Welcome to the Onshape forum! Ask questions and join in the discussions about everything Onshape.
First time visiting? Here are some places to start:- Looking for a certain topic? Check out the categories filter or use Search (upper right).
- Need support? Ask a question to our Community Support category.
- Please submit support tickets for bugs but you can request improvements in the Product Feedback category.
- Be respectful, on topic and if you see a problem, Flag it.
If you would like to contact our Community Manager personally, feel free to send a private message or an email.
Options
Is there a way to sweep an object through space while performing a boolean?

I'm having fun trying to design a scroll pump and realize that the easiest way to do this would be to design one half of the scroll pump, i.e. a thickened spiral, and then to constrain that spiral to the desired mechanical movement in an assembly and *then* to use that movement to carve out the material from the other side.
From what I've learned so far, it looks like the general optimal shape for a scroll pump of infinitely thin walls might be (is?) an involute spiral, but the wall thickness forces a deviation from the optimal math, and furthermore the part near the center output port is not described by an involute.
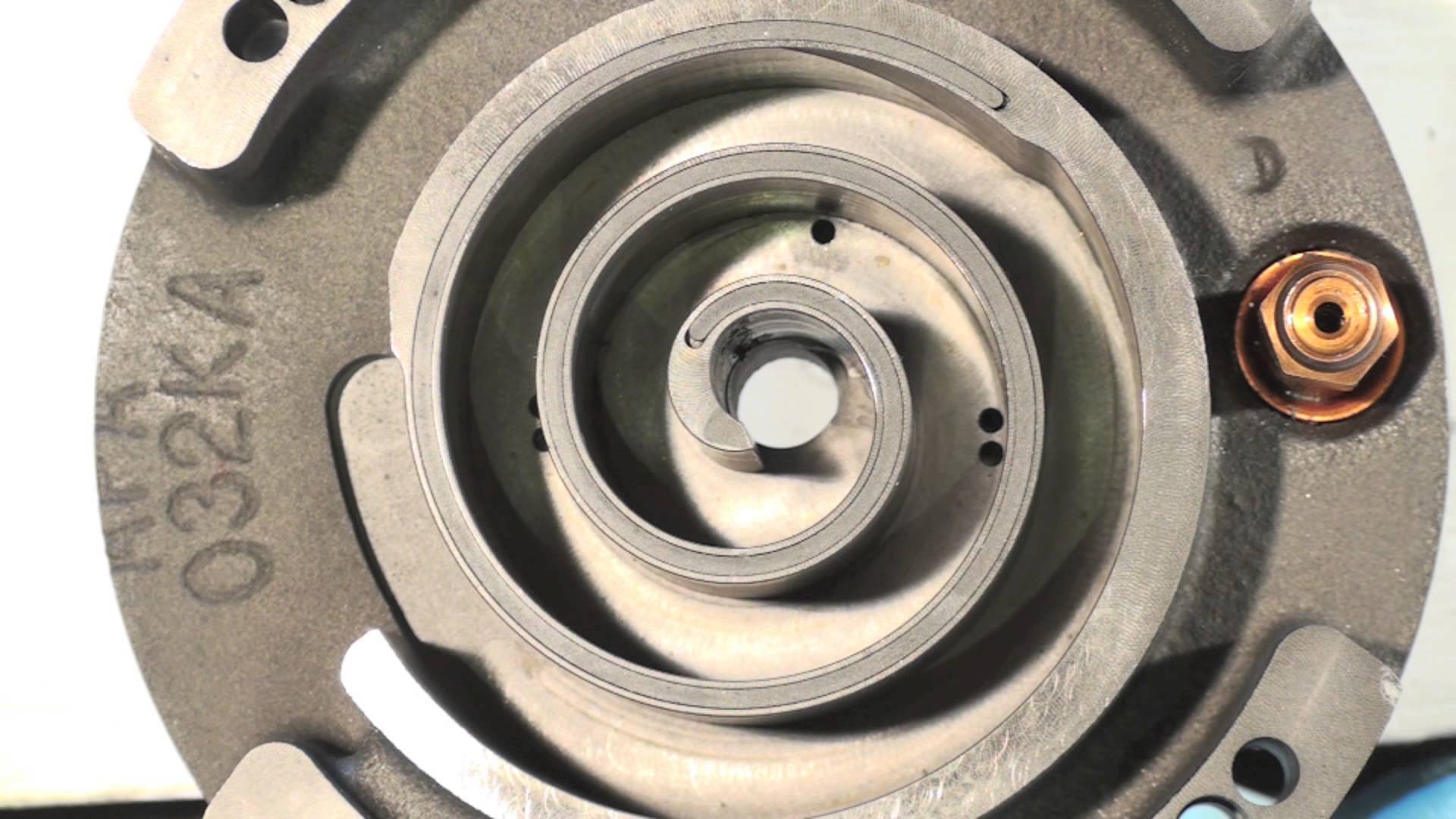
So I figure it's worth doing a numerically optimal way.
Is there a straightforward way to do this with OnShape? (That is to say: create a solid, define a motion for that solid, and then cut anything contacting the moving solid so that the space swept by the solid is clear.)
The best I can think of so far is to manually do this as an assembly in context, but that seems extremely high effort for a relatively low resolution. I'm hoping there's a better way.
(For reference, here's a video of a scroll compressor. Imagine the moving scroll carving out from the fixed scroll side, almost like a broach.)
