Welcome to the Onshape forum! Ask questions and join in the discussions about everything Onshape.
First time visiting? Here are some places to start:- Looking for a certain topic? Check out the categories filter or use Search (upper right).
- Need support? Ask a question to our Community Support category.
- Please submit support tickets for bugs but you can request improvements in the Product Feedback category.
- Be respectful, on topic and if you see a problem, Flag it.
If you would like to contact our Community Manager personally, feel free to send a private message or an email.
Options
Is it possible to create a multi body part using mirror? (Does Onshape support multi body parts?)

I have a part that I wish to create a mirror of and have the part and its mirror be considered one part.
I have used all the options available to me under the Mirror operator and it always results in a new part being created.
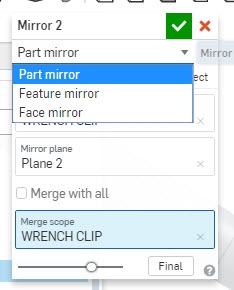
Note: The "Mirror plane" is such that the mirrored result does not touch the part being mirrored.
Note: The "Merge scope" is set to the part that is mirrored.
I have used all the options available to me under the Mirror operator and it always results in a new part being created.
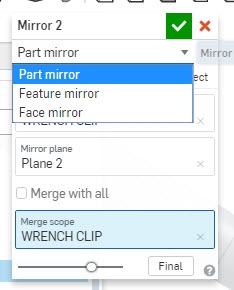
Note: The "Mirror plane" is such that the mirrored result does not touch the part being mirrored.
Note: The "Merge scope" is set to the part that is mirrored.
0
Best Answer
-
StephenG Member Posts: 383 ✭✭✭
I have found a work around... use the proper modeling technique in the first place.
I have never been a fan of CAD products that support multi-body parts, but Onshape with its flexibility to model parts in a "grouping" (a.k.a Part-Studio) seemed like it would support it. The way some 3D operation menu's are written implies the possibility.
I though I would take a short cut and use a "multi-body" part to quickly get the result I wanted.
I thought I would share the process that led me to try creating multi-body part and then show how to do it correctly.
My initial model (highly simplified here) began as a monolithic part.
(I am modeling a part to make a replacement that failed due to a manufacturing defect. The original part was injection molded plastic using dubious material. The "nubs" on the clip features broke off and you could see voids in the material. The quality of the plastic looked like it was sourced from the local land fill with a few ground up tires to give it a uniform black color. Can you guess the country of origin?)
I modeled one clip and then used the Mirror Feature about a mid plane (Plane 2) to create the second clip.
I am going to 3D print a replacement using ABS. Given the vertical orientation of the clips I saw I was going to have a strength/fatigue problem if I printed them in a vertical orientation. A 3D printed part's shear strength is significantly higher in the perpendicular relative to material direction. The clips needed to be printed laying flat (horizontal) on the printer's build table. Therefore, I decided to convert this monolithic model into an assembly of 3 piece parts: 2 clips and a base that would have notches to facilitate the assembly process, i.e. gluing the parts together.
(The process of converting a monolithic part into an assembly of parts in done all the time. It very common to begin a design using a monolithic part to simplify the process of working out interfaces early in a design. Also, it is not uncommon to convert a monolithic part into an assembly because of a manufacturing decision change, for example, converting a design that was originally intended to be a cast, to a weldment.)
I went back to the sketch for the clip and tweaked it to fit a slot. Changed the extrude from "Add" to "New". I noticed that the subsequent mirror produced a duplicate Clip part. Here is where I decided to try to make two clip parts one part consisting of two bodies. My idea was to use the multi-bodied part in a Boolean Subtract to create the slots. Changed the Mirror operation from "New" to "Add" and told it to merge it with the Clip part. No errors just would not do it, and no combination of options would give me a part with 2 bodies.
After submitting this question on the form I realized maybe there was another way a better way... Yep. What I should have done is do a Boolean Subtract of the first clip part and then mirror the Subtract feature. This produced the desired result and I didn't have a duplicate clip part in the Part-Studio.
Modeled the rest of the features, modeled the assembly.
Exported the models for printing...
Came out beautiful, a work of art.
2
Answers
I guess "similar to multi-body part modeling" is not the "same as". My mistake.
It would be nice if Onshape generated an error/warning to the effect that the operation would result in a multi body part and multibody parts are not supported. Right now I can boolean union non touching/non overlapping parts and Onshape says: no problem. The operation is added to the Feature list (history) with zero effect to any geometry in the Part-Studio.
I have never been a fan of CAD products that support multi-body parts, but Onshape with its flexibility to model parts in a "grouping" (a.k.a Part-Studio) seemed like it would support it. The way some 3D operation menu's are written implies the possibility.
I though I would take a short cut and use a "multi-body" part to quickly get the result I wanted.
I thought I would share the process that led me to try creating multi-body part and then show how to do it correctly.
My initial model (highly simplified here) began as a monolithic part.
(I am modeling a part to make a replacement that failed due to a manufacturing defect. The original part was injection molded plastic using dubious material. The "nubs" on the clip features broke off and you could see voids in the material. The quality of the plastic looked like it was sourced from the local land fill with a few ground up tires to give it a uniform black color. Can you guess the country of origin?)
I modeled one clip and then used the Mirror Feature about a mid plane (Plane 2) to create the second clip.
I am going to 3D print a replacement using ABS. Given the vertical orientation of the clips I saw I was going to have a strength/fatigue problem if I printed them in a vertical orientation. A 3D printed part's shear strength is significantly higher in the perpendicular relative to material direction. The clips needed to be printed laying flat (horizontal) on the printer's build table. Therefore, I decided to convert this monolithic model into an assembly of 3 piece parts: 2 clips and a base that would have notches to facilitate the assembly process, i.e. gluing the parts together.
(The process of converting a monolithic part into an assembly of parts in done all the time. It very common to begin a design using a monolithic part to simplify the process of working out interfaces early in a design. Also, it is not uncommon to convert a monolithic part into an assembly because of a manufacturing decision change, for example, converting a design that was originally intended to be a cast, to a weldment.)
I went back to the sketch for the clip and tweaked it to fit a slot. Changed the extrude from "Add" to "New". I noticed that the subsequent mirror produced a duplicate Clip part. Here is where I decided to try to make two clip parts one part consisting of two bodies. My idea was to use the multi-bodied part in a Boolean Subtract to create the slots. Changed the Mirror operation from "New" to "Add" and told it to merge it with the Clip part. No errors just would not do it, and no combination of options would give me a part with 2 bodies.
After submitting this question on the form I realized maybe there was another way a better way... Yep. What I should have done is do a Boolean Subtract of the first clip part and then mirror the Subtract feature. This produced the desired result and I didn't have a duplicate clip part in the Part-Studio.
Modeled the rest of the features, modeled the assembly.
Exported the models for printing...
Came out beautiful, a work of art.