Welcome to the Onshape forum! Ask questions and join in the discussions about everything Onshape.
First time visiting? Here are some places to start:- Looking for a certain topic? Check out the categories filter or use Search (upper right).
- Need support? Ask a question to our Community Support category.
- Please submit support tickets for bugs but you can request improvements in the Product Feedback category.
- Be respectful, on topic and if you see a problem, Flag it.
If you would like to contact our Community Manager personally, feel free to send a private message or an email.
Booleans on parts with tangent surfaces
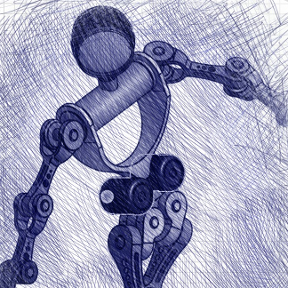
In the real world, I expect that if I lay one part on top of another so that their surfaces are tangent, then I can glue them or weld them together so that they are joined.
But this seems a difficult thing in Onshape. Much of the time, if surfaces or edges are tangent, then the Boolean fails. It seems silly to add 1/100th of an inch to artificially overlap the tangent surfaces just to get the Boolean to work.
Does anyone know why tangents are such a problem with Booleans? I avoid them where I can, but sometimes the parts to join just have to be tangent---like a panel to be welded on a beam or strut...
0
Comments
Could you give an example? If it is an edge-to-edge surface it should work. But if they are solid parts as Neil mentions, they do need some overlap.
Is there a way to make this very simple part with Onshape? It is part of the first project we teach our students.
A 2" cube with two 1" cubes removed from opposite corners. Yes, the innermost corners of the removed 1" cubes are coincident with the center of the 2" cube.
https://cad.onshape.com/documents/8dc4e04d4858db4f45e45234/w/7ac54befcfcb7332072f4dca/e/3c1f15195119d9bbe32d6b19
It is very easy to make in Fusion 360. I am sure there is a fundamental difference in the technologies and I understand there are always advantages and disadvantages.
But I really want to be able to make this part.
Onshape uses the Parasolid kernel, which means that all parts must follow Parasolid's rules.
When you try to cut the 1 inch parts out of the two inch parts, it will fail, since the very centre is non-manifold (There is no thickness between the opposite faces at that point)
IR for AS/NZS 1100
If you model two cubes and the only have one single edge that's coincident (as in one of the examples above), that's and infinitely small thing connecting the two cubes. To make such a thing in the real world would be physically impossible. Either the two cubes are connected by something that is measurable, or they're not (which would leave you with two disconnected cubes). The manifold constraints in the kernel are reflecting this physical reality.
Its hard to tell from your screenshot above if the boolean is failing in this same way - it looks like it may have been a different issue. Coincident faces shouldn't create any boolean issues.
@scott_garman232 - I tried looking at your document, but it looks like its been deleted or its not public.
Mention was made earlier in this thread of "welding" two cubes together where they meet at a point (corner). I don't believe that example is relevant because it relies entirely on the weld fillet to add nonzero contact area. You can't create a sound mechanical joint between two bodies that meet only at a singularity regardless of whether you're in the garage or using the parasolids kernel.
This is also why cross sections will sometimes fail - the cutting plane ends up being tangent to some hole or a similar issue.
Simon Gatrall | Staff Mechanical Engineer | Carbon, Inc.