Welcome to the Onshape forum! Ask questions and join in the discussions about everything Onshape.
First time visiting? Here are some places to start:- Looking for a certain topic? Check out the categories filter or use Search (upper right).
- Need support? Ask a question to our Community Support category.
- Please submit support tickets for bugs but you can request improvements in the Product Feedback category.
- Be respectful, on topic and if you see a problem, Flag it.
If you would like to contact our Community Manager personally, feel free to send a private message or an email.
Custom properties setup in Onshape
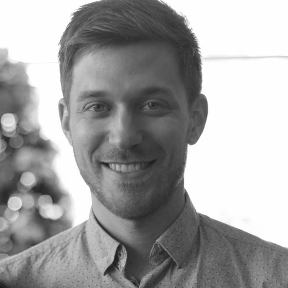
Hello!
We are looking to setup our Onshape account to a potential migration from solidworks/3dexperience. We take this transition for an opportunity to upgrade our standard and CAD methodologies. I would like to know if some people are willing to share there custom properties setup for part and assembly on Onshape ?
We are OEM for packaging equipment. We think the properties need to be kept as simple as possible and let the ERP manage the more "administrative" properties like "cost", "lead time", "alternative supplier".
Also, on Onshape there are possibilities to add properties on a lot of different things! If you have some "must to", do not hesitate to share.
Here is the properties we are planning to setups :
Thank you :)
Comments
I'm confused why you would encode manufacturing steps within the properties. The type is list. Can you give examples of what would be captured in these properties?
How to do document manufacturing processes? Are these part properties or assembly properties? Wouldn't this info normally be part of a part drawing, or SOP (standard operating procedure) document?
Simon Gatrall | Staff Mechanical Engineer | Carbon, Inc.
Hello S1mon! The "important manufacturing step" is to specified steps I want to be respected to obtain the final part. By example, the finish may be "Powder coated" but some time when I want a primer or sandblast step before powder coating. Another example is about aluminum anodization, often I want a glass bead #120 treatment before anodization to obtain a very uniform finish.
Habitually this is for parts but some weld assemblies can have those properties also.
Of course this information may not need to be a "property" and sometime there are notes in the drawing if more detail is needed. But by experience, the subcontractor may not read carefully those long notes and a short list with the steps needed is appreciated. But I think this is useful in some other way :
Here an example where the steps are shown into my drawings :
At this moment, we are looking to Implement an ERP and we are facing some redondance with "routing" from the ERP standpoint and those properties.
Your Idea to have SOP is a good one!
In practice, this makes a lot of sense, but some would argue that a part drawing should specify only the properties and measurements that you need to guarantee a good part which can then always be assembled into a good product. For instance, your second example specifies laser cutting as the first step. There might be a situation where molding, milling, or punching would create a more accurate, less expensive part.
There are definitely many part drawings that I've done in my career which assume a production process, but I would also be careful never to over-specify something which could prevent a part from being made more inexpensively while still achieving the critical to function specifications that you need.
Simon Gatrall | Staff Mechanical Engineer | Carbon, Inc.
Long lists like that tend to get ignored after only a few months, and most of that information becomes redundant based on your standard fabrication outfits; when you only send to the same 3 or 4 manufacturers, they are expecting Inches. Or you can get creative and write functions that will automatically convert all of your dimensions between Std or Metric without having to redefine the drawing.
Things like Item Number is dependent upon which assembly it lives in. Color can vary across the same part, depending where it is installed.
And you've got "Legacy Item number" which just begs the question: if you're starting fresh, what does this represent?
Typically you only need critical Mass properties, material, description, part number.
The rest of that information may be valid, but your ERP system will pull that out depending on which properties are present.
If you start with too much clutter that you won't end up using, then your ERP system will start with 30 columns that never get populated. Then when you start populating new columns with data you find valuable in the future, it just looks messy.
I recommend start small. Narrow that down to no more than 5 critical items that MUST be filled for EVERY part. After that, keep your list as a post-it-note on the wall and maintain "these are valid names". But don't populate every part with all those properties when 95% of the time they won't be filled.
You can always have an ERP column simply named "Extra" which a "Not equal empty" query will return those barely 5% remainder, and do a string compare afterwards. This'll give your SQL/ERP progammers an ease of mind.
I'm on a similar boat as @S1mon regarding Manufacturing Steps being part of the drawing. My approach is that anything regarding process should reside elsewhere, in the case of Manufacturing step it would typically a shop "Traveler" document, the main reason being it's almost a certainty those will eventually change due to newer technology, machinery or facilities being introduced.
Also was wondering why you have 3 different identifiers for the same component (Drawing No. Item No. and Product No)
CAD Engineering Manager