Welcome to the Onshape forum! Ask questions and join in the discussions about everything Onshape.
First time visiting? Here are some places to start:- Looking for a certain topic? Check out the categories filter or use Search (upper right).
- Need support? Ask a question to our Community Support category.
- Please submit support tickets for bugs but you can request improvements in the Product Feedback category.
- Be respectful, on topic and if you see a problem, Flag it.
If you would like to contact our Community Manager personally, feel free to send a private message or an email.
Why are there separate documents for parts studios and assemblies?
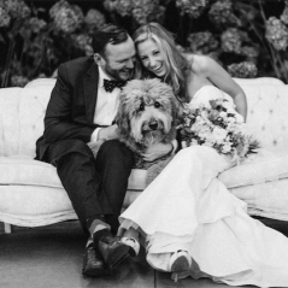
Why are part studios and assemblies separate?
0
Answers
I read the comment from Scott.
I don't disagree. Honestly...I don't really understand what he said and I read it a few times. Scott is obviously way smarter than me
The reason I even ask the question is this-
Today I was trying to convince someone I work with to use onshape. They gave me pushback saying "why would I model in a multi part environment and then have to create an assembly." "If I need to build a mounting plate for a servo motor... I can't import the motor into the part studio, so I might as well use traditional CAD."
I didn't have a good answer....
Maybe someone here can help me out.
For derived parts....it drops them in at the origin and then we are supposed to translate them around? Create mates and then translate based on the mates.....which begs the original question: why are ps and assemblies different entities?
Im sure there is a perfectly good reason why assemblies and ps are separate. I just cannot articulate to my team a good reason why when they bring this as an objection to onshape.
It just seems we should be able to import parts (take a bearing for example) into onshape ps so we can design around that standard part. Currently we go from looking up specifications for standard parts...back to ps to model...back to more specifications...then into an assembly...insert model + standard part. Then when we need to continue modeling....back to the ps BUT there is a gaping hole where the bearing should be in the ps.
EDIT: Additionally- when I import a bearing into onshape....a new part studio is created for the uploaded bearing. Then I have to go create a new assembly to group the bearing components...so I can then import the bearing subassembly into a main assembly. It seems like we should be able to group the bearing components from the part studio....allowing us to skip the step of creating an assembly for this component.
It seems this approach would decrease the ever growing number of tabs across the bottom of the screen.
_Dave_
- Import a derived multi-body part into a part studio (bearing for example)
- Move the derived part with drag handles
- Apply a group mate to the derived components (or the ability to import a derived assembly).
- Mate the derived component. Even if it is just a fastened mate. We could then change the mate type later in the assembly.
There are big gaps in the multi-part design studios when working with imported standard components (that contain multiple parts).