Welcome to the Onshape forum! Ask questions and join in the discussions about everything Onshape.
First time visiting? Here are some places to start:- Looking for a certain topic? Check out the categories filter or use Search (upper right).
- Need support? Ask a question to our Community Support category.
- Please submit support tickets for bugs but you can request improvements in the Product Feedback category.
- Be respectful, on topic and if you see a problem, Flag it.
If you would like to contact our Community Manager personally, feel free to send a private message or an email.
How to calculate the containing volume of a container and how to simulate a stack-able design?

Hi,
I am designing a mould in heart shape (See attached file)
. I am not sure if there are tools to
1. Calculate the containing volume of the mould.
I want to know the amount of water that the mould can contains. From the calculation result, the design will be adjusted according to increase or reduce the size of mould.
2. Simulate to see how good the mould can stack together to achieve the best height.
For example, 10 moulds can stack to get the best-fit, and then to achieve good height for packaging.
My first design with 10 deg in draft angle, but when I printed out with ABS plastic, and stack a mould into the second one, they do not fit perfectly. The gap achieves 8mm. I want to reduce this gap to 1mm (or 2mm).
If there is a way to simulate, then draft angle can be changed to exercise if the design is OK before printing out.
Thanks,
Hung
I am designing a mould in heart shape (See attached file)
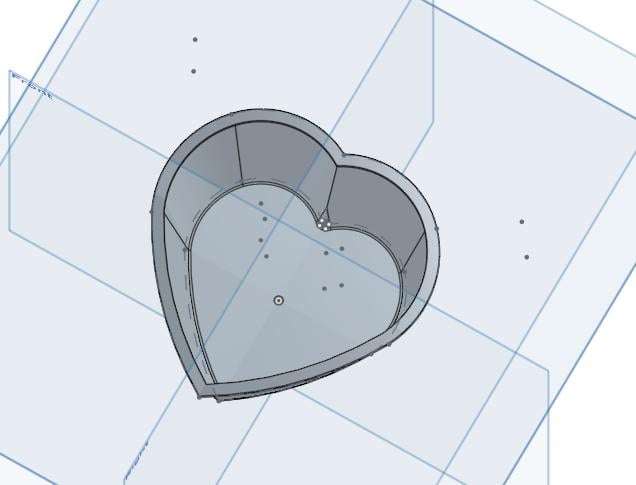
1. Calculate the containing volume of the mould.
I want to know the amount of water that the mould can contains. From the calculation result, the design will be adjusted according to increase or reduce the size of mould.
2. Simulate to see how good the mould can stack together to achieve the best height.
For example, 10 moulds can stack to get the best-fit, and then to achieve good height for packaging.
My first design with 10 deg in draft angle, but when I printed out with ABS plastic, and stack a mould into the second one, they do not fit perfectly. The gap achieves 8mm. I want to reduce this gap to 1mm (or 2mm).
If there is a way to simulate, then draft angle can be changed to exercise if the design is OK before printing out.
Thanks,
Hung
0
Best Answers
-
Narayan_K Member Posts: 379 ✭✭✭
hung_tran744 , To find the volume you have to create a solid body in the cavity.You can find 'Mass porpeties" option by clicking that solid body.Now you can see the volume of the part on mass propety dailog box.
5 -
florian Member, OS Professional Posts: 110 ✭✭✭
If you create the shape with a shell, do the following- Create a copy of the part (Transform > Copy in place
- She'll the part
- Boolean > Subtract > Target: The copy of the unshelled part, Tool: the shell, Check keep tools
- The resulting body is your volume
To test stacking: try creating an assembly with a tangent mate to stack more than one part => check with a section where there is the limiting geometry.
in general: FDM printed parts have tolerances (especially if it's a hobbyist printer). Try filleting the sharp edges (outside at the tip and inside on the heart bumps) and assemble again in onshape.5
Answers
in general: FDM printed parts have tolerances (especially if it's a hobbyist printer). Try filleting the sharp edges (outside at the tip and inside on the heart bumps) and assemble again in onshape.
With the stacking, I did try with an edge and see a result. However, the result does not match to manual calculation, and also the measurement on 2 stacked printed 3D items (Printed 3D items and theory calculation by drawing are matching).
Probably I will try some other edges or surfaces. In general, the method you provided works.
Thanks a lot.
Hung