From what I've learned so far, it looks like the general optimal shape for a scroll pump of infinitely thin walls might be (is?) an involute spiral, but the wall thickness forces a deviation from the optimal math, and furthermore the part near the center output port is not described by an involute.
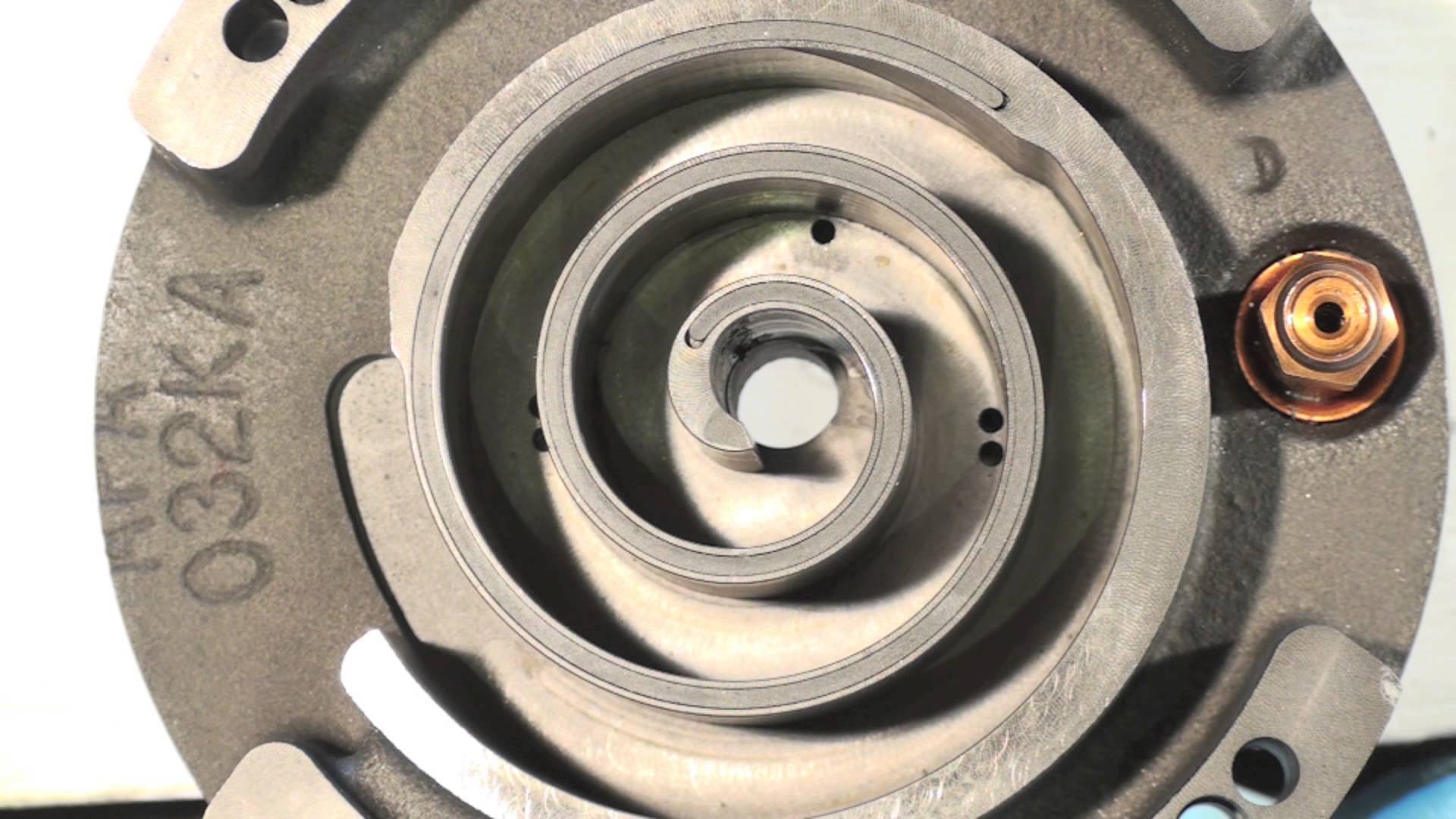
So I figure it's worth doing a numerically optimal way.
Is there a straightforward way to do this with OnShape? (That is to say: create a solid, define a motion for that solid, and then cut anything contacting the moving solid so that the space swept by the solid is clear.)
The best I can think of so far is to manually do this as an assembly in context, but that seems extremely high effort for a relatively low resolution. I'm hoping there's a better way.
(For reference, here's a video of a scroll compressor. Imagine the moving scroll carving out from the fixed scroll side, almost like a broach.)
Tagged:
0
Comments
https://cad.onshape.com/documents/bf5f060b6be9c098a230cbbe/w/7f02616f857ca4006b486dc1/e/63dcf4e30813e9dfe759f711
However, let me point out that this is not an XY question: I am not looking for a solution to the specific scroll pump problem, but instead for a general solution of how to move a tool through space and perform a boolean with all places the tool contacts. This is broadly useful for resolving collisions between moving parts. It would solve the above problem as well as many more I can imagine.
P.S. Wow, looking at your feature scripts. Thanks so much for taking the time to get involved in this question, your page is awesome! I can definitely see how I could use your path pattern tool to come really close to accomplishing the goal, the only challenge that remains is to have a smooth CAD surface instead of the discretized visual surface described by the instances.