Welcome to the Onshape forum! Ask questions and join in the discussions about everything Onshape.
First time visiting? Here are some places to start:- Looking for a certain topic? Check out the categories filter or use Search (upper right).
- Need support? Ask a question to our Community Support category.
- Please submit support tickets for bugs but you can request improvements in the Product Feedback category.
- Be respectful, on topic and if you see a problem, Flag it.
If you would like to contact our Community Manager personally, feel free to send a private message or an email.
"carve" into a part to maximize fit into specific shape, but still able move it out of an opening?
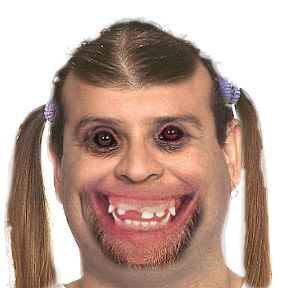
I'm trying to come up with a way to create a part, that would fit into a container occupying maximum volume of the container, yet still be able to move out the container through an opening.
Any tips how to achieve this?
Thank you!
https://cad.onshape.com/documents/958ca436797856d24fe4c985/w/c5d737c3218768a6adbb8440/e/4b5565200a0c0ca7c775af1c?renderMode=0&tangentEdgeStyle=1&uiState=67ed3c3ada0c993a41231396
0
Answers
trial and error 😜
You can place your parts into an assembly, then constrain a portion of your moving part to a spline path by using a tangent mate. Just make a general spline path on a sketch of the direction you think the part will take. Then, if you constrained it "right" you will be able to rotate (freehand) your part while moving it along that path. If you do this while viewing the assembly in section view, you should be able to detect any interference.
If you are making these parts all the time, you can make a custom feature that moves the parts along a path and checks for interference then returns the best path if one is available. This would take some dev work, so I only recommend it if you plan on saving lots of money with it.
Learn more about the Gospel of Christ ( Here )
CADSharp - We make custom features and integrated Onshape apps! Learn How to FeatureScript Here 🔴
If only Onshape had "collision" detection in assembly. The rough estimate of the design I've already done via physical carboard cutout, I was hoping to get more precise results
It does. if you cut a section you'll see red where parts interfere.
Sounds like a calculus problem...
Reminds me of the Moving Sofa Problem which has been famously hard to solve.
The Onsherpa | Reach peak Onshape productivity
www.theonsherpa.com
@EvanReese: "Pivot! Pivot! Pivot!"
You could draw a curve, then create a linear curve pattern with your part with a relatively small distance/high instance count and have all those parts merge to themselves. this way you get a basic solid space claim for the path. perhaps you could even smooth that path out afterwards with the new 'constrained surface' and offset that slighly afterwards for a little play…
oh sorry, wrong way around: I thought you had a part and wanted to move it in, but you want to have a container and create a part with it…
It's about impossible.
Make a cross section in your assembly, go to a side view, and move/tilt one part around as if you are doing it in real life. That will get you 80-90% of the way there. Make adjustments to the design to get it as close as you can.
Then print it out and test in real life. Something will always be missed in CAD that will only show up in real life. You can print just a narrow portion of the design to save time/material. Should be good enough to get your answer before printing the whole thing.