Welcome to the Onshape forum! Ask questions and join in the discussions about everything Onshape.
First time visiting? Here are some places to start:- Looking for a certain topic? Check out the categories filter or use Search (upper right).
- Need support? Ask a question to our Community Support category.
- Please submit support tickets for bugs but you can request improvements in the Product Feedback category.
- Be respectful, on topic and if you see a problem, Flag it.
If you would like to contact our Community Manager personally, feel free to send a private message or an email.
Mating a part to multiple other components
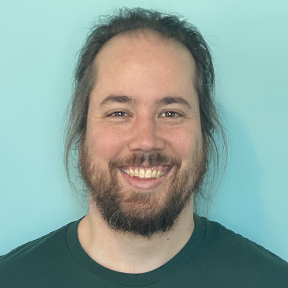
Hi all, I'm a newer user, loving Onshape so far!
I've built out some fairly complex aluminum extrusion frames using the frame tool, and now I'm trying to mate custom brackets to bolt together frame components, as shown below. In Solidworks I would simply center the vertical midplane of the part to the vertical frame member's midplane in one mate, and the slanted midplane of the part to the midplane of the slanted part in a second mate, then flush to the shared sides of both frame members in a third mate, done. However, with mate connectors (MC) I'm overwhelmed. I've tried sliding mates but it feels clunky to have to create custom MCs just to put the Z axis in the direction of sliding (rather than picking a direction vertex like in other operations in OnShape). I'm at a bit of a loss on how to do this elegantly and robustly such that the bracket will keep it's holes centered on both members, even if I were to shift the slanted frame member up or down against the vertical one.
In fact, even forgetting about making the design robust against future adjustments, I'm still not even sure how to fix the dang thing in place at all, other than meticulously measuring current dimensions and manually offsetting some arbitrary starting point with two implicit MCs. For me at that point the value of showing the bracket in my design at all isn't really worthwhile since I've separately configured the part properly for each unique joint, gathered qty's needed, and can now go laser cut the brackets knowing they will indeed fit the final frame. Still, part of me wants my CAD to truly represent what I've built...
Is there a better way, or have users gotten over the tedium of this process as the other benefits of Onshape make it more than worthwhile?
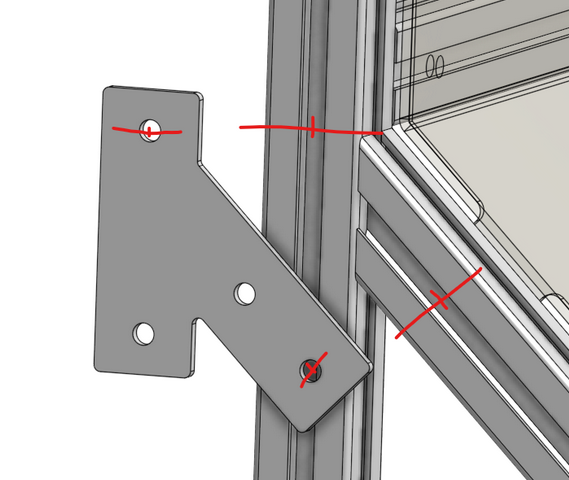
0
Best Answer
-
eric_pesty Member Posts: 2,299 PRO
I have found working with these channels requires getting comfortable with modifying (offsets and re-align) the mate connectors created by the mates (i.e. after creating the mate, video at bottom for more details).
If you used the frame tool, you might be able to add an explicit connector to one of the frame parts (assuming you have a logical sketch reference you can use that might make things easier if you had a matching one in your bracket (like the intersection of the 2 centerlines).
Otherwise the best reference to use with these channels is the round hole in the middle (that way the "manual" offsets are 1/2 the width of your channel, which isn't a "random" number) and this might be a reasonable time to use two mates to locate the part: a slider on the vertical one and something like a planar relation to constrain to your angled part.
You can do it directly from the assembly (as shown below by editing the mate connectors in the mate) but it does make your life easier if you add a couple reference MCs in your connecting plate... I used the holes which requires both re-aligning and offsetting but you could use the "end faces" as well to eliminate most of the "re-aligning" but it's a bit less robust (eg. if you add a fillet on one corner but not the other things will go out of alignment).
