Welcome to the Onshape forum! Ask questions and join in the discussions about everything Onshape.
First time visiting? Here are some places to start:- Looking for a certain topic? Check out the categories filter or use Search (upper right).
- Need support? Ask a question to our Community Support category.
- Please submit support tickets for bugs but you can request improvements in the Product Feedback category.
- Be respectful, on topic and if you see a problem, Flag it.
If you would like to contact our Community Manager personally, feel free to send a private message or an email.
Trying to emulate an organic shaped Harley Davidson rockerbox for 3d printing
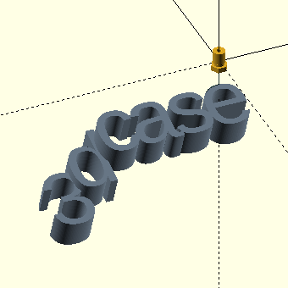
This is my attempt but I would like to get to a more rounded shape and I do not have the experience with onshape organic shapes to do it, I need help?
My attempt is a bit blocky but since it will be a 3d printed model of a real engine, I want it open on the top so you can see inside how it works. I have the whole engine already but this part keeps telling me it should be redone, I just don't know how!
Here is my whole assembly so far:
What I would like to achieve is something that is looking more like the real thing:
Any tips and advice would be appreciated. I do not own one of these, they are too expensive. I used photos from the internet to model the whole thing. If you search for Knucklehead Harley Davidson online you will find loads of photos.
Please suggest in simple steps how somebody experienced would do this? I will follow courses as well to achieve this, I already did the self paced courses to get to where I am now so totally self taught in onshape.
Thank you in advance,
Kees
Best Answers
-
martin_kopplow Member Posts: 852 PRO
Back in the days, the plugs for casting these parts have most probably been shaped by hand. You'll need to use surface modelling for this. There are comprehensive tutorials on the topic in the Onshape learning section. I'm afarid you'll have to work through at least some of them. It doesn't come much cheaper.
1 -
MDesign Member Posts: 1,018 ✭✭✭
The order you listed is a logical order based on how the software thinks, but sometimes is helps to start with something at the end to help you understand "why" you are doing the things prior to that ending. If a person has a background in surface modeling, they may not need that high level overview and just need to understand how the tools work. Good luck. Surface Modeling takes some patience for sure.
0
Answers
Back in the days, the plugs for casting these parts have most probably been shaped by hand. You'll need to use surface modelling for this. There are comprehensive tutorials on the topic in the Onshape learning section. I'm afarid you'll have to work through at least some of them. It doesn't come much cheaper.
Hi @martin_kopplow ,
Thank you for your time, and yes all these engine parts were originally made by creating a plug by hand out of wood, and then to make a mold from them. Cast either cast iron, for the cylinders and heads. or cast aluminum for these rocker boxes or engine covers.
I found the following three self paced courses, but they are not giving any indication as to what is the most logical order to do them in.
Understanding curves. I have partly completed this one a long time ago, will do it again from the beginning.
Introduction to surfacing. This sounds like the start of the surfacing material.
Onshape surface modeling. No clue as to whether this follows up on the intro or if it is something more advanced.
If you have others that I missed I would appreciate it you point me to them. Onshape is great but when it comes to these courses I truly think it could be improved with regards to the order in which they are best followed.
Thanks,
Kees
The order you listed is a logical order based on how the software thinks, but sometimes is helps to start with something at the end to help you understand "why" you are doing the things prior to that ending. If a person has a background in surface modeling, they may not need that high level overview and just need to understand how the tools work. Good luck. Surface Modeling takes some patience for sure.
Thanks @MDesign , Yes curves and projection of them is a frustrating business when attempted without learning first. I am sure surfaces are even worse. But, like all these things, we learn when you need to and after that it is something wonderful 😀
Xmas is coming, I will have time to spend on this.
Regards,
Kees