Welcome to the Onshape forum! Ask questions and join in the discussions about everything Onshape.
First time visiting? Here are some places to start:- Looking for a certain topic? Check out the categories filter or use Search (upper right).
- Need support? Ask a question to our Community Support category.
- Please submit support tickets for bugs but you can request improvements in the Product Feedback category.
- Be respectful, on topic and if you see a problem, Flag it.
If you would like to contact our Community Manager personally, feel free to send a private message or an email.
Best Of
Re: Extruding a taper.
slight change to my suggestion. create a cylinder and use a wrap surface for the base profile surface feature then loft to a point. I also had to make a small boolean subtract in the center to avoid non manifold error, but it doesn't matter if you change the instance count. the boolean doesn't know how to pickup the additional instances. Would be helpful if the circular pattern could merge with existing parts/geometry. If you finish the part with high instance count and include all the parts you can get it to a single part with many instance variations with just a warning of missing selections.
Was playing with variables. I left the sketch on in the animation to demonstrate what is driving the shape.
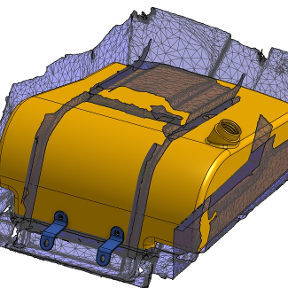
Re: Extruding a taper.
Loft one segment from a sketch to a point. Mirror that part. Then circular pattern.. to get it to work perfectly to you will have to do some math or setup some variables and use formulas.
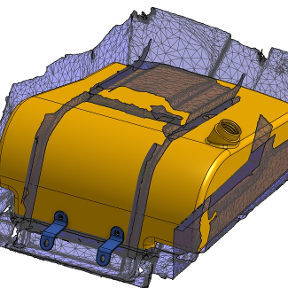
Re: Does anyone know how to do this?
Oliver's right. If it's something that my Shapes feature can already handle, then roll with that for convenience. You may want to pair it with my Selection Fillet feature so that you can change the number of waves and not have to manually select new edges if they are created. Here's an example. If you need a different profile, I'd sketch just one pie wedge of the pattern and make the wedge's angle = 365*degree/#number
, then you can make a circular pattern of that either in the sketch or as a circular pattern feature.
Re: How can I query the faces that highlight when I pick a feature?
You could use lastModifyingOperationId(context, query), against every face. It wouldn't be super efficient, but would work.
How can I query the faces that highlight when I pick a feature?
qCreatedyBy() works for things like Extrude and Revolve because those are creating geometry. It doesn't work for things like Move Face and External Thread because those only modify existing geometry. However if I click on a Move Face or External Thread feature in a Part Studio it highlights the relevant faces. Is there a way to query those highlighted faces?
Is there an option to 'Return to the Previous View' (eg, after rotating the view)
Re: Improvements to Onshape - December 13th, 2024
Thank you Onshape team for a great year of updates. I am looking forward to see what you bring to the table in 2025. Happy Holidays everyone.
Re: Improvements to Onshape - December 13th, 2024
Great updates. I was waiting for the curve approximation tools
Re: Improvements to Onshape - December 13th, 2024
Brilliant! That's made my day!