Welcome to the Onshape forum! Ask questions and join in the discussions about everything Onshape.
First time visiting? Here are some places to start:- Looking for a certain topic? Check out the categories filter or use Search (upper right).
- Need support? Ask a question to our Community Support category.
- Please submit support tickets for bugs but you can request improvements in the Product Feedback category.
- Be respectful, on topic and if you see a problem, Flag it.
If you would like to contact our Community Manager personally, feel free to send a private message or an email.
Best Of
Re: Is there a usage standard for CALLOUTS that have boundary geometry?
2017 is the latest version of ASME Y14.100. I have the 2013 version, and the flag note section doesn't say much.
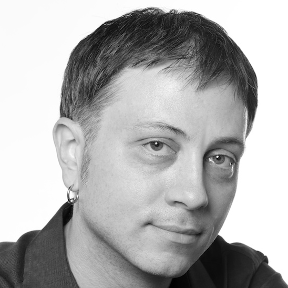
Re: Is there a usage standard for CALLOUTS that have boundary geometry?
I dug through some files that came home with me from work when I retired. Found a PDF of ASME Y14.100-2004 (which even after 20 years appears to be the most current revision). I referenced parts of it when creating/unifying a set of starter drawing templates for the company I worked for, which needed to be optimized to work in the CAD system currently being used.
It appears that OS did a broad survey of drawings in the wild to determine all the possible symbols that might be used with flag notes and callouts and included them in OS. In reality there is no officially industry standard with respect to flag/callout symbol usage.
I have to say Y14.100 is a classic example of designing a horse by committee; you get a camel.
