Welcome to the Onshape forum! Ask questions and join in the discussions about everything Onshape.
First time visiting? Here are some places to start:- Looking for a certain topic? Check out the categories filter or use Search (upper right).
- Need support? Ask a question to our Community Support category.
- Please submit support tickets for bugs but you can request improvements in the Product Feedback category.
- Be respectful, on topic and if you see a problem, Flag it.
If you would like to contact our Community Manager personally, feel free to send a private message or an email.
More efficient: Sketch or solid patterns?
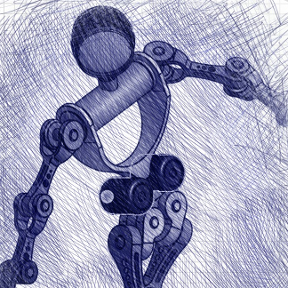
Best Answer
-
NeilCooke Moderator, Onshape Employees Posts: 5,891
They will be the same since STEP only looks at the final solid geometry.Senior Director, Technical Services, EMEA5
Answers
My extruded pentagon sketch is 17.2 KB while my chamfered rectangular extrusion is 16.2 KB. Likewise, an extruded hexagon sketch is 20.7 KB while a twice-chamfered rectangular extrusion is 18.7 KB. And an extruded heptagon sketch is 24.2 KB while a thrice-chamfered rectangular extrusion is 21.2 KB.
In all cases, the chamfers are specified to produce the same geometries as the extruded sketches. For every face added, chamfering saves you 1 KB over extruding a sketch. Why?
This may seem like splitting hairs, and it would be if I weren't dealing with very large patterns, where a difference of a few KB per extrusion can add up to MB in the final extruded part! Anyway, just trying to understand why chamfering seems more efficient when the exported geometry is by all appearances the same?
Also (this gets complicated): extruding a heptagon sketch with a filleted corner at 0.2" radius... beats filleting an edge of a thrice-chamfered rectangular extrusion at the same radius.
Sorry for the tongue twister.
The solid fillet adds 2.8 KB to the STEP file size while the sketch fillet adds 4 KB. Likewise, two 0.2" solid fillets add 10.1 KB while two 0.2" sketch fillets add 14 KB.
In all cases the solid and sketch fillets are specified to produce the same geometries. So with fillets too it seems solid features beat sketch features when it comes to STEP file size!
Chamfering a rectangular extrusion adds 2 KB while extruding a pentagon sketch adds 5.3 KB (relative to the plain rectangular extrusion). Twice-chamfering the rectangular extrusion adds 3.9 KB while extruding a hexagon sketch adds 9.4 KB. Thrice-chamfering the rectangular extrusion adds 5.8 KB while extruding a heptagon sketch adds 13.3 KB.
So with Parasolid too it seems chamfering solids beats adding sketch edges...