Example doc:
https://cad.onshape.com/documents/7dde71c7350454606a95cb3e/w/6bc23be9bf2088505e317eeb/e/86cda3c90b9bb6001ca77122?renderMode=0&uiState=64d6ba36ad2b1030a1c1b289
See also "Assembly 1" and part 4151 for examples of how adding MCs to the brackets really helps streamline the process...
Video on editing mate connectors:https://www.youtube.com/watch?v=HUVFq7tixKM&t=2s
2
Answers
If you used the frame tool, you might be able to add an explicit connector to one of the frame parts (assuming you have a logical sketch reference you can use that might make things easier if you had a matching one in your bracket (like the intersection of the 2 centerlines).
Otherwise the best reference to use with these channels is the round hole in the middle (that way the "manual" offsets are 1/2 the width of your channel, which isn't a "random" number) and this might be a reasonable time to use two mates to locate the part: a slider on the vertical one and something like a planar relation to constrain to your angled part.
You can do it directly from the assembly (as shown below by editing the mate connectors in the mate) but it does make your life easier if you add a couple reference MCs in your connecting plate... I used the holes which requires both re-aligning and offsetting but you could use the "end faces" as well to eliminate most of the "re-aligning" but it's a bit less robust (eg. if you add a fillet on one corner but not the other things will go out of alignment).
Example doc:
https://cad.onshape.com/documents/7dde71c7350454606a95cb3e/w/6bc23be9bf2088505e317eeb/e/86cda3c90b9bb6001ca77122?renderMode=0&uiState=64d6ba36ad2b1030a1c1b289
See also "Assembly 1" and part 4151 for examples of how adding MCs to the brackets really helps streamline the process...
Video on editing mate connectors:
Your workflow description suggests that the mating challenges you are dealing with may be a consequence of your overall approach. OS gives you the opportunity to create a complex frame with far fewer mates than would be needed in SW, but this outcome depends heavily on appropriate use of multipart modeling and other OS features. Here are some key aspects of our approach.
We fabricate frames by cutting extrusions to length and striving to use a minimum number of joining plates. We make extensive use of 8020's "end fasteners" and counterbored joints for right-angle corners. We model flat joining plates in OS and cut them on a CNC router. Even when we are using commercially available plates, it's helpful to create the plates within the model rather than import them.
Our modeling approach is based on the principle that all parts should be created in the exact position that they will occupy in the final assembly. We begin with a master parts studio that defines the geometry of the frame with layout sketches on the three native planes. Rather than using the Frame tool, we incorporate simple representations of the extrusion profiles (e.g a 1x2 in rectangle for the common 1020 extrusion profile) in construction geometry and create the extrusion parts using the custom feature "Extrude 8020Inc Profile" and the "up to vertex" option in the extrusion dialog. Parts that meet at an angle other than 90 degrees can be created by extruding "up to face" of an exsting part or by splitting a part with the face of an adjoining part.. Once all of the extrusion parts are created, we model the joining plates and counterbore hole locations with sketches on the approriate extrusion faces. Defining all of the model geometry in sketch dimensions facilitates future revisions.
For very complex frames, it may be necessary to model parts in additional parts studios. The layout sketches in the master studio can be derived into these tabs to keep the model's origin consistent
Most of our frames include multiples of individual parts. Our preferred approach is to model only a single instance of each part in the parts studio, and to insert additional instances in the assembly. Doing so yields a bill of materials with accurate part counts and no redundant duplicates. However, the addtional instances must be mated individually. I can't offer a foolproof way to simplify this process, but I would encourage you to keep experimenting to find methods that work for you. Begin by fixing (only) one part and use the group mate wherever possible. We lean heavily towards using only fastened mates with implicit mate connectors on the faces and edges of extrusion parts. As @eric_pesty noted, strive to use offsets that can be easily measured from the innate geometry of the hardware. Often, the simplest mating arrangement may involve fastening non-adjacent parts with an appropriate offset based on the overall model geometry.
Here is a simple example from our 2023 robot that illustrates our approach; Team 293 Frame Example. The assembly illustrates a variety of mating approaches, but there are many ways to skin this cat!
https://cad.onshape.com/documents/00c287c349a9fd9685831061/w/60ac01dcd44d0da641eb114e/e/c0f77d7dc58d9547a35fa6a3