Industry conventions and company drawing practices appear to be all over the map. At best ASME Y14.x documents contain a mish mash of information that a company might consider when documenting their internal drawing practices.

Re: Configurable text item (Sticker or Padprint)
Text is configurable. You might need to clarify, or share your document.
Re: AI tool to enhance your renders: magnific.ai (maybe helps improve render studio results?)
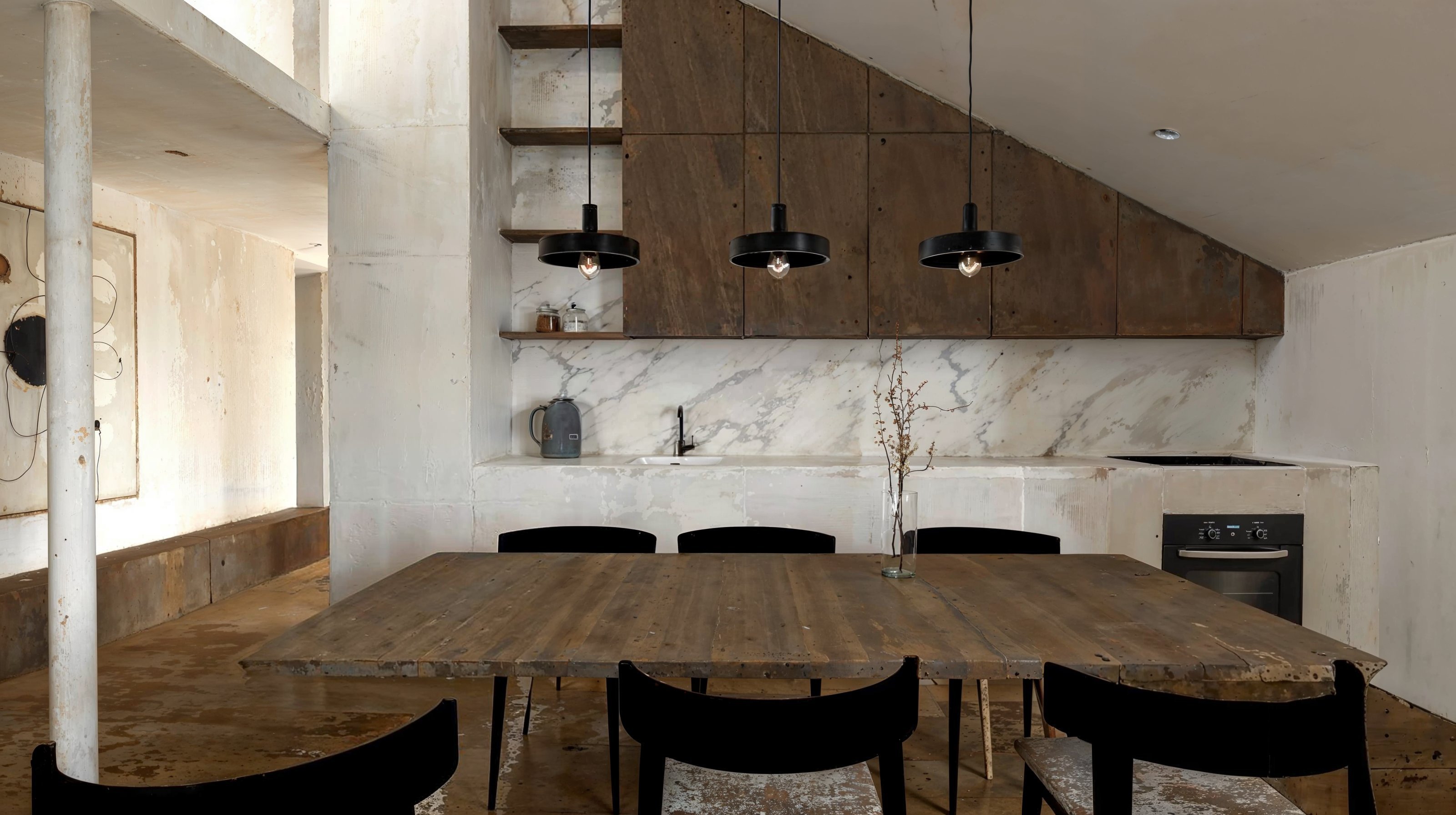
Here it is "optimized for" set to "3d render":
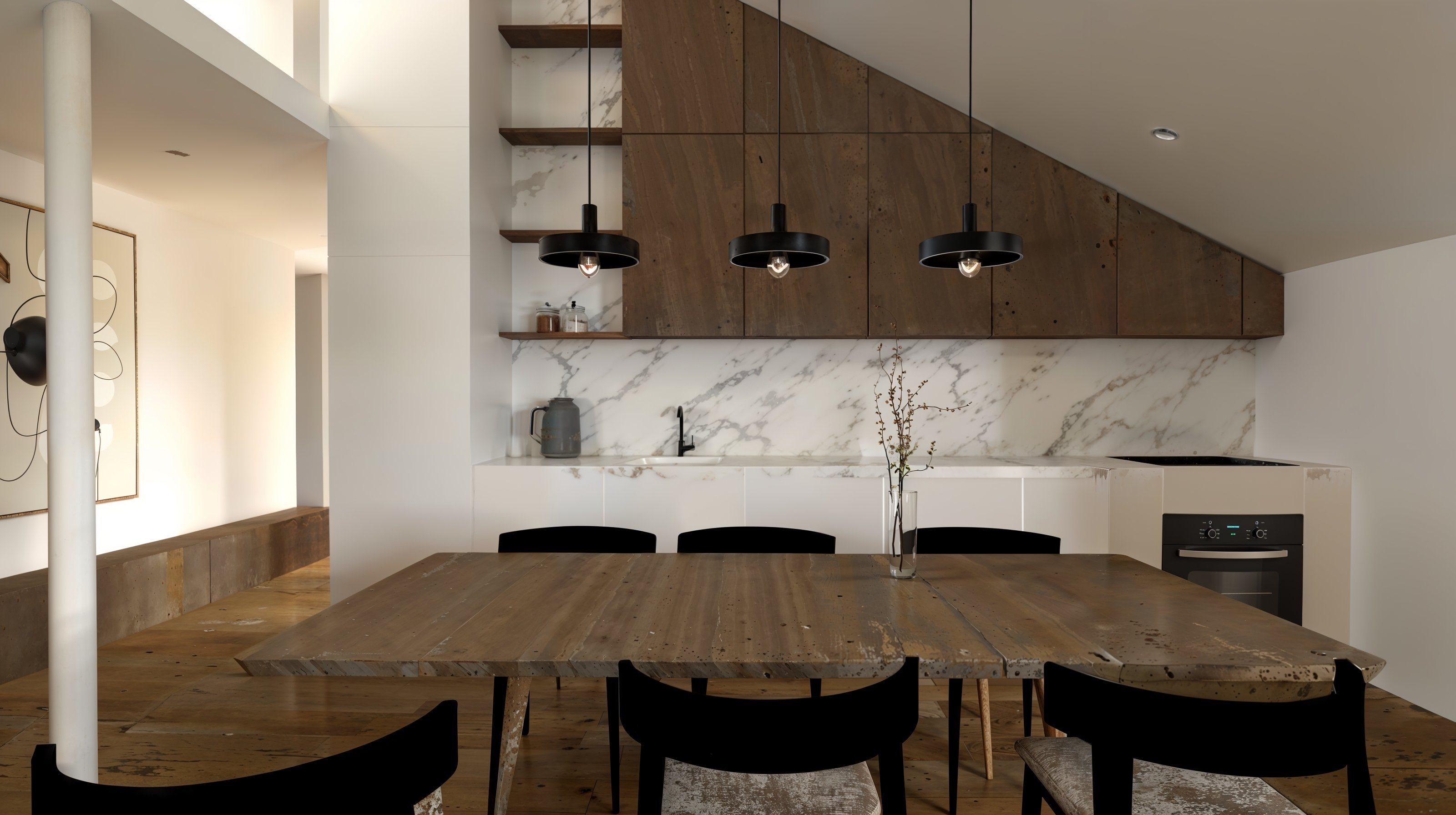
@Ste_Wilson it's pretty subtle! Here is a close up of one area:
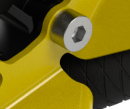
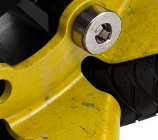
@Rhett_Robinson yes - it has the following modes:
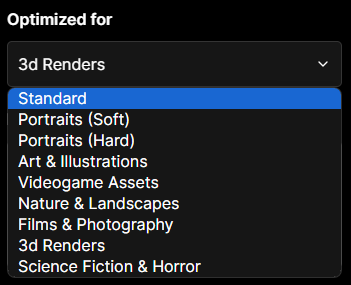
@MichaelPascoe here it is! "standard" optimization mode:
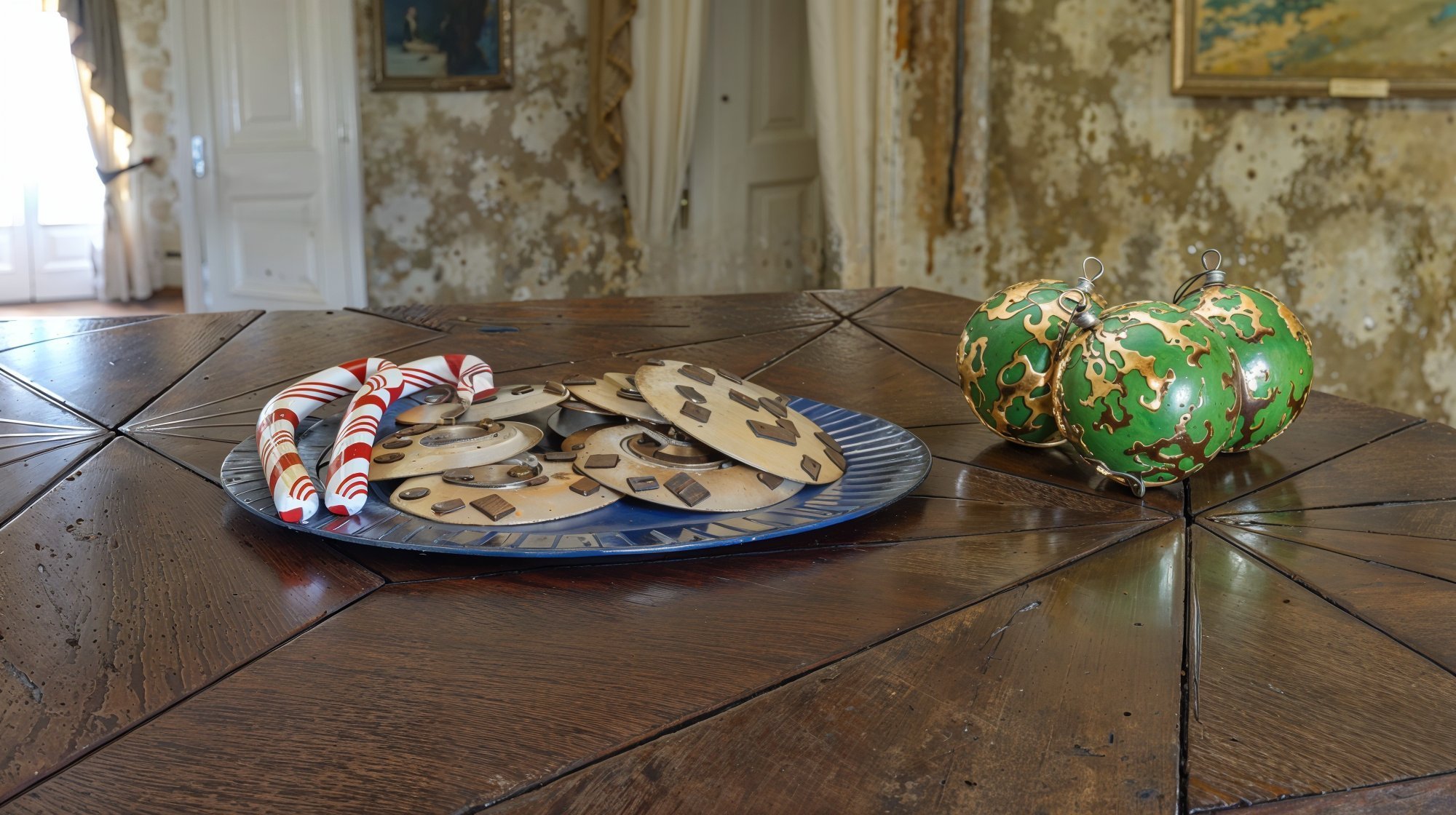
