Welcome to the Onshape forum! Ask questions and join in the discussions about everything Onshape.
First time visiting? Here are some places to start:- Looking for a certain topic? Check out the categories filter or use Search (upper right).
- Need support? Ask a question to our Community Support category.
- Please submit support tickets for bugs but you can request improvements in the Product Feedback category.
- Be respectful, on topic and if you see a problem, Flag it.
If you would like to contact our Community Manager personally, feel free to send a private message or an email.
FEA partners ready?
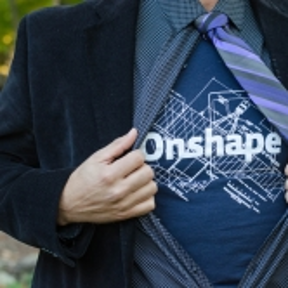
in General
Ive got a poor man's cloud with 3 machines here at work running FEA on an enclosure being designed to resist a 621 psi hydrotstatic overpressure test. It's painfully slow, but really necessary - so we soldier on. Are any partners ready for folks to give their system a try? I'd love to use my Onshape account as a gateway to FEA. I think that would be a great driver of business to Onshape as well. It would be awesome to run the analyses I've been running and will continue to run this week in a much more capable platform. We often stop considering geometry variances because we run out of time in analyzing. There are plenty of more scenarios I would like to run to also question the assumptions we make in FEA studies. Running more scenarios has the advantage of playing one's own devil's advocate and understanding when the FEA model is sensitive to certain assumptions you are making. Are you partners willing to let a hack get an early taste?
0
Comments
Why is taking so long to solve? Is just an internal pressure and lineal analisis with contacts? Should no take more than a few minuts to solve, maybe a good meshing of the part will be more painfull than solving. SW is not good at solving big models, you should try another solver. If you want some advice (or maybe professional work), just get in contact.
Regards
You need a model that can be solved very quick and be enough precise (not necessary 100% accurate), in order to allow you to made several desing iterations, try different configurations, materials or boundary conditions in razonable time. The more quick the model solve, the more time you have to make mistakes and learn from that. So...
1) If your part is simmetric, then use in your simulation. You can reduce the size of your model to a half, and in terms of solving time maybe 5-10 times less.
2) Remove all the small/finishing radius of your model prior to mesh. You must model your part having the FEA in mind (leaving the small radius, simmetries as the last modeling features, so you can roll back easily). This will reduce the quantity of elements and increase his quaility (shape). After the first runs you must check where are the stress hotspots and just add the radius in that areas, the same for mesh improvement (you don't need a perfect mesh in all the part, but must be accurate at least in the stressed areas)
3) Contact is iterative process very time demainding, so you must try to avoid it and replace for another kind of idealizations in the FEA model, at least for the initial runs.
Regards, and we keep in touch
Regards.
Regards.
By the way, if you are interest in the contact areas then all the radius can be removed. Can you show a picture of your mesh maybe?
http://www.simsolid.com/
I recognize that meshing (and preparing the geometry) is the most demanding task in the FEA process, now I have started to work with open source tools like Salome-Plataform, Netgen and Calculix and I can really understand the advantage of comercial codes in terms of features, support and productivity. I'm very anxious to see this "mesh less" process, have heard on the past but never sought on action.
Do you know if is possible to review the recorded webinar in some place?
Regards.
the recording link: https://www.onshape.com/videos/simsolid-partner-webinar
As @pete_yodis says, very impressive. Doing FEA on assemblies is a very time consuming task, and very often at the end you consider "everithing is glued" to get at least a first results and then focus on the stressed areas.
Regards