Welcome to the Onshape forum! Ask questions and join in the discussions about everything Onshape.
First time visiting? Here are some places to start:- Looking for a certain topic? Check out the categories filter or use Search (upper right).
- Need support? Ask a question to our Community Support category.
- Please submit support tickets for bugs but you can request improvements in the Product Feedback category.
- Be respectful, on topic and if you see a problem, Flag it.
If you would like to contact our Community Manager personally, feel free to send a private message or an email.
Best ways of modeling surface area details?
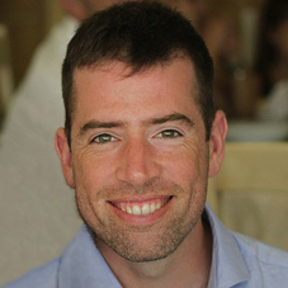
In mechanical design there are a bunch of important details that need to be captured in the design and then communicated to fabricators can't easily be modeled with geometry. Most often they are a specific part of a surface.
Examples include:
Examples include:
- Varying surface finish or tolerances on different parts of a surface with a constant nominal dimension (a shaft for instance)
- Masking, painting, adhesive, and other applications to specific portions of a surface.
- Threads, knurls, roughing grooves, on surfaces where adding the actual geometry takes too much time or compute resources.
- Aesthetic tool mark patterns.
Tagged:
2
Comments
Until such time as these (and many other) extrinsic designations of part characteristics are standardised, not just across CAD packages but across the international engineering community, it's not going to be feasible to base contractual commitments on 3D models.
@pete_yodis Onshape does not yet have any way to capture information about surfaces in the model. I hope they add this capability eventually. I was hoping for info on how people do this in other CAD packages or what they would like to see in Onshape.
I'm really thinking about information capture. How do I keep track of the fact that part of a surface needs to be treated differently. How can someone else opening up the design understand that.
Regarding 2D vs 3D, I think it's a silly argument. One uses the form of communication that is most effective and efficient for the situation.
However there is a subset of the opposite side of the argument who wish to deny all users the option of 2D representations, presumably on the basis that if they cannot access them, they will be forced to find some way to force 3D representations to act as an acceptable substitute.
Which, for some requirements, would be not just silly but impracticable.
The bar 3D has to meet, before it can "go solo", is set remarkably high: communicating unambiguously, as well as effectively and efficiently, and into the indefinite future, in all aspects of all fields of endeavour, in all locations and operating environments of the world where stuff is built, appraised, inspected, maintained, and litigated about.
Exploring just one of these points: items with long lifetimes are a particular case in point. Who can still read 3D models produced by mainframe systems, like Prime, or even the workstations which followed them, like Ideas? The most obvious situation where this matters, but by no means the only one, or even the most important one: Large expensive engineering installations (say, an ultra-high tonnage press or ultra-heavy lift crane) have long payback and very long service lives, sometimes a great many decades.
Moreover, certain inherently dangerous technologies (not just the obvious nuclear plants, but things like highly pre-stressed concrete structures on a sufficiently grand scale) can be tricky to decommission safely, and this might have to happen a long time into the future.
The most durable means of accurate communication ever devised were pottery tablets, stamped with wedge shapes and then fired. They are still, in many cases, virtually unaffected by the passage of many thousands of years since they were 'written', and it's paradoxical that the most fleeting communication technologies, in general terms, are the most recent ones.
And it seems to me that to suggest CAD companies can drive the eradication of 2D is a bit like suggesting a technology provider bloc, such as machine tool builders, could have driven the US to abandon inch/pound measurement in the 1950s.
Perhaps I phrased my original post poorly. I'm asking about good ways to capture the information for the designers so that design information is centralized. I'm not implying that the subsequent communication to fabricators should be 2D or 3D.
Currently in SW I capture surface treatment info in drawings, which means that someone opening up the part does not have all the information they need at hand.
I currently create a super thin extrude or revolve at the location of the surface treatment so that the boundary line is visible on the drawing. This is a bit of a hack.
There are locations on some parts that need a logo, or laser mark. Onshape currently has no way to apply a bitmap onto a surface.
These are the kinds of things I'm talking about.
Please hear what I am trying to convey with regards to 2D drawings so that we don't have any polite misunderstandings but rather some more good and productive thinking together... Don't let the shortcomings of a modeling tool drive us to ALWAYS need a 2D drawing to entirely convey what's needed. I think your post is right in line with this thinking. If we can think about a better modeling tool, then the user has better choices in front of them on whether just the model works in the current circumstance or whether a 2D drawing is also needed. Current packages have not given us enough choice and for that reason we are still using 2D drawings, when they might not really be needed in a lot of scenarios. Onshape has such wonderful potential to lead the way here in this realm for a lot reasons, one if which the viewer is inherent with the data. I would hate (and I think most everyone here) to see it nail it on the platform and come so close to getting it... but not quite there on the robustness of the model definition.
In SW, I use splits a lot to do what you're describing. I guess this maps to a trimmed surface definition which is basic geometry which all CAD systems should support. Hoping OS supports these operations soon.
Love the meta data attachment OOP scheme that you're talking about. I guess we could define the toString() method to call out the meta data associated with underlying geometry object.
The big picture, I don't think a standards committee getting their act together and pulling something like this off. I do see a small start up CAD company defining this system and industry using it. Much like DXF and the whole autodesk thing. Let's just hope it's a better standard than DXF.
If I wrote the code, would you try it?
Sounds great. I'll help with what I can.