"3d render" optimization mode:
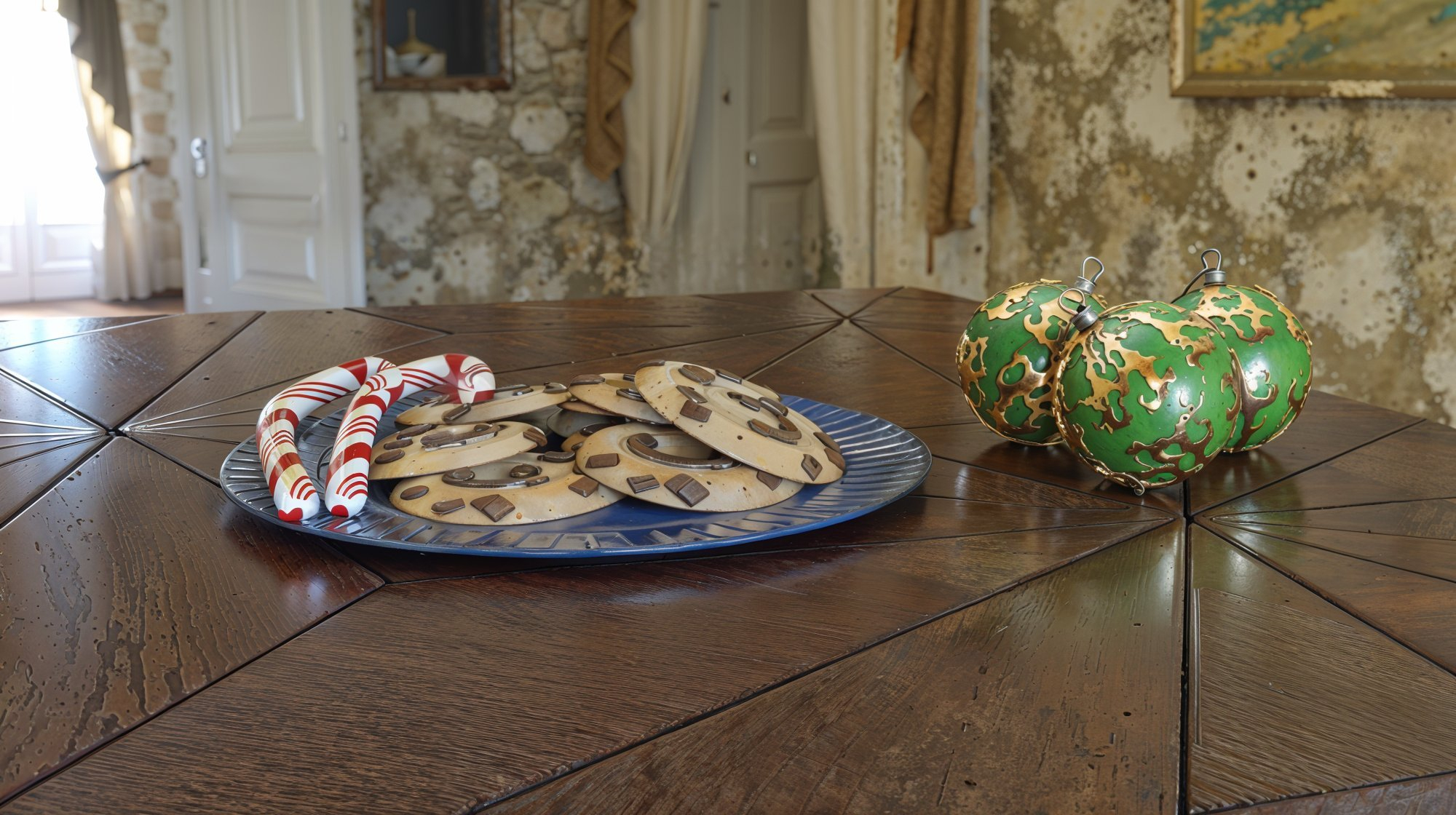
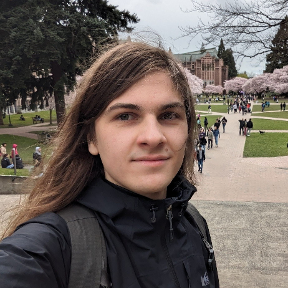
AI tool to enhance your renders: magnific.ai (maybe helps improve render studio results?)
In short, it's an upscaling + detail adding tool that uses generative AI to improve images: hand drawn, photos, renders, etc...
Of course, I'm most interested in the render part, to see how can things I make be made to look more photorealistic (or just cooler.)
Here are some samples of inputs and outputs, prompt is at the end of this post.
Since they don't have a free trial, let me know if you have any images you'd like me to run through it. Post your render here, and I'll post back with the generated result.
I just ask that you limit them to no more than about 1000x1000 pixels, since the cost scales a lot with image size.
