Welcome to the Onshape forum! Ask questions and join in the discussions about everything Onshape.
First time visiting? Here are some places to start:- Looking for a certain topic? Check out the categories filter or use Search (upper right).
- Need support? Ask a question to our Community Support category.
- Please submit support tickets for bugs but you can request improvements in the Product Feedback category.
- Be respectful, on topic and if you see a problem, Flag it.
If you would like to contact our Community Manager personally, feel free to send a private message or an email.
Sheet metal performance best practices
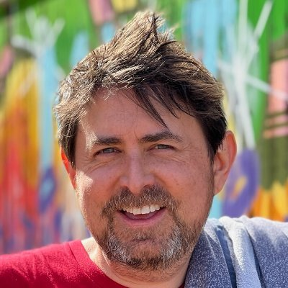
What are the best practices to keep sheet metal performance in check? Completing my latest project so that I could send out for parts became extremely painful towards the end with 20+ second regens. The particular part studio consists of only 103 features and 14 parts. Of which one part is derived and 5 parts are sheet metal ~5 flanges each. Everything else is sketches and references (13) to a single assembly context. Not really complicated at all and all details such as holes and breaks were added at the end. Sorry I can not post an actual link.
I was told by someone that slow sheet metal regens is a Parasolid issue. Is this true?
The only scaleable path forward I can see is to put each sheet metal part in its own part studio. I really don't want to do this.
Here is the regens when I put the rollback bar above all the details and it's also all dominated by sheetmetal features. 10 seconds still feels very unproductive. It seems crazy that a single flange would take nearly half a second.
Comments
Without seeing the actual model it's hard to tell. Perhaps the holes may be trying to check the scope between a bunch of parts. If you explicitly tell the hole feature to only intersect the part(s) you want, does that help?
I have to scope the holes so they don't interfere with other parts. The holes are all either single scope on the sheet metal or two flanges.
I've run into this quite a bit…
My plan for the next project is to make use of the "derive" feature for active sheet metal parts. Create only the key "shared" geometry of your parts in a part studio and then "finish" the parts in their own part studio after deriving them in.
After onshape added "Insert entire Part Studio as rigid" and "Add mate connector to instance origin" I have been moving away from derived parts. The other day I realized I was back in assembly camp after so many years and posted this to my X.
The realization really hurt, but it was true for me and closed an era for me.
I also think onshape are themselves pushing back into this direction considering the recent restrictions and warnings they've put on derived.
I don't want to go back to the old fashioned single part files but finding the balance is very difficult.
Yeah the trick is finding the right balance.
Top down design with layout sketches derived into multiple part studios is going to be the most efficient in terms of regen times but just making the mating parts in a single part studio is the easiest/quickest (until it gets too slow to regen).
Deriving active sheet metal parts now at least allows starting with everything in a part studio and "parting it out" at a later point to add details as a mitigation strategy.
I've found sheetmetal to be slow as molasses on a few projects I worked on. Disappointing for sure. Creo would hardly ever bog down on anything. Maybe it is that parasolid kernal, I have no idea. I know Creo uses its own kernal from the late 80's I guess. What I did that helped a lot was "finish" the sheetmetal model immediately after the main shape with bends was all finished. Then, put the holes/slots/etc afterwards. This removes them from the flat pattern and speeds regeneration. I found the vendors don't want a flat pattern anyway, they unfold the step model in their own software. Also now, hobby places like sendcutsend accept step files (before they only accepted flat pattern dxf).
Interesting. For some reason I was self-insisting that I keep those flat patterns valid. Ironically though sendcutsend lately has been vomiting on STEP and I've had to use flat patterns with them.
Oh, in my case I couldn't break up my model even if I wanted to. My main chassis was all one piece of sheetmetal 6 feet tall and 3 feet wide with hundreds of holes in it for PEM fasteners, rivets, etc.
I guess one of the most important factors in wanting them in one part studio is because of all the connecting rivet/fastener holes?
In case of each part its own studio, you'd have to have one part leading the hole positions, and then create a context for each other part to create the accompanying holes in the other parts. Not ideal either.
I've yet to find the ideal way of working for sheet metal assemblies as wel, so just joining the thread
That was the only thing I sometimes mis Autodesk Inventor for: bolted connections created a chain of fasteners and the proper holes in all parts all from the assembly interface.
This would be awesome in Onshape as well! anybody aware of an improvement request for such a solution?
@jelte_steur814 ,
There are a number of requests that would need to be done before something like this was implemented.
One of them is "assembly features" and there's also "Featurescript for assemblies".
I have used the SolidWorks implementation of "smart fasteners" and while it did mostly work it had a tendency to be a bit flaky (and quite slow if I remember correctly, but it's been a while).