Welcome to the Onshape forum! Ask questions and join in the discussions about everything Onshape.
First time visiting? Here are some places to start:- Looking for a certain topic? Check out the categories filter or use Search (upper right).
- Need support? Ask a question to our Community Support category.
- Please submit support tickets for bugs but you can request improvements in the Product Feedback category.
- Be respectful, on topic and if you see a problem, Flag it.
If you would like to contact our Community Manager personally, feel free to send a private message or an email.
I've been going round and round and round this spiral problem.
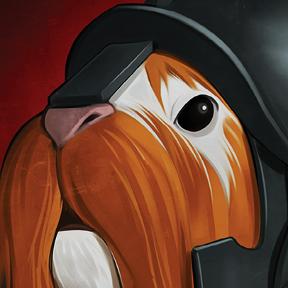
Morning all,
This wonderful drawing has just landed on my desk:
Where the spiral grove is:
I have tried
It's awesome but can't seem to work out how to get the spiral tighter. It starts too far out from the center.
I have manually constructed a spiral and you can find my efforts here (You can see the FS Script version in the versions tree).:
So a couple of questions:
Is this actually possible to model as drawn. I'm mostly struggling with the start and the end. Ideally it needs to be a smooth transition so that the dimensions shown in the section view of the drawing (uploaded into the linked doc) are accurate. As you can see I'm getting a squiggle.
Have I just missed an option in the feature script to set the start distance from the origin?
Best Answers
-
Oliver_Couch Member Posts: 230 PRO
What's the purpose of the modeling? Does it need to be physically accurate or just representative?
If just representative, rather than a true spiral - being a line of smoothly decreasing radius - you can do a pretty good piecewise approximation by doing a series of tangent arcs with decreasing radii.
YoYou could setup a variable called #Pitch, then set the radii of the arcs to pitch*n/m
WWhere N is the sequential number of a given arc, and M is the number of arcs to make up 360°
0 -
steve_shubin Member Posts: 1,116 ✭✭✭✭
@Ste_Wilson
In PART STUDIO 1, Take a look at Sketch 4
I probably made a document here that's way more features than necessary. But it’s late and this is all that has come to mind
If you go into edit of Sketch 3 and make sure that only Curve 1 is showing, you'll see that from the centerpoint to the first part of the spiral is 12 mm (0.472 inches). It shows in inches because for some reason I can't figure out how to get it to show in millimeters.
The remaining 3 distances between the spirals are all 15mm (0.591 inches)
I'm not sure but I think that's what your diagram was looking for.
So what I had to do was set up everything except for the very last feature (Sketch 4). Then I went into Sketch 1 and turned on the FINAL button. Now I originally set the diameter in Sketch 1 to 114 mm by using (3 x 15mm + 12mm) x 2. But this gave me a distance of 14.25mm between the outer 3 wraps of the spiral. So, I just guessed that the diameter for the circle in Sketch 1 should be increased to 120mm in order to give me the distance of 15mm between the outer 3 wraps in Sketch 3, and by chance, that worked. I got a distance of .591 inches (15mm) as displayed in the Measured Value feature - that is, the feature just before Sketch 4.
Now In the last feature - Sketch 4, as far as those two small fillets, I couldn't figure out what your drawings were calling for because it's kind of late and my eyes are not working as good as they should, so I just punched in a number and you could change that to whatever you want
Probably way more involved method of arriving at a solution then necessary
Someone like Michael Pascoe could probably do this in about three or four features, or maybe even less — who knows
Anyway, for what it’s worth, here is something
https://cad.onshape.com/documents/8c572d2d91650b52eb553864/w/83050318ceb7545e5ddcfd62/e/5c040efeb8490d152574d633
2 -
romeograham Member, csevp Posts: 715 PRO
Another approach is to use the standard Helix feature. A spiral can be made by projecting a conical helix onto a plane - so you can use the Conical Helix options in Helix to create a 2D spiral. Using layout sketches & measured variables (as you have) you can achieve the geometry with very few features. Have a look here:
4
Answers
What's the purpose of the modeling? Does it need to be physically accurate or just representative?
If just representative, rather than a true spiral - being a line of smoothly decreasing radius - you can do a pretty good piecewise approximation by doing a series of tangent arcs with decreasing radii.
YoYou could setup a variable called #Pitch, then set the radii of the arcs to pitch*n/m
WWhere N is the sequential number of a given arc, and M is the number of arcs to make up 360°
From the rather ridged spec from the qualification provider the students have to produce THAT drawing. My thought was to get a 3d model together and then the students could create the drawings, so it needs to be possible (if possible) to recreate it. My current problem is getting the center of the slot over the center line for the start and the end in the transition so that the dims are correct on the section view, and the external moderator is happy. They also have to do some 3D modeling of another part. Just a bit of context, the full doc from the awarding body also contains instructions which should work on AutoCAD 14. I'll leave it to you to find out when that was released! :)
So for the section dims to be accurate the slot needs to be centered on those points at the start and the end. I think. Maybe.
