Welcome to the Onshape forum! Ask questions and join in the discussions about everything Onshape.
First time visiting? Here are some places to start:- Looking for a certain topic? Check out the categories filter or use Search (upper right).
- Need support? Ask a question to our Community Support category.
- Please submit support tickets for bugs but you can request improvements in the Product Feedback category.
- Be respectful, on topic and if you see a problem, Flag it.
If you would like to contact our Community Manager personally, feel free to send a private message or an email.
What is the easiest way to make two identical parts with different sized holes at one point?
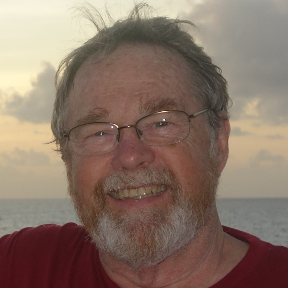
I'm a neophyte, although I once was fluent in SDRC Ideas. I'm designing a mechanism to help learn this new software. The mechanism has two concentric shafts, and two nearly identical cranks. The only differences between these two cranks is the size of the hole that attaches to the shaft ends. Since the shafts are concentric, one crank has to have a different sized hole to account for the concentricity of the shafts. I would like to be able to adjust the length of the two cranks at a later time to adjust them to fit later parts of the mechanism. I've designed one crank "In Context" using the assembled concentric shafts, but when I try to sketch the new crank In Context using the first crank as a pattern, it makes the relevant hole the same size as the first crank, and I cannot figure out how to make it fit the smaller shaft. I would like to be able to adjust the new crank length on one crank and have it change the other length automatically. Is there a better way to do this? Thanks.
Tagged:
0
Answers
https://www.onshape.com/videos/introducing-onshape-configurations
I don't have permission to open the document you shared (could you make it public?).
Regardless, I think this is a really informative use case for configurations. So I whipped up an example on how you could use configurations to solve this type of problem in this document:
https://cad.onshape.com/documents/c465a6b998854e12d5b373ed/w/0fa1d54a1394f41db2e3fc84/e/a1d1e67e4a65f3ebcd8b0949
The document has two different strategies for modeling the two cranks. The first strategy uses configurations and In Context editing both together, and the second strategy uses just configurations.
Configurations + In context
For this design (the "Cranks (In context)" folder), I did the following:
- Create a crank with two configurations: Large hole and small hole, and model the cranks without the hole.
- Assembled the cranks and the shaft, making sure to add one of each configurations, and mate them in place
- Edit the first crank in context, add a boolean with offset to create the properly sized hole.
- Right-click the "tools" in the boolean feature and click configure. This allows the tools to be different in different configurations
- Edit the second crank in context. This takes you back to the Crank Part Studio in the other configuration. Edit the boolean, delete the old tool, click the shaft in the new context
And voila! You have a configured shaft whose geometry is dependent on two different assembly contexts, one for each configuration.Just configurations
For this design (the "Cranks (In context)" folder), I changed the hole size with a single configured dimension.
If your hole is simple, you could model this hole directly in the configured crank's Part Studio and configure the size of that hole.
However, my hole was complicated. I did the following:
- Use derived to bring in all the shaft's geometry, and do a boolean subtract with offset (just like we did in the in context case).
- Next, I utilized the fact that the shaft itself was configured. Right-click to configure the "Shaft diameter" input on the derived, and, in the table on the right pane, set the shaft diameter it to the two values needed for the assembly.
This is a pretty interesting design. The only thing controlled by the crank's configuration... is the shaft's configuration!-----
In both designs, the crank geometry is defined once, and the shaft geometry is defined once. Making a change to that base geometry will update all configurations and all assemblies.
Additionally, in the "No context" version, the crank will update automatically if you change the shaft.
In the "In context" version, you will need to manually update the two contexts in order for the holes to update. However, these updates could let you make changes to the design that are more aware of the full assembly (like, say, changing the angle between the crank and the shaft).
-----
Now... I built this document based off of my interpretation of your description, since I thought it made a cool example of Onshape's newly release configurations. My interpretation is probably off, so please share the document to let us see your real use case!
Configurations are an extremely flexible tool in Onshape's toolbox, so I'm confident we can come up with a good solution for your case.