Onshape render of mecanum wheel:
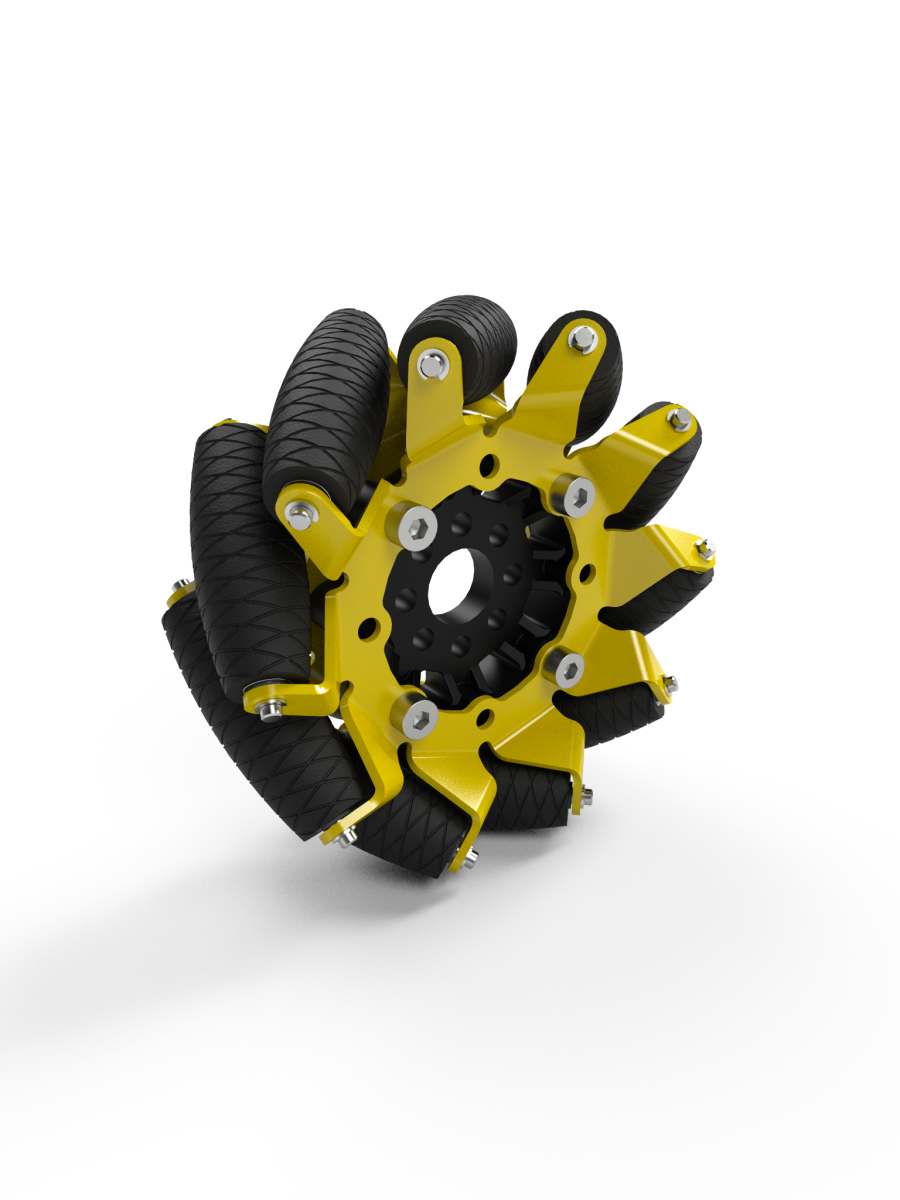
AI output:
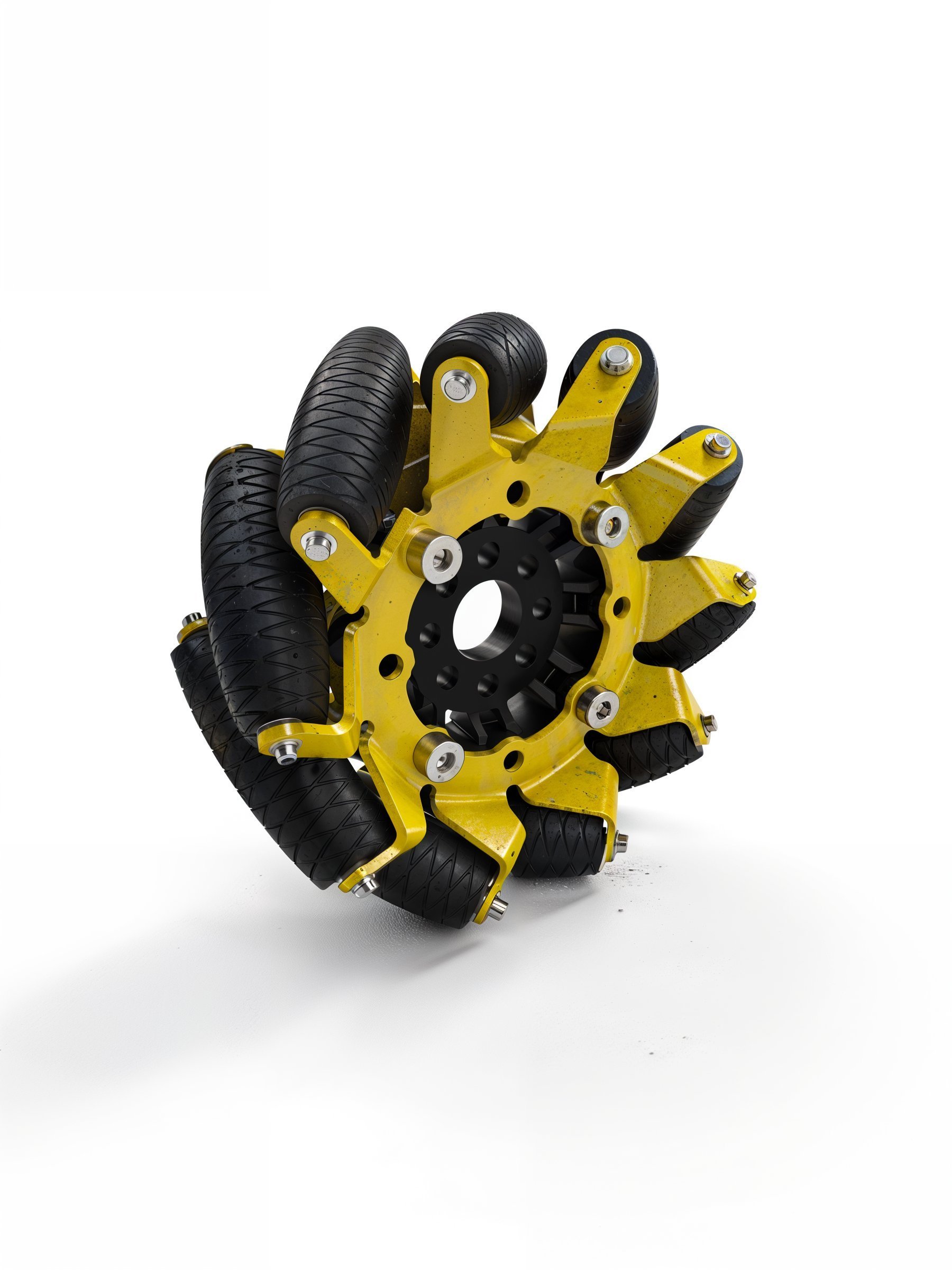
Render of underwater robot (done in Blender since Render Studio kept crashing):
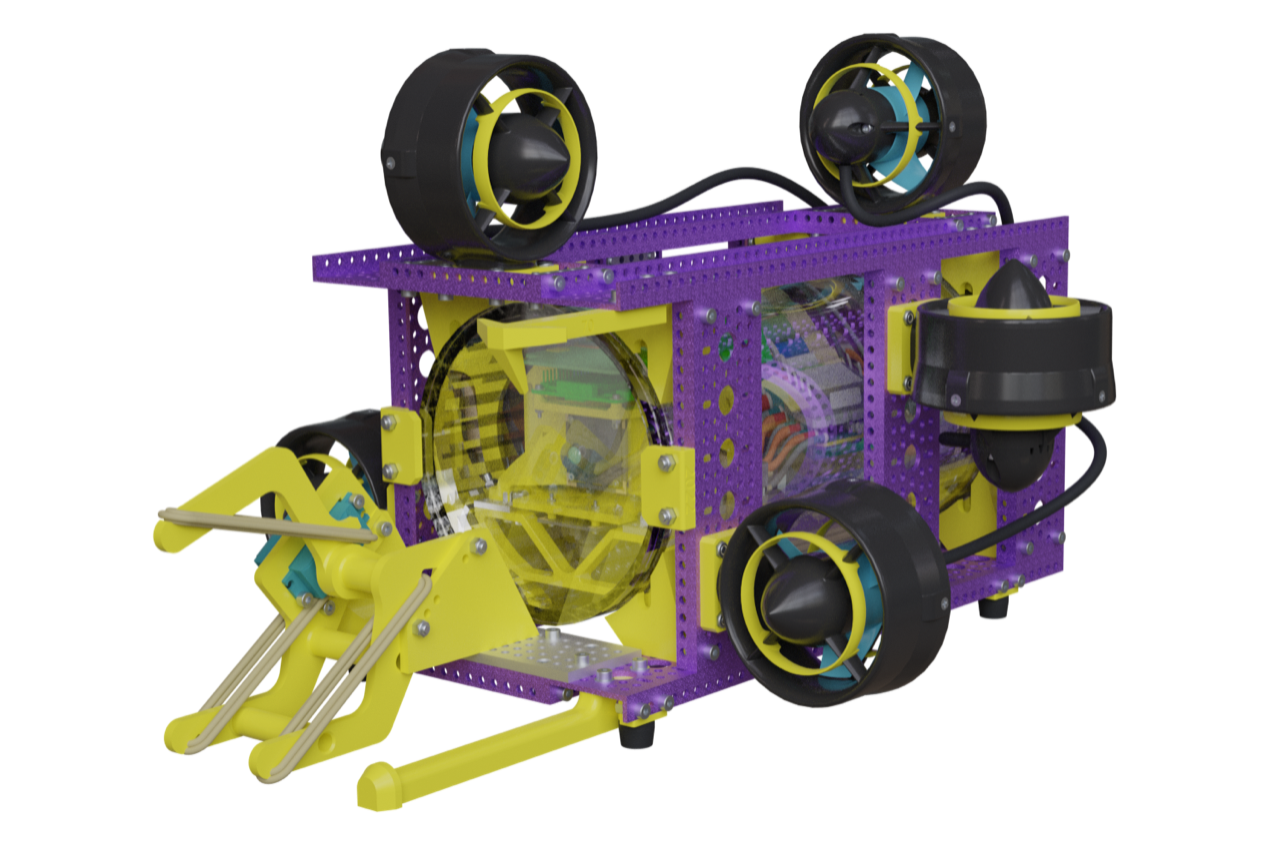
AI output:
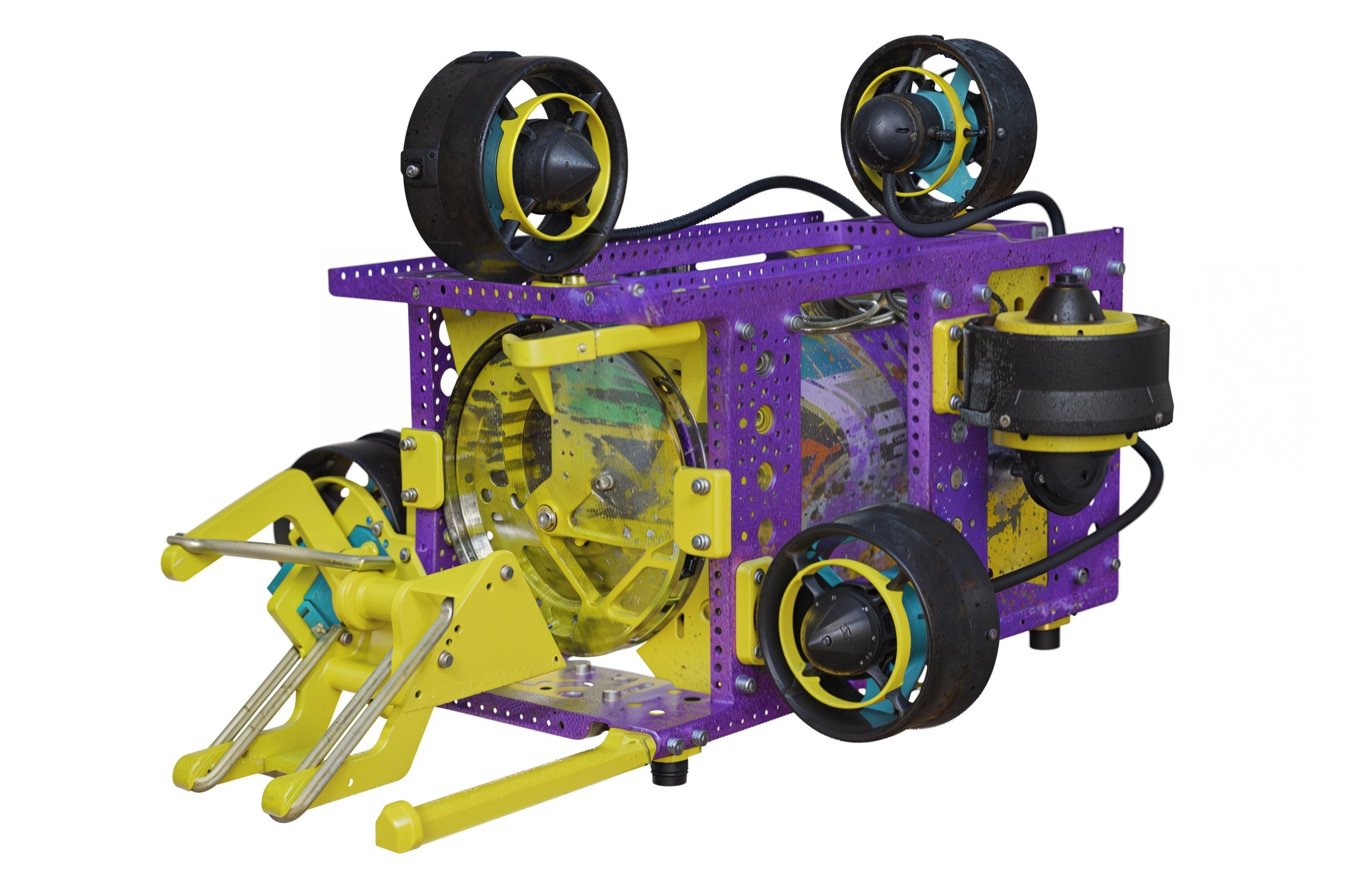
The prompt/setup (same for both images):
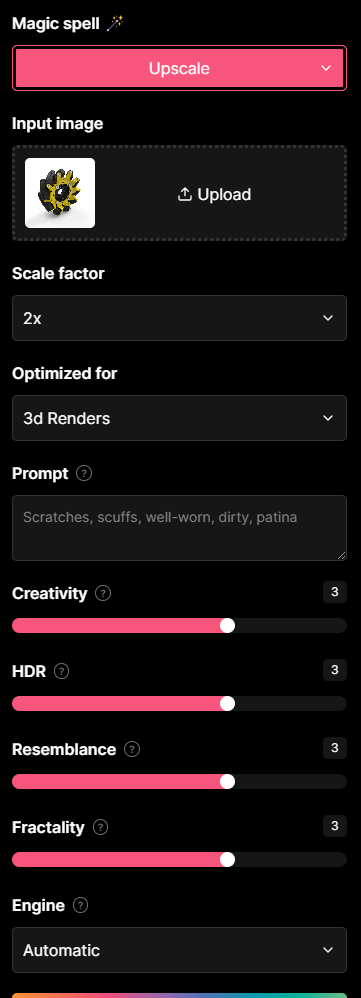
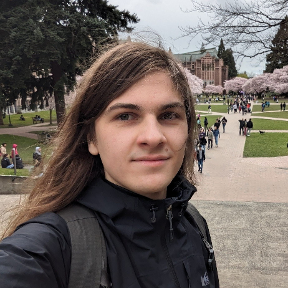
Re: Why is inserting a view of a configured assembly instance into a drawing not possible?
Creating a "phantom" assembly (Move to new subassembly) of the configured assembly instance works around the inability to create a drawing view directly of a configured assembly instance. It certainly is a lot easier than creating a view of the parent assembly and hiding all the parts except those that make up the configured assembly instance.
I was able to create the drawing that describes how to derive the hinge from off-the-shelf hardware.
However, this method does come with some complications:
o The parent assembly structure gets an additional layer that doesn't make sense. An assembly instance that contains just one instance of an assembly.
