape of a cable-tie, I don't think having a set of pre-defined shapes will work well. I rather think of a basic geometry that doesn't geometrically change such as the 'lock' part of it and maybe the puller part that has no ratchet, then an input curve, ideally derived from the cross section of the parts that need to be tied, and someting to define the plane for the curve. A mate connector comes to mind here.
It would almost be like inserting a standard part: Select type (Width) from the cable-tie insert dialog, specify location (Mate Connector) then click all parts that need to be included in the loop. X-Axis of MC defines the 'lock' position. Direction of the loop could be reversed the usual way.
I think you would need FS on the assy environment for what you describe to work.
Best option I can think of right now would to add each new weird shape as a config in the one source part using a context. It might get hard to keep track of what's what though.
I'm not sure how much value a custom feature would add... Maybe it could save a bit of time generating the sweep path (using similar logic to the belt FS) compared to manual sketch
Thanks for the reply Eric & Martin,
So what I'm thinking, is to create the "library/starter" part as just the locking end with the tag end, and maybe a very small portion of straight tie, then after deriving into a second part, sweep this (tie) profile using whatever contour it takes - and this second part, is the finished usable part. The "starter" part could contain all the various configs (for width,color, & size). - and the final part would reside in the project document, and have all necessary BOM data.
I could actually live with this simplistic approach (I'm talking about hobby use, not making F.S. for pro users), and not just for zip ties, but other things that have odd shaped profiles as well. Good discussion, got me thinking.
https://cad.onshape.com/documents/b66dae2007cb3b004054b9e0/w/d60018ab48d0c8c035b56355/e/a66a38a2b1781dab1b4e81a9
Haven't figured out the new way to link yet, just copy/paste into URL line ( 2 parts & 1 assembly )
This example is crude - and was kind of time consuming , but the results were good enough for me. I'm sure someone with F.S. skills could streamline and automate the whole process - but sadly I'm not that guy.
I've tried to use the routing curve FS Greg recently posted (see link below). The fun thing with this is that the excess lenght follows the calculated circumference, so you can see wether your chosen zip-tie's length is sufficient (still need to implement a blocking mechanism, though). After inserting a Zip-Tie into an assembly, shouldn't it be possible to edit it in context and create a new configuration while we're at it?
https://cad.onshape.com/documents/d9da0bbff6cc563c9d3cc1f3/w/4680e5b7b7881e74bbe00ef7/e/7fed6c1515d45a79e908f881?renderMode=0&rightPanel=configPanel&uiState=66c336d80978a47396567882
To play with it: Open the ROUTING CURVE FS, click of FINAL, then move one of the for vertices.
(It's a pity I cannot upload a video here)
In an ideal world, I'd insert a new zip-tie into my assembly in default configuration, which would be "widest possible loop", position it, click to select the parts to be bound, then pull the end of the tie with my mouse pointer, and watch the tie conforming to whatever volume I had previously selected, and automatically generate a configuration of the original zip-tie part, count one up on t QTY in BOM … ah, I'm dreaming again. ;0)
Unfortunately:
…. so the approach of configuring them in context does not currently work.