Welcome to the Onshape forum! Ask questions and join in the discussions about everything Onshape.
First time visiting? Here are some places to start:- Looking for a certain topic? Check out the categories filter or use Search (upper right).
- Need support? Ask a question to our Community Support category.
- Please submit support tickets for bugs but you can request improvements in the Product Feedback category.
- Be respectful, on topic and if you see a problem, Flag it.
If you would like to contact our Community Manager personally, feel free to send a private message or an email.
Options
Improving Lofting
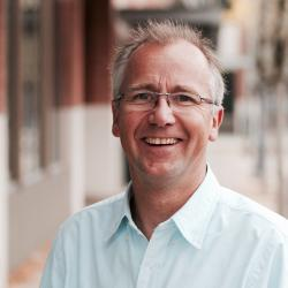
There are a couple of features missing related to lofting.
- Need ability to create multiple planes at a given offset or angle.
- Need ability to join splines, lines and arcs that are touching or intersecting to create a continuous spline.
- Need ability to "straighten" joined splines to get tangent transitions. Basically remove "kinks".
- Need ability to dynamically move spline, line and arc points of the profiles that generate the loft to dynamically adjust the loft shape.
1
Comments
A further desirable enhancement would be some control of the relative weighting of the end profiles vs the side profiles, so that a single feature, with a more straightforward and consistent user interface, could replace both lofts and boundary surfaces from Solidworks.
Raino
I assumed the reason for the straight line in that loft was that the number of sectors (and hence endpoints) was different in the starting profile from the finishing profile, and this made it impossible for the software to infer meaningful guide curves.
A guide curve (whether manual or automatic) needs to run between corresponding vertices on all the loft profiles, and this is also a necessary condition for "Match Vertices" to work as it should.
ON EDIT: I have checked back to the original thread relating to the pictured loft and it seems I may have been wrong to assume it would be solved by providing the same number of sectors for both profiles. I will check the model when I get a moment and see if there's some other issue with it.
Yep, making the number of sectors equal didn't solve that issue. To be honest, I think it shouldn't matter as in some cases it would be rather tricky to fine tune the sketches like that. For example when one was to loft something that is a bit more complex. Just for an example an aircraft fuselage that evolves from a circle section to a narrow oval section via triangular section. In that triangular section there would be six different curves in one sketch. I know that doesn't sound like too complicated but it's just an example to show that things might get complicated. Now matching the circle to the complex section by slicing it up. Could it be simpler? Christians pointers should really fix what i'm rambling about...
Raino
I've tried making the same number of sectors on the start and finish profiles of the copy I took of your model, and it has actually "fixed" the problem, in the sense that the loft is now symmetrical, AND it conforms to all the information you have supplied it with.
The problem for you is that the inferred guide curve is now present on both sides, and it happens to be straight.
This is because the software cannot know what shape you want this guide curve to follow unless you tell it, by creating it explicitly. If you remove from the loft definition the guide curves you have provided (you can do this temporarily by deselecting "add guides"), you will see that the entire loft becomes straight, so this is the default condition.
Onshape is more restrictive of the ways you can specify your intentions than most other packages for this situation because, in its present beta phase, there is no way to tell it what the global direction of the tangency is at each profile. The guide curves evidently provide only a local indication of tangency.
Nor, as I first mentioned in your other thread, is there a way yet of specifying a "path" or "centreline" for the loft - this would have given the software a better chance of positioning the intermediate profiles, which would probably prevent the undesired inference you see here.
I have done the exercise of constructing the missing pair of guide curves with Raino's loft just to satisfy myself that it's possible, but I can't pretend it's straightforward.
Someone else can probably come up with a simpler workflow. My model is at
https://cad.onshape.com/documents/da23d67a50174f50a1786062/w/492e406ffc7c4562a84f35e9/e/0245eb45dcaf4a7f97c16684
The lack of 3D sketching makes it a bit laborious to provide guide curves, because the two loft profiles are different widths, so that a pair of angled 2D sketch planes has to be constructed, based on construction lines in one of the profile sketches, and a pair of "3 point " planes. Furthermore, to project one curve across to the other side is not straighforward: I used a surface extrude across to the midplane (so the projection would be normal to the source sketch) then "Use/Convert" to bring the curve across to the opposite 2D plane (normal to the latter)
Having modelled the 'left' side, it would be a simple matter of mirroring and using a boolean "Union" to combine the two halves into a single part
Christian, sorry for the thread hijack
Raino
It needs either something like "boundary" in Solidworks, which (when used to create a "surface") is like a loft sideways as well as longways, with control of tangency on all boundaries, or at the very least the ability in loft to add tangency conditions along the edge boundaries (outermost guide curves, in the case of a "surface" loft).