o Any additional constraints that were added in the parent assembly to further restrict motion within the parent assembly, along with named positions are not copied into the subassembly.
o You have to switch to the "phantom" assembly to change the configuration of the configured assembly instance.
The above issues would be non-issues if OS had better part selection methods for hiding parts in a drawing view, or allowed selection of configured assembly instances when creating drawing views.
.

Re: Configurable text item (Sticker or Padprint)
There are a couple ways I can think of. You didnt specify if a composite part would do the job, but that's what I would recommend. Now: how to make different numbers of bodies all work in the same composite!
The first is to use this custom feature:
https://cad.onshape.com/documents/e2f3157a9eba6b34464401f1/v/5bbb442dbb8634fcef9693c7/e/0f7cc7c368165593e24abb3e
Take a look at "the cool way" and "the cool assembly" (save the uncool way for later).
What that feature does is create a closed composite from the bodies resulting from one or more other features (like your extrudes). So in your example, I create two extrude operations. One extrudes the word "Invariant" and the other extrudes "AAA" "BB" or "C" from the configured text. These features, then are supplied as inputs to the custom feature and it gathers up all the bodies up in to a single composite part "Composite part 1". Try it out. The number of bodies may change but the resulting composite does not. You can see in the assembly that the assembly is configured, and that the different assembly configurations reference the different configurations of the part studio. Easy peasy, keep it sleazy.
The second way is to grab my custom feature called "text".
Grab the latest version, and take a look at the examples in the doc that contains the custom feature. When the time comes to create solids, select "create composite". The feature parameters are all configurable, so you can configure the text to be whatever you want. The result will always be a single closed composite.
I think chaining the results of one operation to the input of another is a pretty great UI pattern that I would like to see more often in the standard library. Until then we just write our own.
NOTE: Just for fun, I tried to do this "the uncool way", which is:
create configured sketch,
3 different composite operations corresponding to each of the resulting body sets.
configure the part studio and configure the suppression of the composites.
Then, in the "uncool assembly", repeat the process. Insert the 3 different configs, then configure their suppression. I tried switching between them but it doesn't work. The composite body in the uncool way gets 3 different ids, so each time you switch configs in the assembly the instance reference gets broken.
Do it the cool way.

Re: How to replicate sketch/extrusion across faces of extrusions from circular pattern?
Use an actual circular pattern feature (instead of drawing each pin)!
Re: Printable Onshape Keyboard/Mouse Shortcuts Quick Reference Card
Updated reference card to reflect the 3D Viewing (rotation) behavior change using the cursor keys in the latest update (1.191, 2024-12-13).
Here is the downloadable PDF…