I've just fudged the drawi
ng a little, so the current solution is good enough. Any advice on how to get the start and end 'correct' would be good or alternative ways of attacking the problem would be good..Honestly, I'd check with the drawing provider about that. It's not clear to me from what you've shown, and that always means ask.
Assuming it's to be manufactured on a mill though, I'd say it's most likely the sweep of a cutter along an archimedean spiral, with sharp 90° corners at each end of the path - in which case you should do a sweep with a revolve at each end and another sweep 90° to it.
Not going to get any response from the drawing provider. They haven't changed it 30 years!
@Ste_Wilson
In PART STUDIO 1, Take a look at Sketch 4
I probably made a document here that's way more features than necessary. But it’s late and this is all that has come to mind
If you go into edit of Sketch 3 and make sure that only Curve 1 is showing, you'll see that from the centerpoint to the first part of the spiral is 12 mm (0.472 inches). It shows in inches because for some reason I can't figure out how to get it to show in millimeters.
The remaining 3 distances between the spirals are all 15mm (0.591 inches)
I'm not sure but I think that's what your diagram was looking for.
So what I had to do was set up everything except for the very last feature (Sketch 4). Then I went into Sketch 1 and turned on the FINAL button. Now I originally set the diameter in Sketch 1 to 114 mm by using (3 x 15mm + 12mm) x 2. But this gave me a distance of 14.25mm between the outer 3 wraps of the spiral. So, I just guessed that the diameter for the circle in Sketch 1 should be increased to 120mm in order to give me the distance of 15mm between the outer 3 wraps in Sketch 3, and by chance, that worked. I got a distance of .591 inches (15mm) as displayed in the Measured Value feature - that is, the feature just before Sketch 4.
Now In the last feature - Sketch 4, as far as those two small fillets, I couldn't figure out what your drawings were calling for because it's kind of late and my eyes are not working as good as they should, so I just punched in a number and you could change that to whatever you want
Probably way more involved method of arriving at a solution then necessary
Someone like Michael Pascoe could probably do this in about three or four features, or maybe even less — who knows
Anyway, for what it’s worth, here is something
https://cad.onshape.com/documents/8c572d2d91650b52eb553864/w/83050318ceb7545e5ddcfd62/e/5c040efeb8490d152574d633
Thanks for having a spending some time on this. Looks really good.
I'll have a closer look at it when I'm at my desk on Monday but it looks simpler than my method of constructing it as a sketch (so many circles).
Looks like there is some good stuff there for me to unpick and learn.
Here's how I suspect this would've been done originally, without geometric perfection:
https://cad.onshape.com/documents/4f8e24f45f65eaaf27f4c062/w/ab96230b0b9011db3364acc4/e/f7e0a6a549b5bb06b6e75f98?renderMode=0&uiState=670138fb08682a02aba05fcc
I had a half decent sleep. Thought I’d see if I could eliminate the part where I GUESSED at using 120mm instead of the original 114mm that I used in Sketch 1
So in PART STUDIO 1 —— I opened up Sketch 1 and RESET IT for what I originally had - which was 114mm (15mm x 3 + 12mm) x 2
Then I opened up Sketch 3 to see what the measurement was at the outermost part of the spiral and that was 14.25mm (.561 inches)
So then I divided the 15mm that I was looking for at this point, by the 14.25 that I had, and came up with 1.0526315789, which I used to multiply against my original 114mm in Sketch 1, and that gave me an amount of 120mm
So I went back to Sketch 1 and used 120mm for the diameter, and of course, that did the trick — without using guess work.
There is a part studio now called LESS FEATURES
https://cad.onshape.com/documents/8c572d2d91650b52eb553864/w/83050318ceb7545e5ddcfd62/e/86b7bb3599f1f9a9218049e1
But I have a feeling that the person that does the scoring is not going to be onboard with this method I used for making the spiral. Don’t ask me why. Just have a feeling. Maybe it’s because I didn’t get the score I thought I should have had on a test WAAAAAAAAY back in Junior College many decades ago. LOL
Oliver’s method is probably the better one to use
Another approach is to use the standard Helix feature. A spiral can be made by projecting a conical helix onto a plane - so you can use the Conical Helix options in Helix to create a 2D spiral. Using layout sketches & measured variables (as you have) you can achieve the geometry with very few features. Have a look here:
https://cad.onshape.com/documents/b66a67abca299bec2066a7e2/w/202eddb7cc0e31f6a40bca7b/e/7a33cb7ff2154b6d2def3524
Thanks all for your input. It's been really helpful.
I've used the helix function, which upon investigating from your solutions, can be used to generate a flat spiral. I also did the two vertical cuts into the spiral separately as demonstrated in one of your docs which get an nice radius without going off center.
Final solution
https://cad.onshape.com/documents/3e144264874ab82d386c49e8/w/ca8298ec85195144cd3531f8/e/5e6d32d17736f45e08d17c31
Thanks once again.