Welcome to the Onshape forum! Ask questions and join in the discussions about everything Onshape.
First time visiting? Here are some places to start:- Looking for a certain topic? Check out the categories filter or use Search (upper right).
- Need support? Ask a question to our Community Support category.
- Please submit support tickets for bugs but you can request improvements in the Product Feedback category.
- Be respectful, on topic and if you see a problem, Flag it.
If you would like to contact our Community Manager personally, feel free to send a private message or an email.
Render Studio: Appearances no property of Parts?
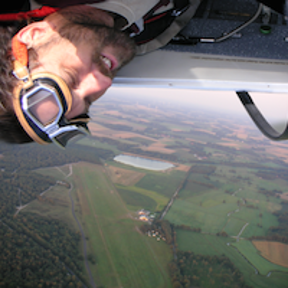
in General
I recently rendered an assembly that re-used parts and subassemblies I already rendered in another context. I was expecting these parts to already have their previously assigned appearance with them, but they didn't. Does that mean I have to reassign all the appearances each time I create a rendering of another combination of the same old parts? I feel that would be pretty un-onshapeish, wouldn't it?
If I have E.G. a door handle I use in many projects, I'd like it to bring in it's assigned appearance each time I add it to a new assembly and render. That'd be one of the key benefits of a render studio working on the very same data set as the CAD. Am I missing something?
0
Comments
One exception is that if you don't assign or otherwise edit the initial appearances in Render Studio, they remain derived from what you have in Onshape (which are determined by a combination of the material assigned, if from the Onshape material library, and the appearance of the part). Once you modify or assign a new appearance that one will override what comes from Onshape.
There’s also a related need for managing multiple color ways and color specifications for manufacturing. Ideally that would be connected to managing all the settings for rendering.
Simon Gatrall | Staff Mechanical Engineer | Carbon, Inc.
There are many different competing uses of appearances in CAD. I've definitely used color coding of surfaces to show areas which are post-machined, or to highlight revised areas of a model to toolers, or to show which areas of a part are core/cavity/slides/lifters, or which areas are textured/polished/painted/treated a certain way. That's more of a schematic use of color, not a representative use.
For rendering or certain types of product definition, you may want your virtual model to look as much like the real thing will as possible.
I get that having 27 "Textured plastic" Appearances is a lot to wade through and irrelevant to some users. However I'm often specifying the texture of parts/tools for injection molding. If these Appearances are indeed accurate, they are very useful. My experience with other rendering tools is that the scale of textures like this are often hard to get right.
There's probably a better way that Appearances could have been structured by Nvidia/Onshape. With plastics, I would ideally like to pick the general type of resin (which will impact translucency etc), the nominal color, and then select a texture from known vendors/standards (e.g. Moldtech, Yick Sang, and VDI EDM numbers). The same tool with different resins will yield different real world appearances despite the texture being part of the tool.
The textured plastic ones you're showing assume an opaque PC and/or ABS type plastic as far as I can tell. If you want clear PC or PMMA with a texture, you'll have to do some more work. PC and PMMA have clear or cloudy versions, but nothing with a texture. This isn't how product designers think about these issues.
Simon Gatrall | Staff Mechanical Engineer | Carbon, Inc.