Welcome to the Onshape forum! Ask questions and join in the discussions about everything Onshape.
First time visiting? Here are some places to start:- Looking for a certain topic? Check out the categories filter or use Search (upper right).
- Need support? Ask a question to our Community Support category.
- Please submit support tickets for bugs but you can request improvements in the Product Feedback category.
- Be respectful, on topic and if you see a problem, Flag it.
If you would like to contact our Community Manager personally, feel free to send a private message or an email.
Sheet Metal Move Face
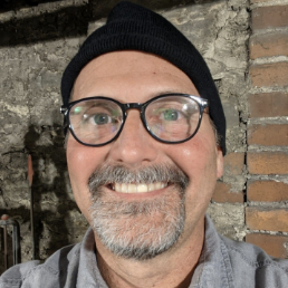
https://cad.onshape.com/documents/04c87755529dcde47d445aa1/w/04c2368ea7c2118167ab6eae/e/9de12eea9092b4c2a30c3d43
I'm struggling with moving a sheet metal face/edge. Look at the last two features in the feature tree. I need to pull all three of the sheet metal edges into the box. I can only pull one. Can anyone tell me why I can't move the other two? I moved the silhouetted face .75 but can't move the orange face the same amount. Maddening at this point......
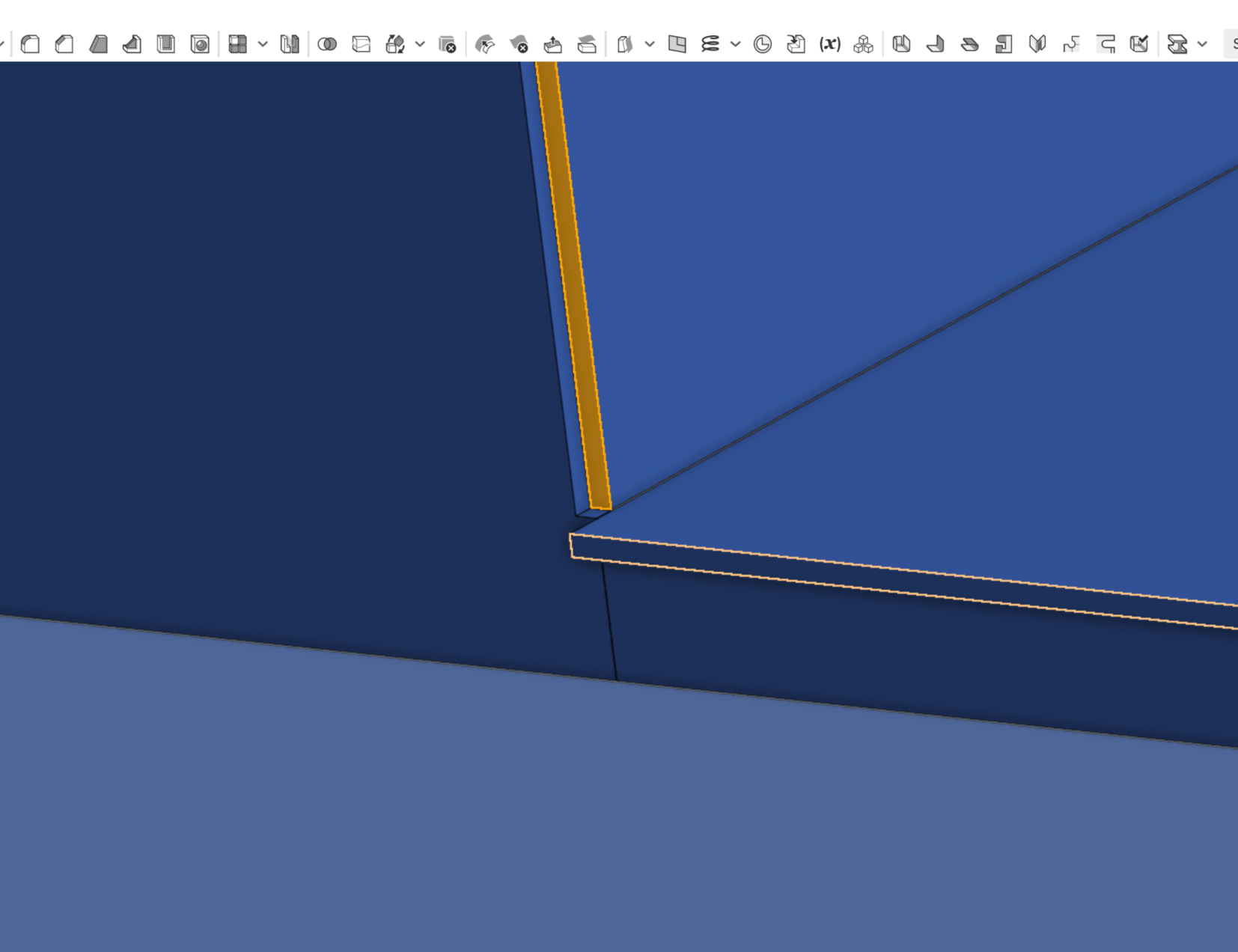
I'm struggling with moving a sheet metal face/edge. Look at the last two features in the feature tree. I need to pull all three of the sheet metal edges into the box. I can only pull one. Can anyone tell me why I can't move the other two? I moved the silhouetted face .75 but can't move the orange face the same amount. Maddening at this point......
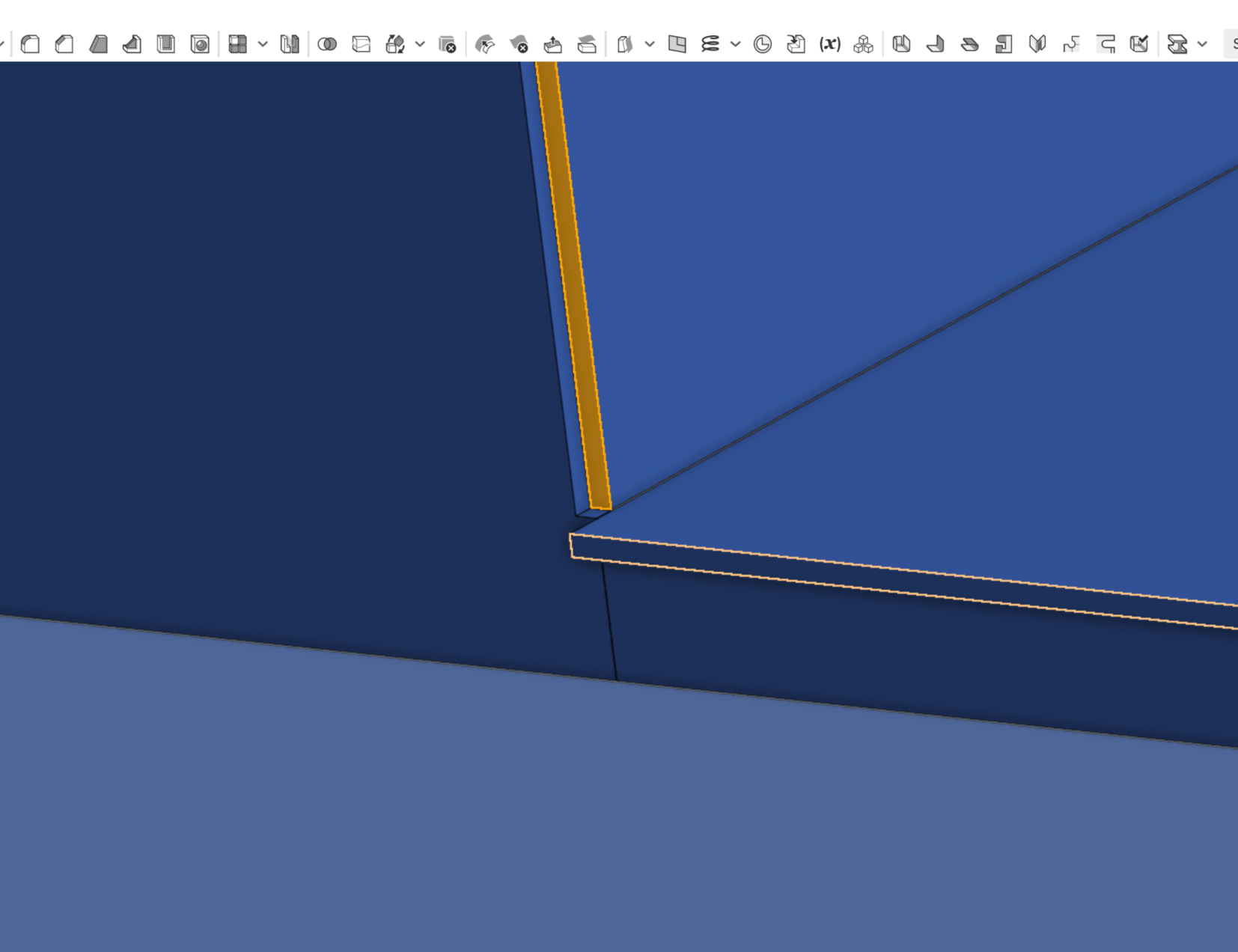
Tagged:
0
Comments
Once a part is sheet-metal, it gains a lot of restrictions that prevent you from making impossible sheet-metal parts.
Because you made everything sheet-metal from a single feature, it is treating it like a single piece of sheet-metal and is trying to make sure the corners have reliefs.
I would recommend not using sheet-metal for this part, because they are all flat pieces, with the exception of the curved ends. You could make those Sheet-metal.
If this was done with extruded faces, it would require considerable time to move/trim each edge for proper fitment. Something Onshape's sheet metal does automatically, neatly, and correctly.
https://cad.onshape.com/documents/bb8b8777c1b274bb25c0d4fd/w/5d55c34292bf0ef965cd271f/e/82933f2f186dc72191589388